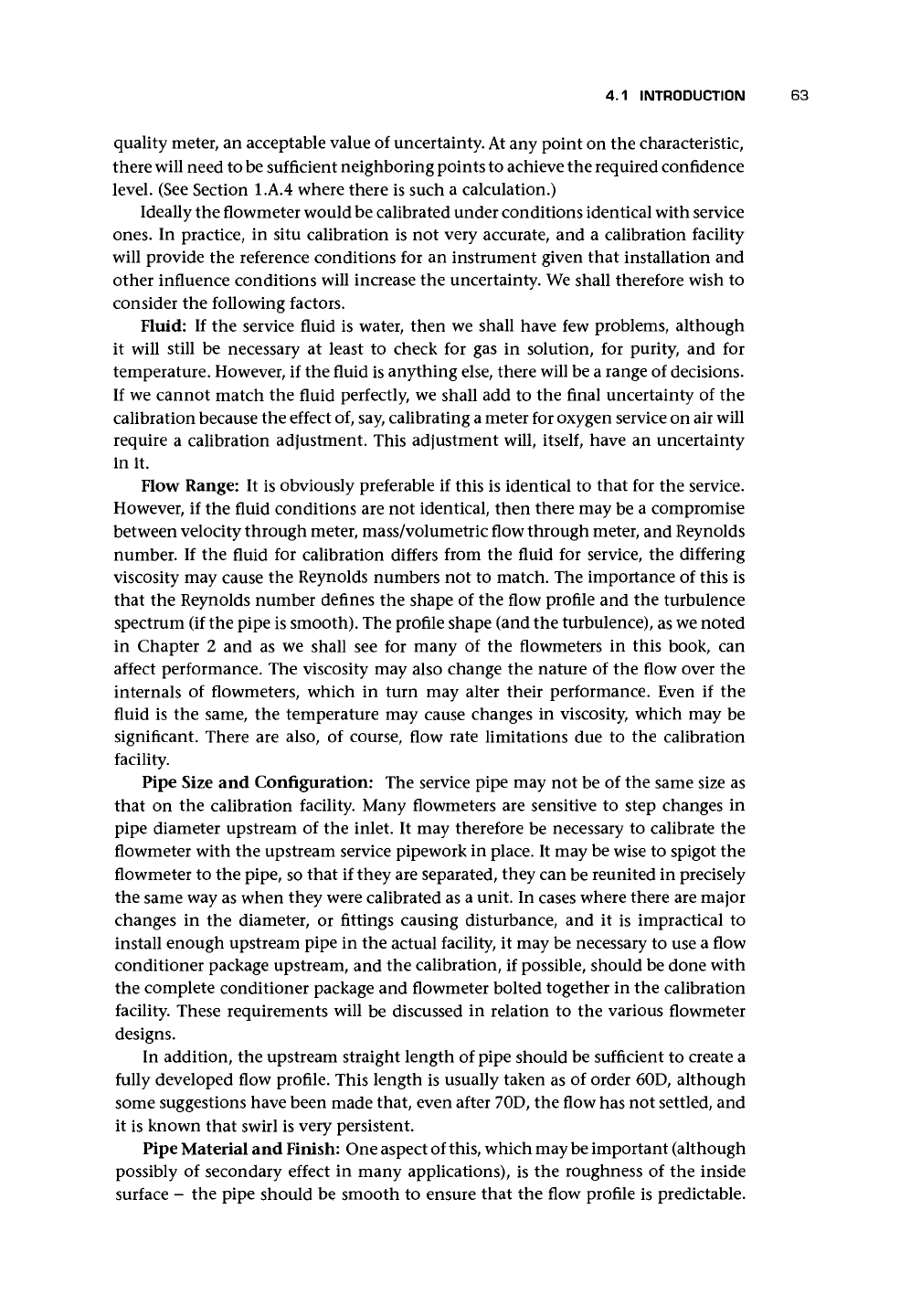
4.1 INTRODUCTION 63
quality meter, an acceptable value of uncertainty. At any point on the characteristic,
there will need to be sufficient neighboring points to achieve the required confidence
level. (See Section 1.A.4 where there is such a calculation.)
Ideally the flowmeter would be calibrated under conditions identical with service
ones.
In practice, in situ calibration is not very accurate, and a calibration facility
will provide the reference conditions for an instrument given that installation and
other influence conditions will increase the uncertainty. We shall therefore wish to
consider the following factors.
Fluid: If the service fluid is water, then we shall have few problems, although
it will still be necessary at least to check for gas in solution, for purity, and for
temperature. However, if the fluid is anything else, there will be a range of decisions.
If we cannot match the fluid perfectly, we shall add to the final uncertainty of the
calibration because the effect of, say, calibrating a meter for oxygen service on air will
require a calibration adjustment. This adjustment will,
itself,
have an uncertainty
in it.
Flow Range: It is obviously preferable if this is identical to that for the service.
However, if the fluid conditions are not identical, then there may be a compromise
between velocity through meter, mass/volumetric flow through meter, and Reynolds
number. If the fluid for calibration differs from the fluid for service, the differing
viscosity may cause the Reynolds numbers not to match. The importance of this is
that the Reynolds number defines the shape of the flow profile and the turbulence
spectrum (if the pipe is smooth). The profile shape (and the turbulence), as we noted
in Chapter 2 and as we shall see for many of the flowmeters in this book, can
affect performance. The viscosity may also change the nature of the flow over the
internals of flowmeters, which in turn may alter their performance. Even if the
fluid is the same, the temperature may cause changes in viscosity, which may be
significant. There are also, of course, flow rate limitations due to the calibration
facility.
Pipe Size and Configuration: The service pipe may not be of the same size as
that on the calibration facility. Many flowmeters are sensitive to step changes in
pipe diameter upstream of the inlet. It may therefore be necessary to calibrate the
flowmeter with the upstream service pipework in place. It may be wise to spigot the
flowmeter to the pipe, so that if they are separated, they can be reunited in precisely
the same way as when they were calibrated as a unit. In cases where there are major
changes in the diameter, or fittings causing disturbance, and it is impractical to
install enough upstream pipe in the actual facility, it may be necessary to use a flow
conditioner package upstream, and the calibration, if possible, should be done with
the complete conditioner package and flowmeter bolted together in the calibration
facility. These requirements will be discussed in relation to the various flowmeter
designs.
In addition, the upstream straight length of pipe should be sufficient to create a
fully developed flow profile. This length is usually taken as of order 60D, although
some suggestions have been made that, even after 70D, the flow has not settled, and
it is known that swirl is very persistent.
Pipe Material and
Finish:
One aspect of
this,
which may be important (although
possibly of secondary effect in many applications), is the roughness of the inside
surface - the pipe should be smooth to ensure that the flow profile is predictable.