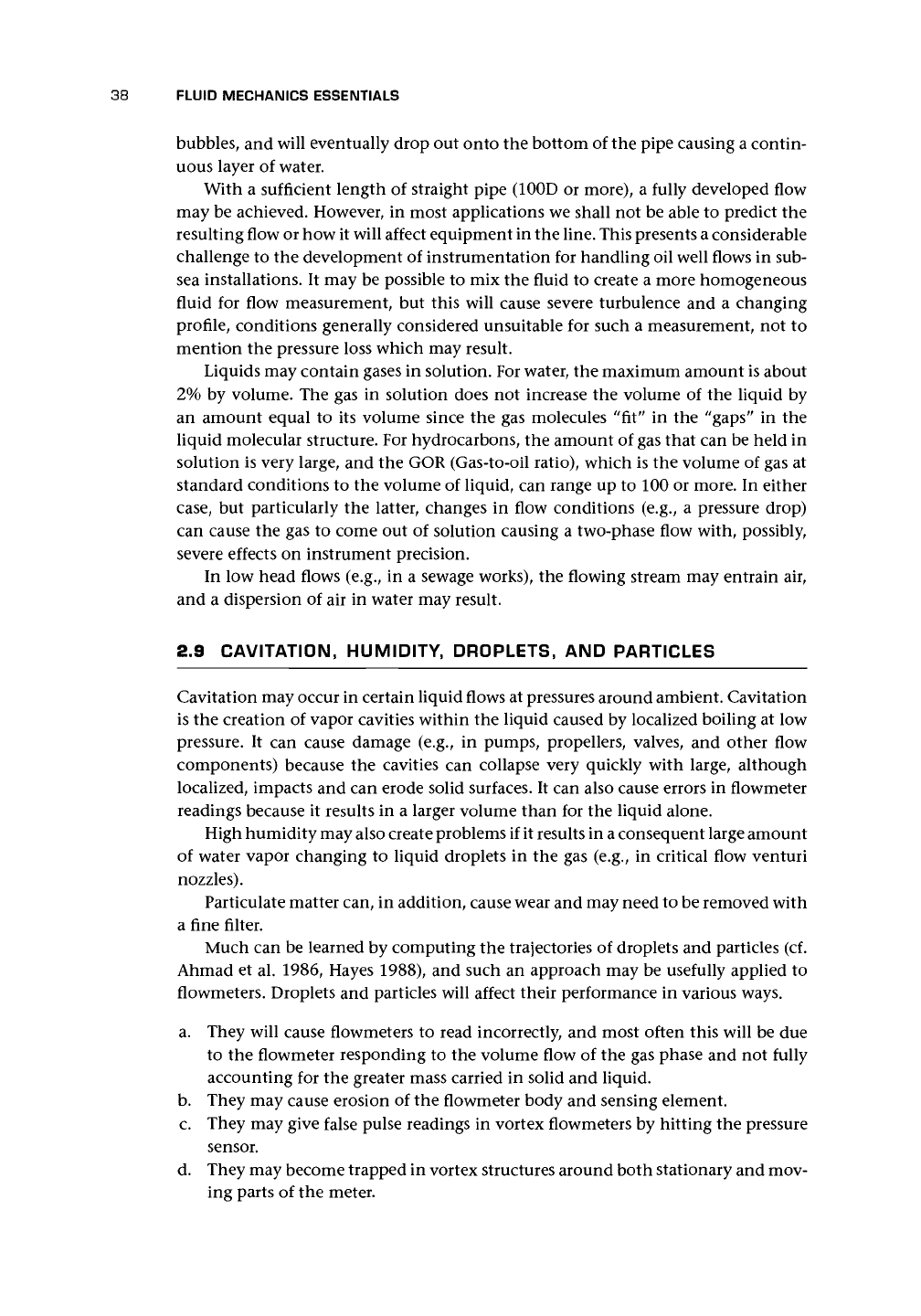
38 FLUID MECHANICS ESSENTIALS
bubbles, and will eventually drop out onto the bottom of the pipe causing a contin-
uous layer of water.
With a sufficient length of straight pipe (100D or more), a fully developed flow
may be achieved. However, in most applications we shall not be able to predict the
resulting flow or how it will affect equipment in the line. This presents a considerable
challenge to the development of instrumentation for handling oil well flows in sub-
sea installations. It may be possible to mix the fluid to create a more homogeneous
fluid for flow measurement, but this will cause severe turbulence and a changing
profile, conditions generally considered unsuitable for such a measurement, not to
mention the pressure loss which may result.
Liquids may contain gases in solution. For water, the maximum amount is about
2%
by volume. The gas in solution does not increase the volume of the liquid by
an amount equal to its volume since the gas molecules "fit'' in the "gaps" in the
liquid molecular structure. For hydrocarbons, the amount of gas that can be held in
solution is very large, and the GOR (Gas-to-oil ratio), which is the volume of gas at
standard conditions to the volume of liquid, can range up to 100 or more. In either
case,
but particularly the latter, changes in flow conditions (e.g., a pressure drop)
can cause the gas to come out of solution causing a two-phase flow with, possibly,
severe effects on instrument precision.
In low head flows (e.g., in a sewage works), the flowing stream may entrain air,
and a dispersion of air in water may result.
2.9 CAVITATION, HUMIDITY, DROPLETS, AND PARTICLES
Cavitation may occur in certain liquid flows at pressures around ambient. Cavitation
is the creation of vapor cavities within the liquid caused by localized boiling at low
pressure. It can cause damage (e.g., in pumps, propellers, valves, and other flow
components) because the cavities can collapse very quickly with large, although
localized, impacts and can erode solid surfaces. It can also cause errors in flowmeter
readings because it results in a larger volume than for the liquid alone.
High humidity may also create problems if it results in a consequent large amount
of water vapor changing to liquid droplets in the gas (e.g., in critical flow venturi
nozzles).
Particulate matter can, in addition, cause wear and may need to be removed with
a fine filter.
Much can be learned by computing the trajectories of droplets and particles (cf.
Ahmad et al. 1986, Hayes 1988), and such an approach may be usefully applied to
flowmeters. Droplets and particles will affect their performance in various ways.
a. They will cause flowmeters to read incorrectly, and most often this will be due
to the flowmeter responding to the volume flow of the gas phase and not fully
accounting for the greater mass carried in solid and liquid.
b.
They may cause erosion of the flowmeter body and sensing element.
c. They may give false pulse readings in vortex flowmeters by hitting the pressure
sensor.
d. They may become trapped in vortex structures around both stationary and mov-
ing parts of the meter.