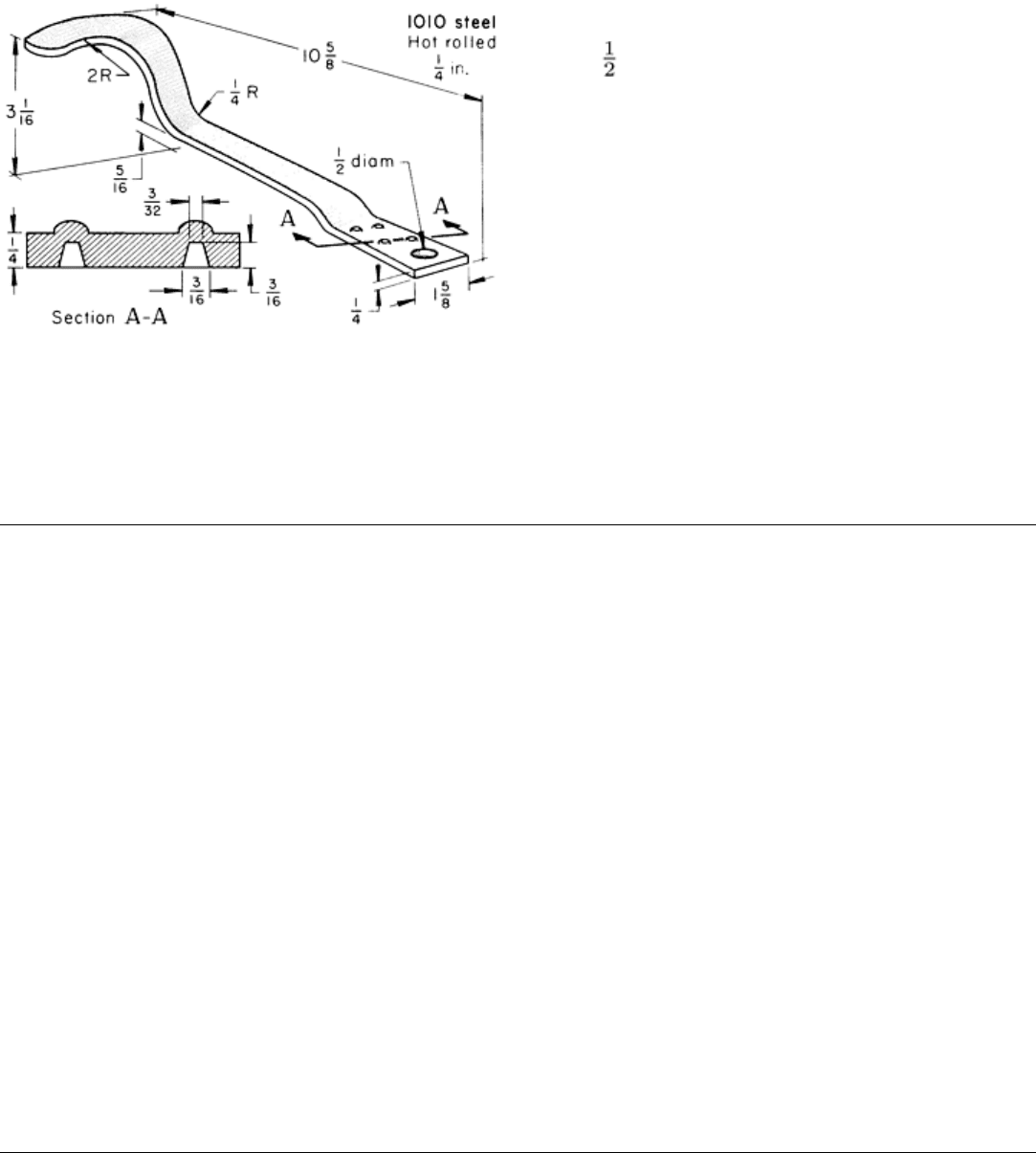
Each blank was edge bent to a 50 mm (2 in.) radius at
the narrow end. Other operations included bending the
offset and making the two other bends, piercing the 13
mm ( in.) diam hole, extruding four weld projections
(section A-A, Fig. 14), and trimming the radius on the
small end. The cutting and forming sections of the dies
were made of air-hardened tool steel.
The stock was cut to length in an 1100 kN (120 tonf)
end-wheel press (mainshaft extending front-to-back)
operating at 60 strokes per minute. Edge bending,
forming, trimming, and piercing were done by separate
dies in a 1700 kN (190 tonf) open-back inclinable press
at 30 pieces per minute.
Limitations. The size of the offset radii, the length and
depth of the offset, and the location of the offset with
respect to the flanges may preclude the edge bending of
a rectangular blank. The potential cracking and thinning
of the outer edge and the wrinkling of the inner edge
make the use of a blanked shape more practical.
Press Bending of Low-Carbon Steel
Straight Flanging
Flange bending (flanging) in a wiping die is similar to the cantilever loading of a beam. To prevent movement during
bending, the workpiece is clamped to the die by a pressure pad before the punch contacts the workpiece. The bend axis is
parallel with the edge of the die.
Flanging dies are often cam actuated, with an accompanying loss of efficiency. Hold-down pads must be used, adding
further to the press capacity requirement. Considering all factors, the press capacity for flanging in a wiping die may be
up to ten times that for forming a similar length of bend in a V-die with a spacing of at least eight times the thickness of
the work metal.
In some operations, only single flanges are bent. More often, more than one flange is bent at a time, as in Examples 3, 9,
12, and 13. Dies can be simple V-dies, U-dies, wiping dies, or complex flanging dies such as shown in Fig. 8.
Even when fairly close tolerances must be held, simple V-dies can be used to make a complex part if production is low.
Flanging dies are more expensive than ordinary press-brake dies, but considering the time and labor saved in making
simple flanged pieces in flanging dies, they often pay for themselves quickly.
Hemming is an operation in which flanges are flattened against the workpiece in 180° bends to make a finished or
reinforced edge. If the flange to be hemmed has been bent somewhat more than 90°, the hemming die can be a simple flat
bed or anvil and a simple flat punch. Flanging and hemming can both be done in one press in a compound die, as shown
in Fig. 9.
Press Bending of Low-Carbon Steel
Bending of Curved Flanges
When a flange has concave curvature, the metal in the flange is in tension, and the flange is called a stretch flange (Fig.
15a). When the curvature is convex, the metal in the flange is in compression, and the flange is called a shrink flange
(Fig. 15b). The amount of tension or compression in either type of flange increases from the bend radius to the edge of the
flange. Excessive tension in a concave (stretch) flange causes cracks and tears; excessive compression in the convex
(shrink) flange causes wrinkles.
Fig. 14
Pedal lever that was edge bent to save metal and
to increase the strength of the part.
inches.