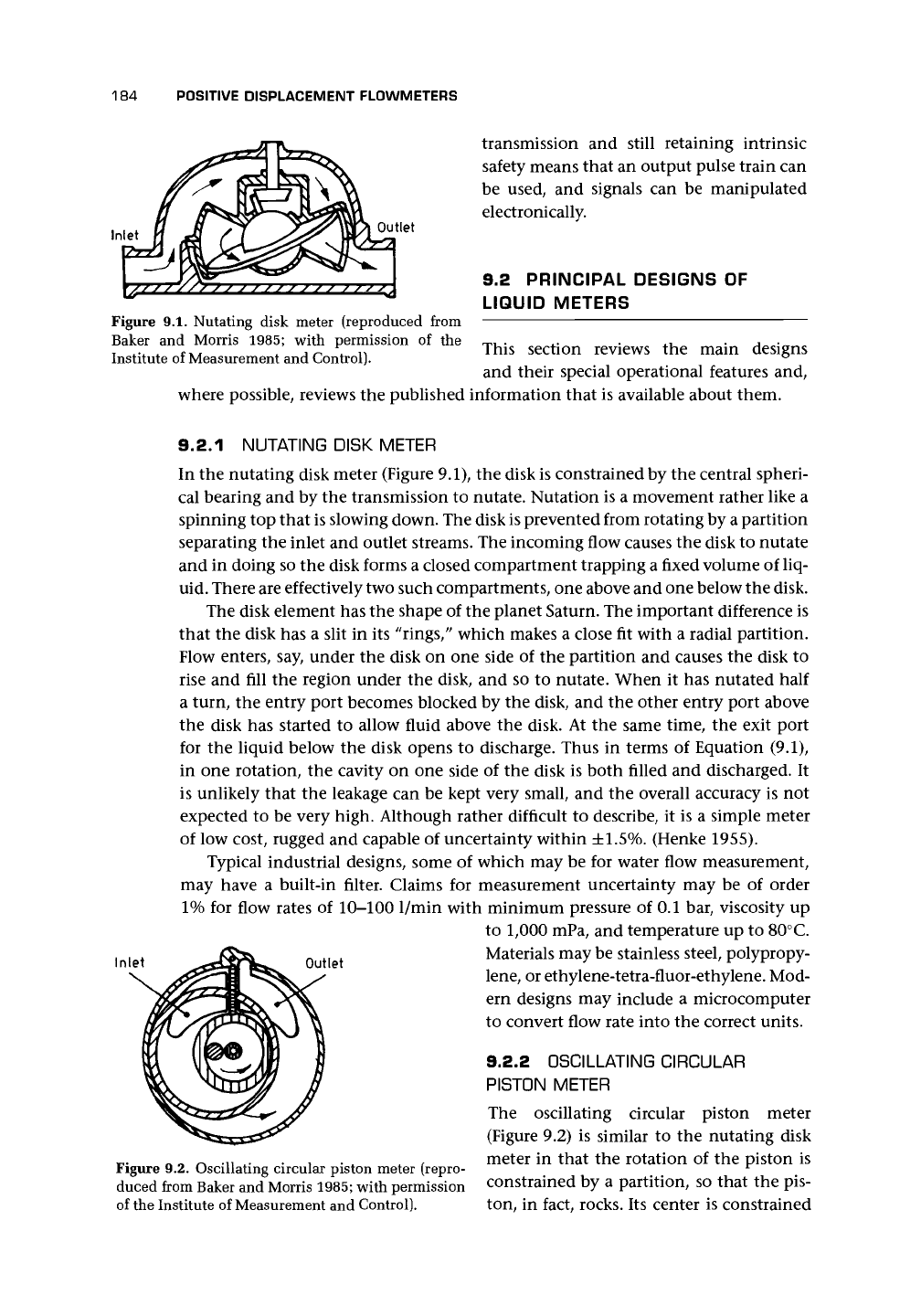
184
POSITIVE DISPLACEMENT FLOWMETERS
Inlet
Outlet
Figure 9.1. Nutating disk meter (reproduced from
Baker and Morris 1985; with permission of the
Institute of Measurement and Control).
transmission and still retaining intrinsic
safety means that an output pulse train can
be used, and signals can be manipulated
electronically.
9.2 PRINCIPAL DESIGNS OF
LIQUID METERS
This section reviews the main designs
and their special operational features and,
where possible, reviews the published information that is available about them.
Inlet
9.2.1 NUTATING DISK METER
In the nutating disk meter (Figure 9.1), the disk is constrained by the central spheri-
cal bearing and by the transmission to nutate. Nutation is a movement rather like a
spinning top that is slowing down. The disk
is
prevented from rotating by a partition
separating the inlet and outlet streams. The incoming flow causes the disk to nutate
and in doing so the disk forms a closed compartment trapping a fixed volume of liq-
uid. There are effectively two such compartments, one above and one below the disk.
The disk element has the shape of the planet Saturn. The important difference is
that the disk has a slit in its "rings/' which makes a close fit with a radial partition.
Flow enters, say, under the disk on one side of the partition and causes the disk to
rise and fill the region under the disk, and so to nutate. When it has nutated half
a turn, the entry port becomes blocked by the disk, and the other entry port above
the disk has started to allow fluid above the disk. At the same time, the exit port
for the liquid below the disk opens to discharge. Thus in terms of Equation (9.1),
in one rotation, the cavity on one side of the disk is both filled and discharged. It
is unlikely that the leakage can be kept very small, and the overall accuracy is not
expected to be very high. Although rather difficult to describe, it is a simple meter
of low cost, rugged and capable of uncertainty within
±1.5%.
(Henke 1955).
Typical industrial designs, some of which may be for water flow measurement,
may have a built-in filter. Claims for measurement uncertainty may be of order
1%
for flow rates of 10-100 1/min with minimum pressure of 0.1 bar, viscosity up
to 1,000 mPa, and temperature up to 80°C.
Materials may be stainless steel, polypropy-
lene,
or ethylene-tetra-fluor-ethylene. Mod-
ern designs may include a microcomputer
to convert flow rate into the correct units.
9.2.2 OSCILLATING CIRCULAR
PISTON METER
The oscillating circular piston meter
(Figure 9.2) is similar to the nutating disk
meter in that the rotation of the piston is
constrained by a partition, so that the pis-
ton, in fact, rocks. Its center is constrained
Outlet
Figure 9.2. Oscillating circular piston meter (repro-
duced from Baker and Morris 1985; with permission
of the Institute of Measurement and Control).