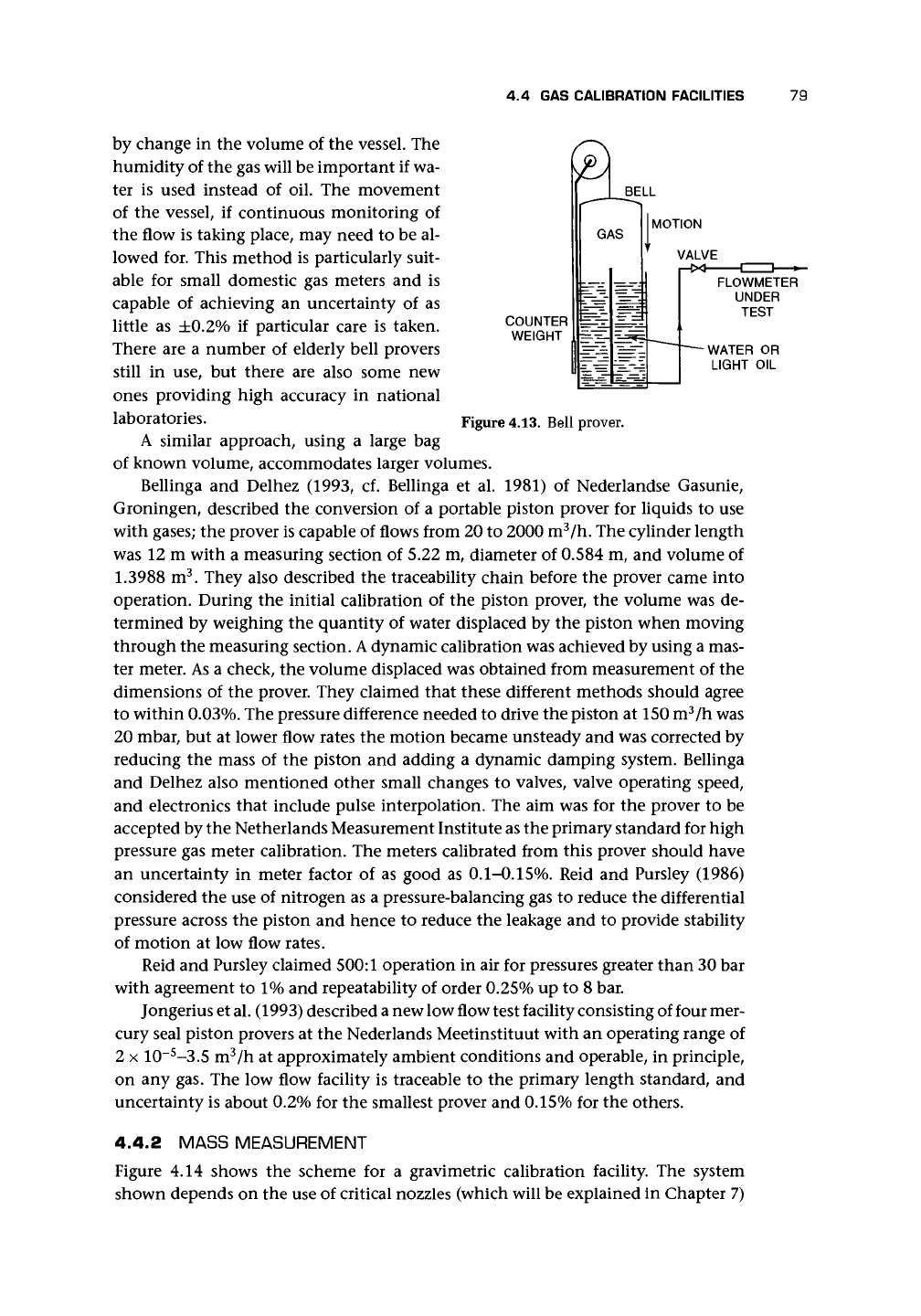
4.4 GAS CALIBRATION FACILITIES
79
COUNTER
WEIGHT
GAS
MOTION
VALVE
Figure 4.13. Bell prover.
by change in the volume of the vessel. The
humidity of the gas will be important if wa-
ter is used instead of oil. The movement
of the vessel, if continuous monitoring of
the flow is taking place, may need to be al-
lowed for. This method is particularly suit-
able for small domestic gas meters and is
capable of achieving an uncertainty of as
little as ±0.2% if particular care is taken.
There are a number of elderly bell provers
still in use, but there are also some new
ones providing high accuracy in national
laboratories.
A similar approach, using a large bag
of known volume, accommodates larger volumes.
Bellinga and Delhez
(1993,
cf. Bellinga et al. 1981) of Nederlandse Gasunie,
Groningen, described the conversion of a portable piston prover for liquids to use
with gases; the prover is capable of flows from 20 to 2000 m
3
/h. The cylinder length
was 12 m with a measuring section of 5.22 m, diameter of 0.584 m, and volume of
1.3988
m
3
. They also described the traceability chain before the prover came into
operation. During the initial calibration of the piston prover, the volume was de-
termined by weighing the quantity of water displaced by the piston when moving
through the measuring section.
A
dynamic calibration was achieved by using a mas-
ter meter. As a check, the volume displaced was obtained from measurement of the
dimensions of the prover. They claimed that these different methods should agree
to within
0.03%.
The pressure difference needed to drive the piston at 150 m
3
/h was
20 mbar, but at lower flow rates the motion became unsteady and was corrected by
reducing the mass of the piston and adding a dynamic damping system. Bellinga
and Delhez also mentioned other small changes to valves, valve operating speed,
and electronics that include pulse interpolation. The aim was for the prover to be
accepted by the Netherlands Measurement Institute as the primary standard for high
pressure gas meter calibration. The meters calibrated from this prover should have
an uncertainty in meter factor of as good as 0.1-0.15%. Reid and Pursley (1986)
considered the use of nitrogen as a pressure-balancing gas to reduce the differential
pressure across the piston and hence to reduce the leakage and to provide stability
of motion at low flow rates.
Reid and Pursley claimed 500:1 operation in air for pressures greater than 30 bar
with agreement to 1% and repeatability of order 0.25% up to 8 bar.
Jongerius et
al.
(1993) described a new low flow test facility consisting of four mer-
cury seal piston provers at the Nederlands Meetinstituut with an operating range of
2 x 10~
5
-3.5 m
3
/h at approximately ambient conditions and operable, in principle,
on any gas. The low flow facility is traceable to the primary length standard, and
uncertainty is about 0.2% for the smallest prover and 0.15% for the others.
4.4.2 MASS MEASUREMENT
Figure 4.14 shows the scheme for a gravimetric calibration facility. The system
shown depends on the use of critical nozzles (which will be explained in Chapter 7)
FLOWMETER
UNDER
TEST
-WATER OR
LIGHT OIL