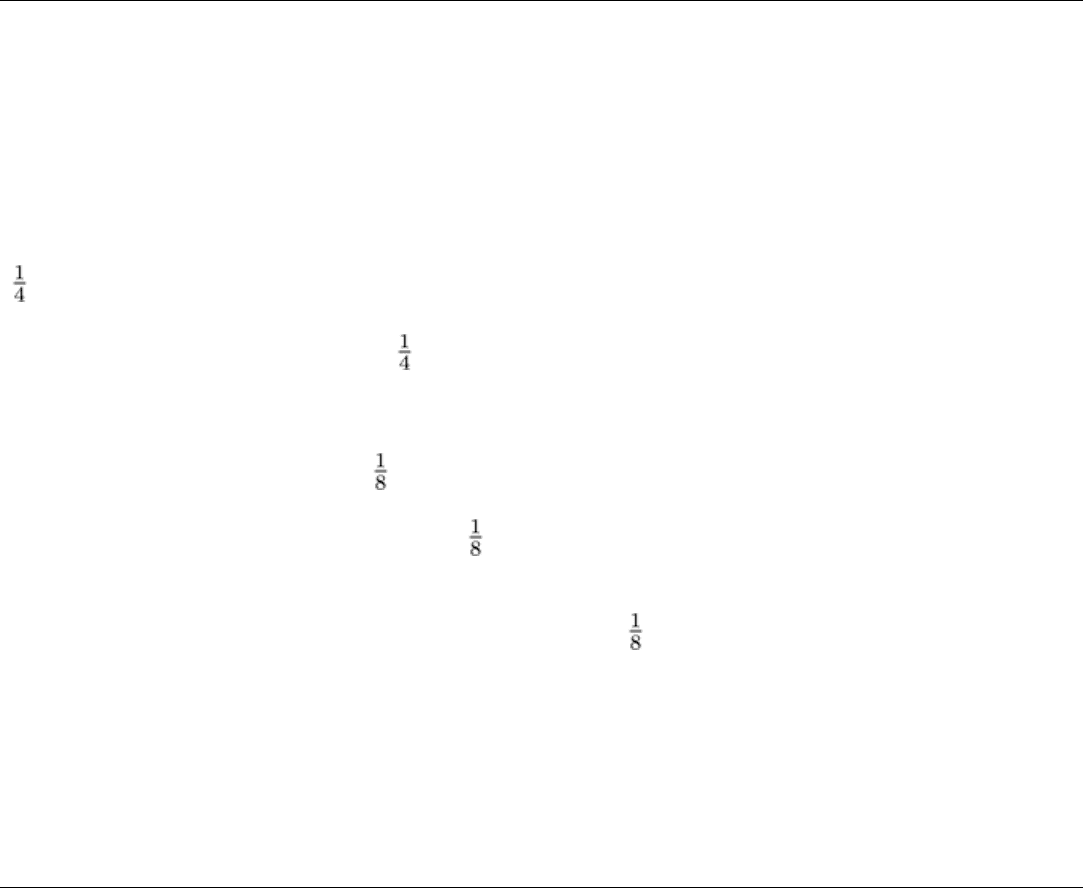
To achieve high productivity and low unit cost, most blanking is done in high-speed mechanical presses. Speeds as high
as 1200 strokes per minute are used. The equipment for high-speed blanking ordinarily includes a short-stroke press,
automatic feed devices, and dies designed for bottom ejection.
In most blanking operations, press speed is limited by the length of feed, which is governed by blank size, or by the
relationship between the force capacity of the press and the load. The combination of blanking with forming or drawing in
compound dies also restricts press speed. Blanking speed may be as low as ten strokes per minute in producing blanks
that are extremely large or that present handling problems for other reasons.
Regardless of the number of strokes per minute, the velocity of the punch always approaches zero near the bottom of the
stroke. Within the usual range for production work in conventional blanking dies, the speed of the press has little practical
effect on the speed of the punch during the blanking portion of the stroke. This effect, however, is critical for fine edge
blanking, in which punch speed during the interval while the punch is cutting through the work metal is usually about 7.6
to 1.5 mm/s (0.3 to 0.6 in./s) (see the article "Fine Edge Blanking and Piercing" in this Volume).
Lubrication requirements are generally less critical for blanking than for forming or deep drawing; stock to be blanked
is often fed into the press with no lubrication other than the residue remaining on the stock from the lubrication at the
mill. The stock is sometimes coated with a light mineral oil or a light chlorinated oil. However, lubrication is important in
dies that have close clearance between punches and stripper. At speeds of 40 strokes and more per minute, such dies must
be lubricated constantly with a spray of light mineral oil to prevent galling of the punches in the stripper. Additional
information on lubrication requirements in blanking is available in the article "Selection and Use of Lubricants in
Forming of Sheet Metal" in this Volume.
Blanking of Low-Carbon Steel
Effect of Work Metal Thickness
Stock thickness affects the selection of material for dies and related components, as well as the selection of die type and
design. The amount of shear and relief (angular clearance or draft) built into a blanking die and the amount of clearance
between punch and die all depend on blank thickness.
Work metal thickness is also a factor in the selection of blanking method, handling procedure, and handling equipment.
Blanking in a punch press is usually the fastest and most economical way of producing blanks thinner than about 6.4 mm
( in.) in medium or large quantities.
Plate stock, in thicknesses of 6.4 to 25 mm ( to 1 in.), is less frequently blanked in presses than sheet or strip. Blanks of
such thick material are often made by gas cutting, sawing, nibbling, or routing instead of by shearing or by press
operations; selection of the method depends primarily on plate thickness and production quantity.
Almost all blanks thinner than 3.2 mm ( in.), except for intricate shapes chemically blanked from foil, are produced
with conventional dies in mechanical or hydraulic presses. In only two of the examples of commercial practice presented
in this article was work metal thicker than 3.2 mm ( in.) (Example 3: 3.96 mm, or 0.156 in., and Example 9: 4.75 mm,
or 0.187 in.).
Because of its strength and rigidity, material thicker than 3.2 mm ( in.) is seldom blanked from coil stock or in a
progressive die. On the other hand, because of its lack of strength and extreme flexibility, material thinner than 0.51 mm
(0.020 in.) generally requires special handling techniques. The articles "Piercing of Low-Carbon Steel," "Blanking and
Piercing of Electrical Steel Sheet," and "Press Forming of High-Carbon Steel" in this Volume contain additional
information on the effect of work metal thickness on processing.
Distortion is often a problem in blanking complex shapes from thin low-carbon steel sheet by repeated strokes of a
notching die. Distortion of such parts can be minimized by the use of hardened stock and by performing the entire
blanking operation in one stroke in a single die.
Blanking of Low-Carbon Steel