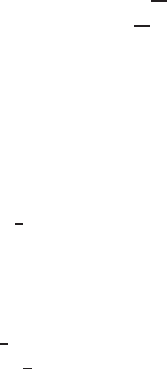
BOLTED CONNECTIONS 285
Cornell University in the 1950s to study the type of failure
caused by shearing of the bolt.
8.37,8.38
It was found that
the shear–tension strength ratio is independent of the bolt
diameter, and the ratios are equal to about 0.62 and 0.72
for double-shear and single-shear tests, respectively. In
view of the fact that the failure by shearing of the bolt
is more sudden than that in the sheets being connected,
a conservative shear-to-tension ratio of 0.6 has been used
in the past for both double- and single-shear conditions
in the development of design provisions, even though the
extremes of test values ranged from 0.52 to 1.0; that
is, the type of failure by shearing of the bolt occurs
at a strength equal to 0.6 times the tensile strength of
the bolt.
8.4.2 AISI Design Criteria for Bolted Connections
Based upon the results of tests summarized in Section 8.4.1
and past design experience, Section E3 and Appendix A of
the 2007 edition of the AISI North American Specification
includes a number of requirements for the design of bolted
connections in the United States and Mexico and are
summarized herein. Section E3 and Appendix B contain
the provisions for Canada.
8.4.2.1 Thickness Limitations On the basis of the same
reasons discussed in Section 8.3.2.1 for the design of
welded connections, Section E3 of the Specification is
applicable only to the design of bolted connections for cold-
formed steel members that are less than
3
16
in. (4.8 mm) in
thickness. For materials not less than
3
16
in. (4.8 mm), the
AISC specification
1.411
should be used for the design of
bolted connections in cold-formed steel structures.
8.4.2.2 M aterials Prior to 1980, the AISI design provi-
sions concerning the allowable shear stresses for mechan-
ical fasteners were limited to A307 and A325 bolts. Because
the maximum thickness for cold-formed steel members was
increased in 1977 from
1
2
in. (12.7 mm) to 1 in. (25.4 mm),
other high-strength bolts, such as A354, A449, and A490
bolts, were added to the 1980 specification for bolted
connections.
In view of the fact that A325 and A490 bolts are available
only for a diameter of
1
2
in. (12.7 mm) and larger, whenever
smaller bolts [less than
1
2
in. (12.7 mm) in diameter] are
required in a design, A449 and A354 Grade BD bolts
should be used as equivalents of A325 and A490 bolts,
respectively.
For other types of fasteners, which are not listed in
Section E3 of the AISI North American Specification, draw-
ings should indicate clearly the type and size of fasteners
to be employed and the design force.
8.4.2.3 Bolt Installation The requirement for bolt instal-
lation was added to the AISI Specification since 1980
to ensure that bolts are properly tightened according to
acceptable practice. Because the required pretension in bolts
usually varies with the types of connected part, fasteners,
applied loads, and applications, no specific provisions are
provided in the AISI North American Specification for
installation.
The effect of torques on the strength of bolted connec-
tions has been studied in the past and was reported in
Ref. 8.45.
8.4.2.4 Maximum Sizes of Bolt Holes The 1986 and
the 1996 editions of the AISI Specification include the
maximum sizes of standard holes, oversized holes, short-
slotted holes, and long-slotted holes, as shown in Table 8.4.
Standard holes should be used in bolted connections, except
that oversized and slotted holes may be used as approved
by the designer. Additional requirements are given in the
AISI North American Specification for the use of oversized
and slotted holes.
8.4.2.5 Shear, Spacing, and Edge Distance in Line of
Stress According to Section E3.1 of the AISI North
American Specification, the nominal shear strength, P
n
,of
the connected part as affected by spacing and edge distance
in the direction of applied force shall be calculated as
follows:
P
n
= teF
u
(8.51)
(a) When F
u
/F
y
≥ 1.08:
= 2.0 (ASD)
φ = 0.70 (LRFD)
(b) When F
u
/F
y
< 1.08
= 2.22 (ASD)
φ = 0.60 (LRFD)
where P
n
= nominal resistance per bolt
e = distance measured in line of force from
center of standard hole to nearest edge of
adjacent hole or to end of connected part
t = thickness of thinnest connected part
F
u
= tensile strength of connected part
F
y
= yield stress of connected part
Equation (8.51) was derived from Eq. (8.45) in Section
8.4.1.1. The above design equation is the same as that used
in previous editions of the AISI specification, except that
the limiting F
u
/F
y
ratio was reduced in 1996 from 1.15