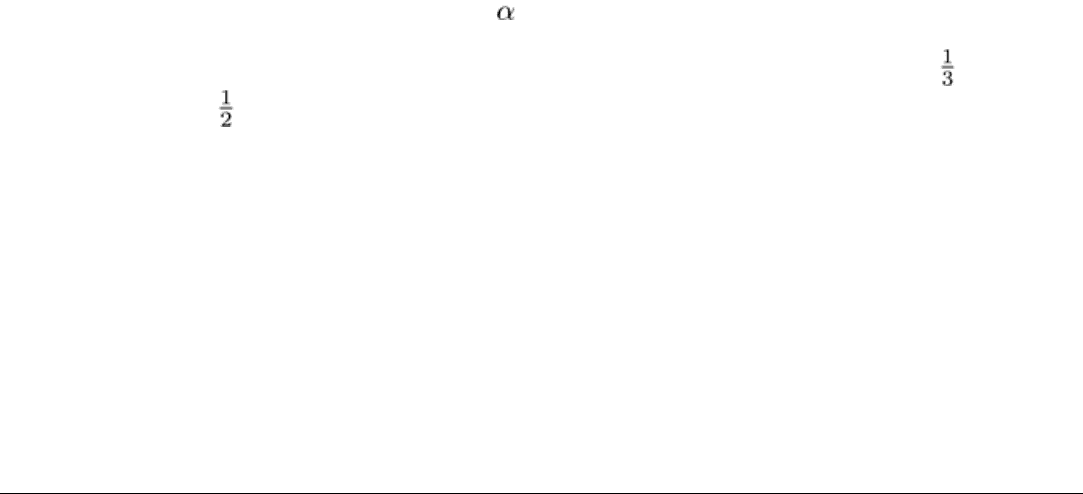
where 0.01745 is a factor to convert degrees to radians; is the included angle to which the metal is bent (in degrees); r is
the inside radius of the bend (in inches); and k is the distance of neutral plane or axis from the inside surface at the bend
expressed as the fraction of the metal thickness, t, at the bend. Empirically determined values of k are: , for bends of
radius less than 2t; and , for bends of greater radius. Sample calculations showing the use of Eq 3 are presented in the
article "Contour Roll Forming" in this Volume.
Permissible bend radii depend mainly on the properties of the work metal and on tool design. For most metals, the
ratio of minimum bend radius to thickness is approximately constant, because ductility is the primary limitation on
minimum bend radius. Another complicating factor is the effect of work hardening during bending, which will vary with
metal and heat treatment.
Condition of Machines and Tools. Machines and tools must be kept in the best possible condition for maintaining
close dimensions in the finished product. General-purpose tooling is seldom built for precision work and is frequently
given hard use, which contributes further to inaccuracy through wear. Uneven wear aggravates the condition. If the press
brake has been allowed to become loose and out-of-square and if ram guides and pitman bearings are worn, accurate work
cannot be produced. Good maintenance is as essential in successful press-brake operation as in any other mechanical
process.
Press-Brake Forming
Press-Brake Forming Versus Alternative Processes
For many applications, press-brake forming is the only practical method of producing a given shape. In one case, for
example, press-brake forming was used for a massive workpiece 3 to 3.7 m (10 to 12 ft) long that required several bends
spaced at least 152 mm (6 in.) apart.
Under certain conditions, either a punch press or a contour roll former will compete with a press brake in performance
and economy. When a workpiece can be produced by two or all of these methods, the choice will depend mainly on the
quantity to be produced and the availability of the equipment.
Press Brake Versus Punch Press. When a given workpiece can be made to an equal degree of acceptability in either
a press brake or a punch press, the punch press is usually more economical, and it is more efficient than the press brake in
terms of power requirements for a given force on the ram and number of strokes per unit of time. In addition, air ejection
is more readily adapted to a punch press than to a press brake; this is a factor when air is required for ejecting either the
workpiece or scrap.
The advantages of a punch press over a press brake are generally greater when production quantities are large and
workpieces are relatively small. As workpiece size increases, the advantages of a punch press diminish.
Tooling for a press brake is usually simpler and less costly than counterpart tooling for a punch press--an important
consideration for small production quantities. One disadvantage of punch presses is that they are more sensitive to
thickness variations of the work metal because they operate at a faster rate.
Press-Brake Versus Contour Roll Forming. For many parts usually formed in a press brake, contour roll forming
is an acceptable alternative method of production, and the choice between the two processes depends mainly on the
quantity to be formed. Press-brake forming is adaptable for quantities ranging from a single piece to a medium-size
production run, while contour roll forming is usually restricted to large-quantity production because of higher tooling
costs. An advantage of contour roll forming is that coil stock can be used, while cut-to-length stock must be used in a
press brake (see the article "Contour Roll Forming" in this Volume). The following example compares the efficiency of
press-brake forming and contour roll forming.
Example 8: Press-Brake Forming Versus Contour Roll Forming.
Parts were produced to the shape shown in Fig. 24 in lengths up to 3.7 m (12 ft) and widths varying from 0.30 to 1.5m (12
to 60 in.). The six bends were originally made in a press brake in three operations. When quantity requirements increased,
production was changed to contour roll forming in a tenstation machine, from sheared-to-size sheets. Contour roll