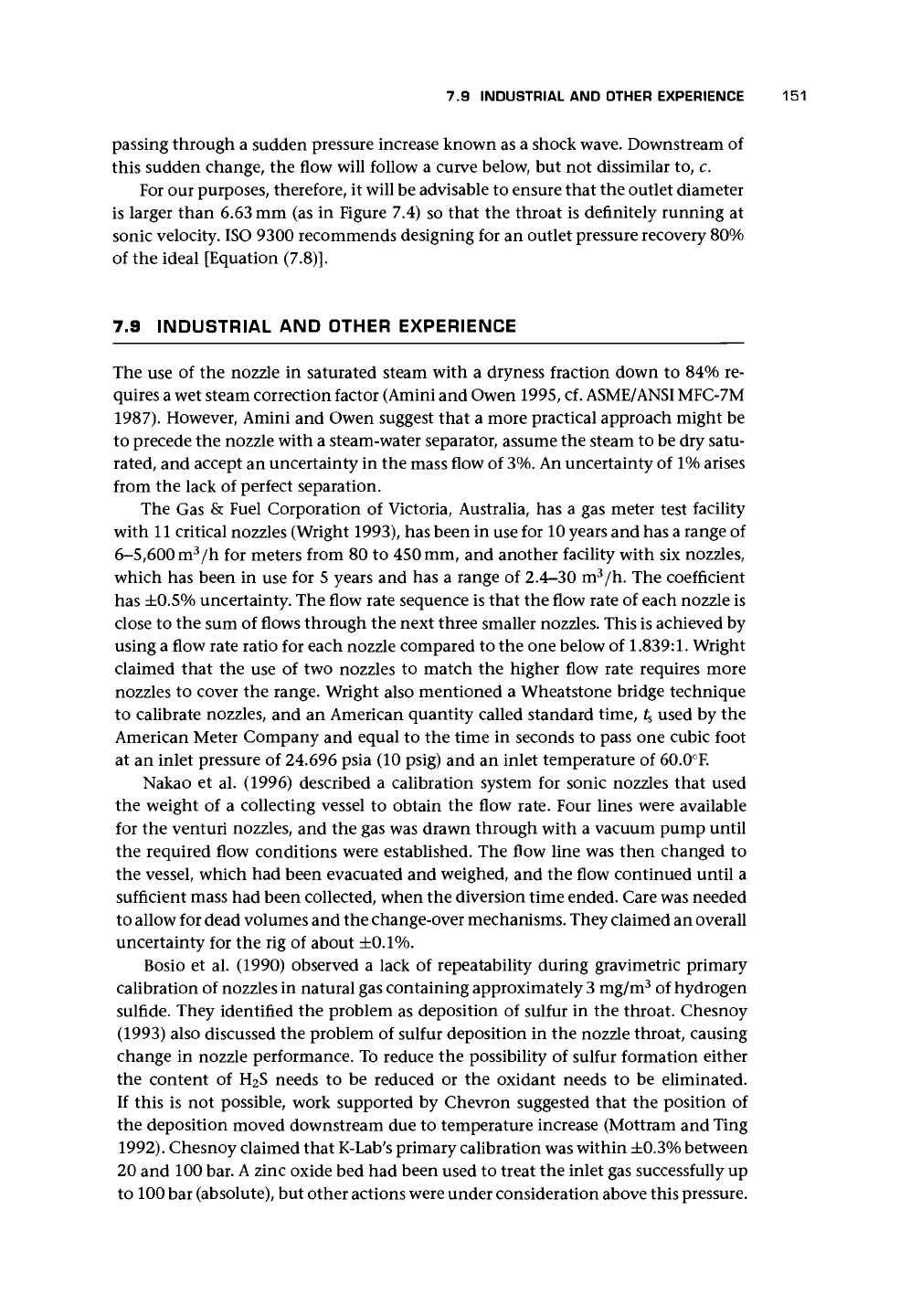
7.9 INDUSTRIAL AND OTHER EXPERIENCE 151
passing through a sudden pressure increase known as a shock
wave.
Downstream of
this sudden change, the flow will follow a curve below, but not dissimilar to, c.
For our purposes, therefore, it will be advisable to ensure that the outlet diameter
is larger than 6.63 mm (as in Figure 7.4) so that the throat is definitely running at
sonic velocity. ISO 9300 recommends designing for an outlet pressure recovery 80%
of the ideal [Equation
(7.8)].
7.9 INDUSTRIAL AND OTHER EXPERIENCE
The use of the nozzle in saturated steam with a dryness fraction down to 84% re-
quires a wet steam correction factor (Amini and Owen 1995, cf. ASME/ANSIMFC-7M
1987).
However, Amini and Owen suggest that a more practical approach might be
to precede the nozzle with a steam-water separator, assume the steam to be dry satu-
rated, and accept an uncertainty in the mass flow of
3%.
An uncertainty of 1% arises
from the lack of perfect separation.
The Gas & Fuel Corporation of Victoria, Australia, has a gas meter test facility
with 11 critical nozzles (Wright 1993), has been in use for 10 years and has a range of
6-5,600 m
3
/h for meters from 80 to 450 mm, and another facility with six nozzles,
which has been in use for 5 years and has a range of 2.4-30 m
3
/h. The coefficient
has ±0.5% uncertainty. The flow rate sequence is that the flow rate of each nozzle is
close to the sum of flows through the next three smaller nozzles. This is achieved by
using a flow rate ratio for each nozzle compared to the one below of 1.839:1. Wright
claimed that the use of two nozzles to match the higher flow rate requires more
nozzles to cover the range. Wright also mentioned a Wheatstone bridge technique
to calibrate nozzles, and an American quantity called standard time, 4 used by the
American Meter Company and equal to the time in seconds to pass one cubic foot
at an inlet pressure of 24.696 psia (10 psig) and an inlet temperature of 60.0°F.
Nakao et al. (1996) described a calibration system for sonic nozzles that used
the weight of a collecting vessel to obtain the flow rate. Four lines were available
for the venturi nozzles, and the gas was drawn through with a vacuum pump until
the required flow conditions were established. The flow line was then changed to
the vessel, which had been evacuated and weighed, and the flow continued until a
sufficient mass had been collected, when the diversion time ended. Care was needed
to allow for dead volumes and the change-over mechanisms. They claimed an overall
uncertainty for the rig of about
±0.1%.
Bosio et al. (1990) observed a lack of repeatability during gravimetric primary
calibration of nozzles in natural gas containing approximately
3
mg/m
3
of hydrogen
sulfide. They identified the problem as deposition of sulfur in the throat. Chesnoy
(1993) also discussed the problem of sulfur deposition in the nozzle throat, causing
change in nozzle performance. To reduce the possibility of sulfur formation either
the content of H
2
S needs to be reduced or the oxidant needs to be eliminated.
If this is not possible, work supported by Chevron suggested that the position of
the deposition moved downstream due to temperature increase (Mottram and Ting
1992).
Chesnoy claimed that K-Lab's primary calibration was within
±0.3%
between
20 and 100 bar.
A
zinc oxide bed had been used to treat the inlet gas successfully up
to 100 bar (absolute), but other actions were under consideration above this pressure.