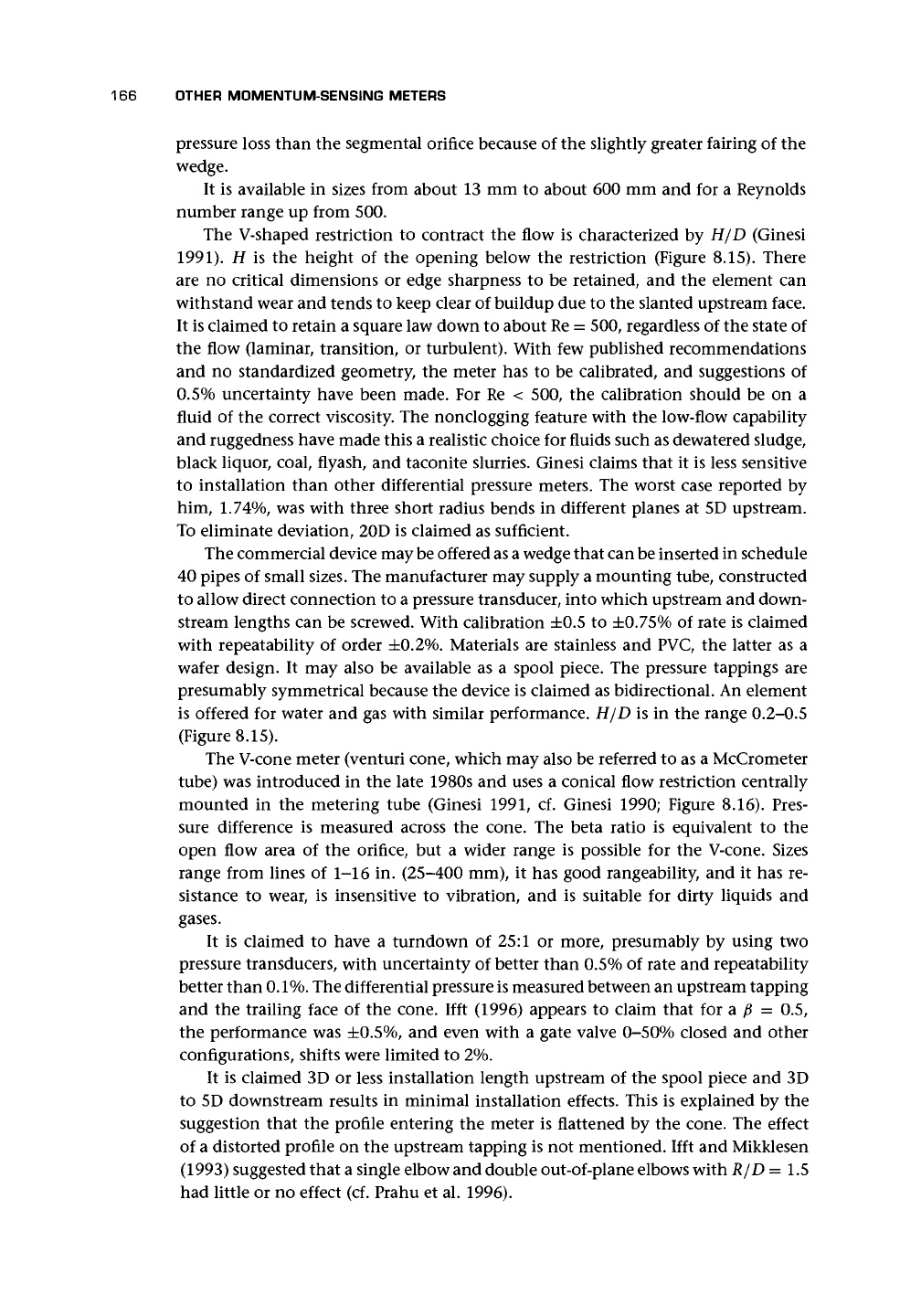
166 OTHER MOMENTUM-SENSING METERS
pressure loss than the segmental orifice because of the slightly greater fairing of the
wedge.
It is available in sizes from about 13 mm to about 600 mm and for a Reynolds
number range up from 500.
The V-shaped restriction to contract the flow is characterized by H/D (Ginesi
1991).
H is the height of the opening below the restriction (Figure 8.15). There
are no critical dimensions or edge sharpness to be retained, and the element can
withstand wear and tends to keep clear of buildup due to the slanted upstream face.
It is claimed to retain a square law down to about Re = 500, regardless of the state of
the flow (laminar, transition, or turbulent). With few published recommendations
and no standardized geometry, the meter has to be calibrated, and suggestions of
0.5%
uncertainty have been made. For Re < 500, the calibration should be on a
fluid of the correct viscosity. The nonclogging feature with the low-flow capability
and ruggedness have made this a realistic choice for fluids such as dewatered sludge,
black liquor, coal, flyash, and taconite slurries. Ginesi claims that it is less sensitive
to installation than other differential pressure meters. The worst case reported by
him,
1.74%,
was with three short radius bends in different planes at 5D upstream.
To eliminate deviation, 20D is claimed as sufficient.
The commercial device may be offered as
a
wedge that can be inserted in schedule
40 pipes of small sizes. The manufacturer may supply a mounting tube, constructed
to allow direct connection to a pressure transducer, into which upstream and down-
stream lengths can be screwed. With calibration ±0.5 to ±0.75% of rate is claimed
with repeatability of order ±0.2%. Materials are stainless and PVC, the latter as a
wafer design. It may also be available as a spool piece. The pressure tappings are
presumably symmetrical because the device is claimed as bidirectional. An element
is offered for water and gas with similar performance. H/D is in the range 0.2-0.5
(Figure 8.15).
The V-cone meter (venturi cone, which may also be referred to as a McCrometer
tube) was introduced in the late 1980s and uses a conical flow restriction centrally
mounted in the metering tube (Ginesi 1991, cf. Ginesi 1990; Figure 8.16). Pres-
sure difference is measured across the cone. The beta ratio is equivalent to the
open flow area of the orifice, but a wider range is possible for the V-cone. Sizes
range from lines of 1-16 in. (25-400 mm), it has good rangeability, and it has re-
sistance to wear, is insensitive to vibration, and is suitable for dirty liquids and
gases.
It is claimed to have a turndown of 25:1 or more, presumably by using two
pressure transducers, with uncertainty of better than 0.5% of rate and repeatability
better than
0.1%.
The differential pressure is measured between an upstream tapping
and the trailing face of the cone. Ifft (1996) appears to claim that for a p = 0.5,
the performance was
±0.5%,
and even with a gate valve 0-50% closed and other
configurations, shifts were limited to 2%.
It is claimed 3D or less installation length upstream of the spool piece and 3D
to 5D downstream results in minimal installation effects. This is explained by the
suggestion that the profile entering the meter is flattened by the cone. The effect
of a distorted profile on the upstream tapping is not mentioned. Ifft and Mikklesen
(1993) suggested that a single elbow and double out-of-plane elbows with R/D =1.5
had little or no effect (cf. Prahu et al. 1996).