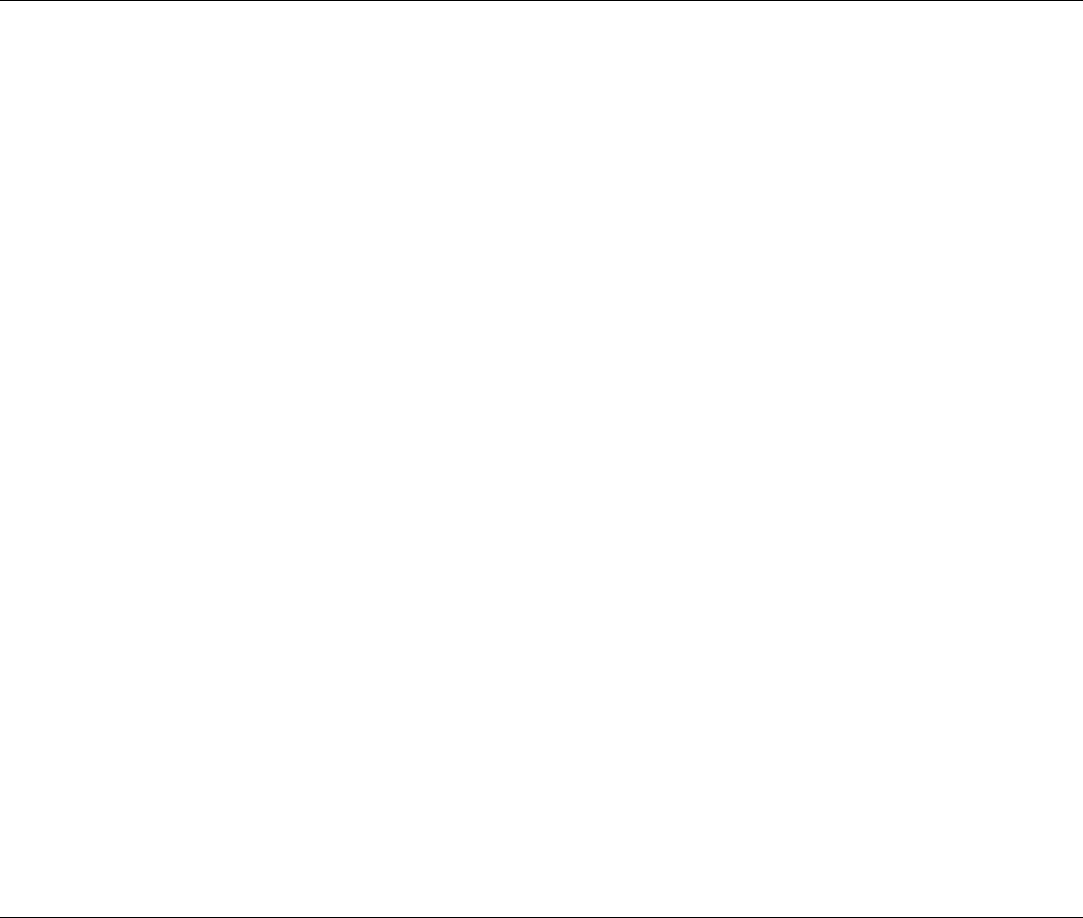
In simplified practice, some plants ignore partial shear in calculating cutting force for blanking. When full shear is used,
force is calculated as without shear and then reduced by 30%.
Stripping force is the force needed (when drop-through is not used) to free the blank from the die or the strip from the
punch when they stick or jam because of springback. Stripping force can be calculated using:
L
st
= kA
(Eq 4)
where L
st
is the stripping force (in pounds), k is a stripping constant (in pounds per square inch), and A is the area of the
cut surface (in square inches) (stock thickness t multiplied by length or perimeter of cut l). Approximate values for the
constant k (as determined by experiment for low-carbon steel) are:
• 1500 for sheet metal thinner than 1.57 mm (0.062 in.) when the cut i
s near an edge or near a preceding
cut
• 2100 for other cuts in sheet thinner than 1.57 mm (0.062 in.)
• 3000 for sheet more than 1.57 mm (0.062 in.) thick
Blanking of Low-Carbon Steel
Factors That Affect Processing
Factors that affect the processing of blanks include the following:
• Size and shape of the blank
• Material for blanking
• Form in which the material is supplied
• Thickness of the blank
• Production quantity and schedule
• Quality specifications
• Availability of equipment and tools
• Number and type of subsequent operations required for completing the work
The size and shape of the blank affect the form and handling of the material blanked, the blanking method, and the
handling of the completed blank. The thickness of the blank affects the press load required (see the section "Calculation
of Force Requirements" in this article), the selection of equipment, and the choice of blanking and handling methods (see
the section "Effect of Work Metal Thickness" in this article).
Production quantity and schedule determine the choice of equipment. A total production of fewer than 10,000 pieces is
considered a short run; 10,000 to 100,000 pieces, a medium run; and more than 100,000 pieces, a long run.
Quality specifications and tolerances for thickness, camber, width, length, flatness, and finish affect the handling of the
material. The availability of single-, double-, or triple-action presses (rated at various force capacities, sizes, speeds,
lengths of stroke, strokes per minute, and shut heights) affects the selection of the processing method. The availability and
capacity of auxiliary press equipment can have an effect on the selection of a tooling system and on whether a part can be
made in-plant.
Operations that follow blanking also affect the choice of equipment, the processing method, and the handling procedures.
Such subsequent operations may include piercing, bending, forming, deep drawing, machining, grinding, or finishing.
Only rarely is the blank a final product.
Blanking of Low-Carbon Steel
Selection of Work Metal Form