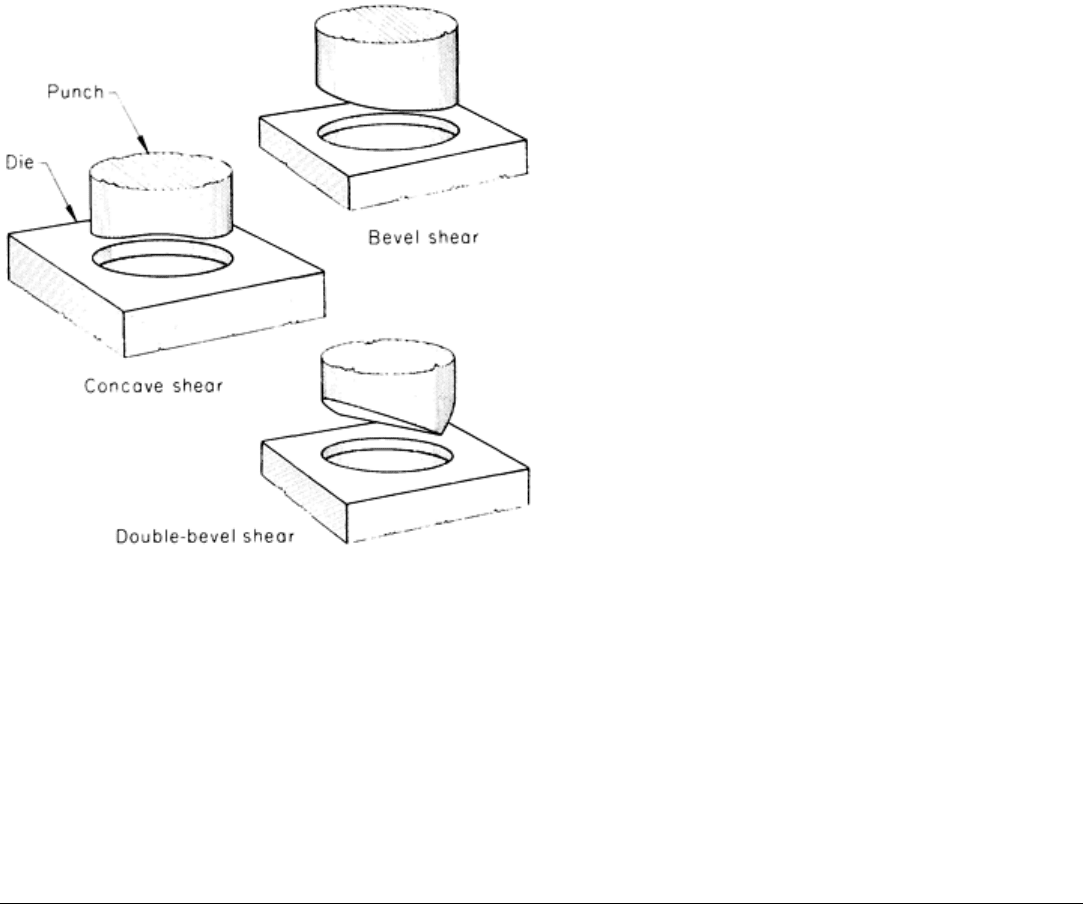
Effect of Punch Shear. Shear is the amount of relief ground on the face of a punch (Fig. 5). It is used to reduce the
instantaneous total load on the tool and to permit thicker or higher-strength materials to be pierced in the same press. It
distributes the total piercing load over a greater portion of the downstroke by introducing the cutting edge in increments
rather than instantaneously.
Piercing force (but not contact edge pressure or total
work done) varies with the amount of shear on the
punch face. With the bottom of the punch flat and
parallel to the face of the die, piercing takes place on
the entire periphery at once, requiring maximum force.
The load on the press and tools increases rapidly to a
maximum after impact and then releases suddenly
when piercing is completed. By grinding shear on the
punch as shown in Fig. 5, the maximum load is
decreased, but the punch travels correspondingly
farther to complete the piercing. Load release is also
somewhat less sudden.
Shear location is ordinarily selected so as to confine
distortion to the scrap metal (slug). Thus, in piercing,
shear is ground on the punch because the punched-out
metal is to be scrap. Concave shear and double-bevel
shear (Fig. 5) provide a balanced load on the punch.
Scalloped shear, sometimes ground on round punches,
also provides a balanced load on the punch. An
unbalanced load may cause deflection and tool
breakage or excessive wear.
The amount of shear is determined by trial. However,
shear equal to one-third of stock thickness (t/3) will
reduce piercing force about 25%, and shear equal to
stock thickness will reduce piercing force about 50%.
Shear can be applied to punches for large holes but not
to small-diameter punches, because they lack column
strength.
When a number of small holes are being pierced and the press load must be reduced, the punches can be ground to
different lengths. This enables the punches to start cutting at different times and reduces the maximum load. In selecting a
press, it should be noted that the reduction in maximum impact load on the press achieved by staggering punch length or
by using shear is not sufficient to enable the use of a press that is significantly lower in tonnage rating, strength, or
rigidity.
Piercing of Low-Carbon Steel
Presses
Presses used in piercing are the same as those used in other pressworking operations. Open-back gap-frame presses of the
fixed upright, fixed inclined, or inclinable type are common. The stock can be fed from the side with minimal interference
from the press frame, and the parts can be removed from the front by the operator or ejected out the back by gravity or air
jets.
Adjustable-bed or horn presses are used for piercing holes in tubing and in the sides of drawn or formed shells and boxes.
Adjustable-bed and gap-frame presses are generally rated at capacities of less than 1.8 MN (200 tonf).
Straight-side presses are commonly used for compound-die and progressive-die operations. Increased accuracy, speed,
and stability are required for these operations.
Fig. 5 Three types of shear on pierci
depth of shear are exaggerated for emphasis.