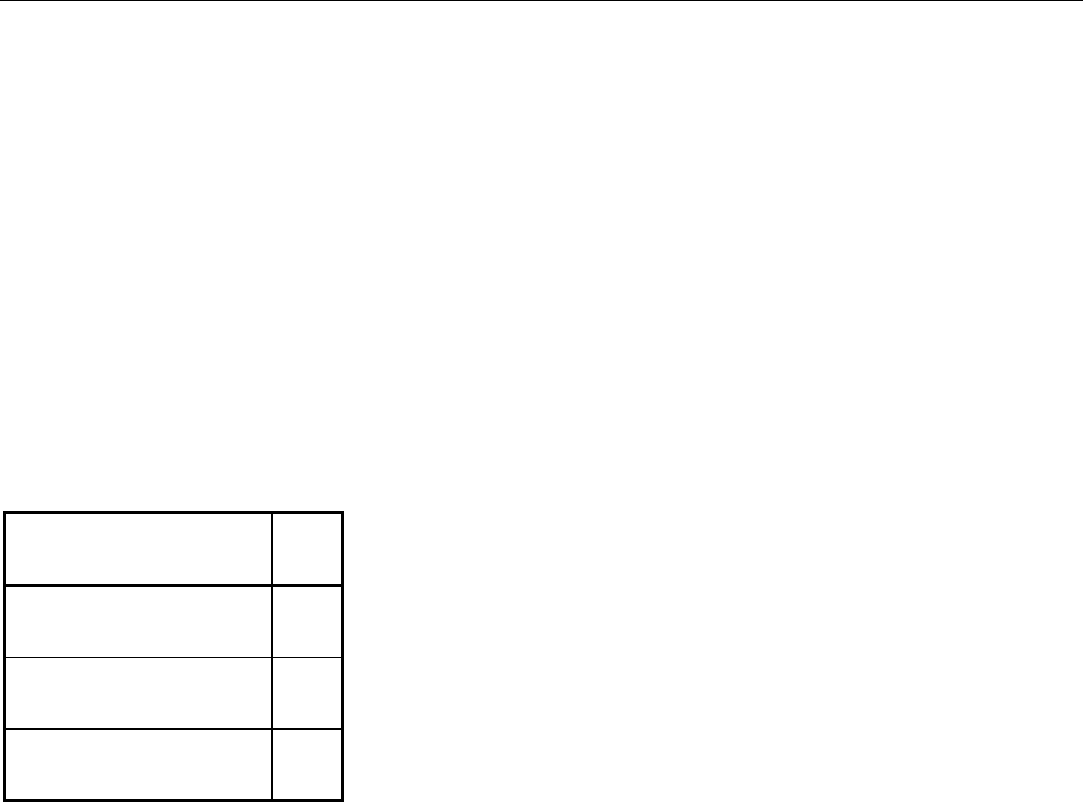
pressure. (c) Modified channel, with partial air bending. (d) Acute-angle channel.
obtained by using a conforming rubber die pad and deflector bars.
Urethane rubber is the type most widely used. Pads inserted into the bottom of the die can be used for forming V and
channel sections in various metals ranging from soft aluminum to low-carbon steel up to 12 gage (2.657 mm, or 0.1046
in.) in thickness. When using the urethane-pad technique, the urethane is, in effect, the die. It is almost impossible to
compress urethane; its shape changes but not its volume. With minimum penetration of the punch, the pad begins to
deflect, exerting continuous forming pressure around the punch. At the bottom of the stroke, the urethane has assumed the
shape of the punch. When the pressure is released, the pad returns to its original shape.
Urethane pads are generally used for short-run production. However, in one plant, 14,000 boiler-casing channels were
formed from 16 gage (1.52 mm, or 0.0598 in.) low-carbon steel in 4.9 m (16 ft) lengths on the same urethane pad before
replacement.
Urethane rubber is made in several different grades ranging in tensile strength from 18 to 76 MPa (2600 to 11,000 psi)
and in hardness from Durometer 80A to 79D. (Additional information is available in the article "Miscellaneous Hardness
Tests" in Mechanical Testing, Volume 8 of ASM Handbook, formerly 9th Edition Metals Handbook.) Selection of grade
depends on work metal hardness and thickness and on severity of forming. Experimentation is often needed to determine
the optimal grade of urethane for the application.
Work Metal Finish. When preservation of work metal finish is a primary objective, the dies or punches or both are
sometimes chromium plated. Other means of preserving the work metal finish include the use of oil-impregnated paper
between the tools and the work metal, or spraying the tools with a plastic of the type used to coat metal sheets for deep
drawing.
Press-Brake Forming
Procedures for Specific Shapes
Procedures and tooling for press-brake operations vary widely and are mainly influenced by workpiece shape. The
following examples describe the procedures used for producing several different shapes, including simple boxlike parts,
panels, flanged parts, architectural columns, fully closed parts, and semicircular parts.
Example 2: Four-Stroke Forming of Closed-Bottom Boxes From Notched Blanks.
Closed-bottom boxes were produced from 1010 steel blanks sheared to 508 × 610 mm (20 × 24 in.) in a press brake. The
four corners were notched to a depth of 102 mm (4 in.) in a standard notching die in the same press brake as that used to
make the blanks. The box was then formed in four strokes of the press brake, using a standard 90° V-die but with a
deeper-than-normal punch (Fig. 18). By bending the 305 mm (12 in.) sides first, all four bends could be made with a die
406 mm (16 in.) long. Hourly production rates for the three operations were:
Operation
Pieces
Shear blanks
55
Notch corners (four strokes)
57
Bend from sides (four strokes)
44