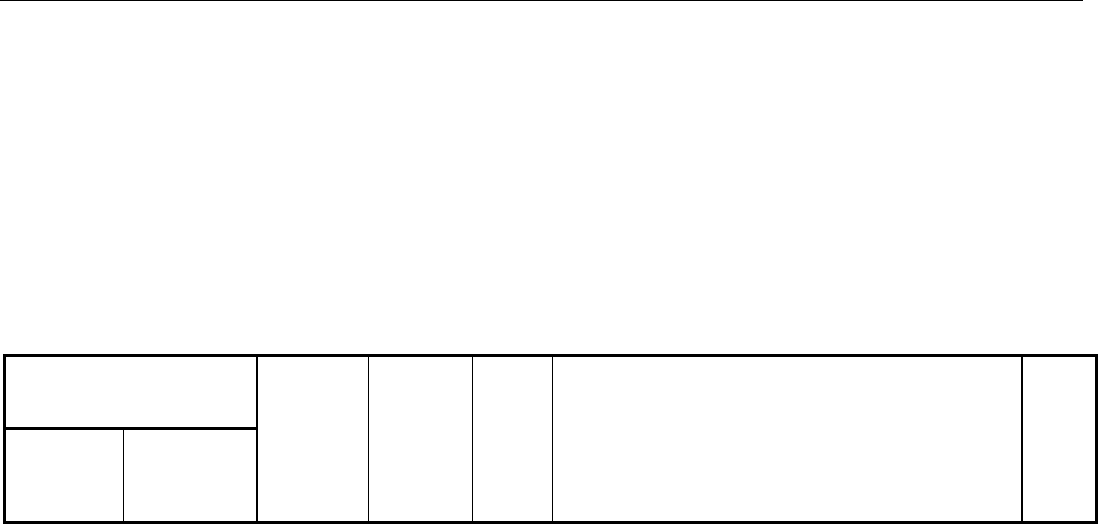
overloading. However, overloading should not be encouraged, because serious damage to the press brake may occur from
improper setup. Another advantage is that operating speeds are greater in mechanical press brakes than in hydraulic press
brakes. The greater speed is especially useful for long-run production of workpieces that are easily handled. Greater speed
also permits instantaneous, high impact forces when the punch contacts the work metal. This impact force is useful in
some operations, although it can damage the machine if the setup lacks rigidity.
A disadvantage of a mechanical press brake is that the stroke cannot be adjusted or controlled to the same degree as is
possible with the hydraulic type. However, mechanical press brakes are available at additional cost with devices that
permit a rapid advance to work and then a slower speed during forming.
Hydraulic Press Brakes. The ram of a hydraulic press brake is actuated by two double-acting cylinders, one at each
end of the ram. Force supplied by the hydraulic mechanism will not exceed the press rating; therefore, it is almost
impossible to overload a hydraulic press brake. (When thicker metal is inadvertently used, the ram stalls.) Therefore,
frames can be lighter and less costly than those for mechanical press brakes, which are subject to overloading.
In hydraulic press brakes, length of stroke and location of the top and bottom of the stroke (within limits of the cylinder
length) are adjustable. The point of rapid advance and return of the ram and its speed during contact with the workpiece
are also adjustable; this adjustment makes possible a dwell period, which is often helpful in controlling springback.
Cycles established by means of the various adjustments are reproduced by switches in the control circuit.
Even though devices are available that permit some control of the stroke of a mechanical press brake, the degree of
control that is possible for a hydraulic press brake is considerably greater. For example, the ram on a hydraulic press
brake can be reversed or its speed can be changed at any point on the stroke. Because of these features, a hydraulic press
brake is often preferred for the segmental forming of stock longer than the dies, for the forming of large sheets that would
be likely to whip in a mechanical press brake, and for the forming of difficult-to-form metals.
Hybrid press brakes incorporate both mechanical and hydraulic elements in the ram drive. The hydraulic-mechanical
hybrid consists of a mechanical press brake driven by a rotary hydraulic motor. Containing a vane that rotates 270°
between stops, the rotary hydraulic motor has replaced the piston used in a hydraulic cylinder. As it moves between the
two stops, the motor propels the eccentric shaft through one complete cycle, driving the ram to the stroke bottom and
back to the top.
The hybrid press brake combines the best features of both mechanical and hydraulic press brakes. It offers the same
accuracy and operating speeds obtainable with the mechanical press brake while providing the adjustable length and
controllability of the hydraulic press brake.
Press-Brake Forming
Selection of Machine
A mechanical press brake is usually preferred for quantity production because its speed is greater than that of a hydraulic
press brake. Conversely, a hydraulic press brake is generally preferred for varied short-run production because it is more
versatile.
Apart from the method of actuating the ram, major factors that must be considered in the selection of a press brake for a
given application are the size, length of stroke, and tonnage capacity of the press brake. Table 1 lists capacities and other
details for mechanical and hydraulic press brakes.
Table 1 Capacities, sizes, speeds, and ratings for mechanical and hydraulic press brakes
Capacity
Mid stroke Near bottom
of stroke
Bed length
Stroke
length
Speed
strokes
per
min
Bending capacity, m (ft), with standard stroke
for low carbon steel with thickness of:
Motor,
hp