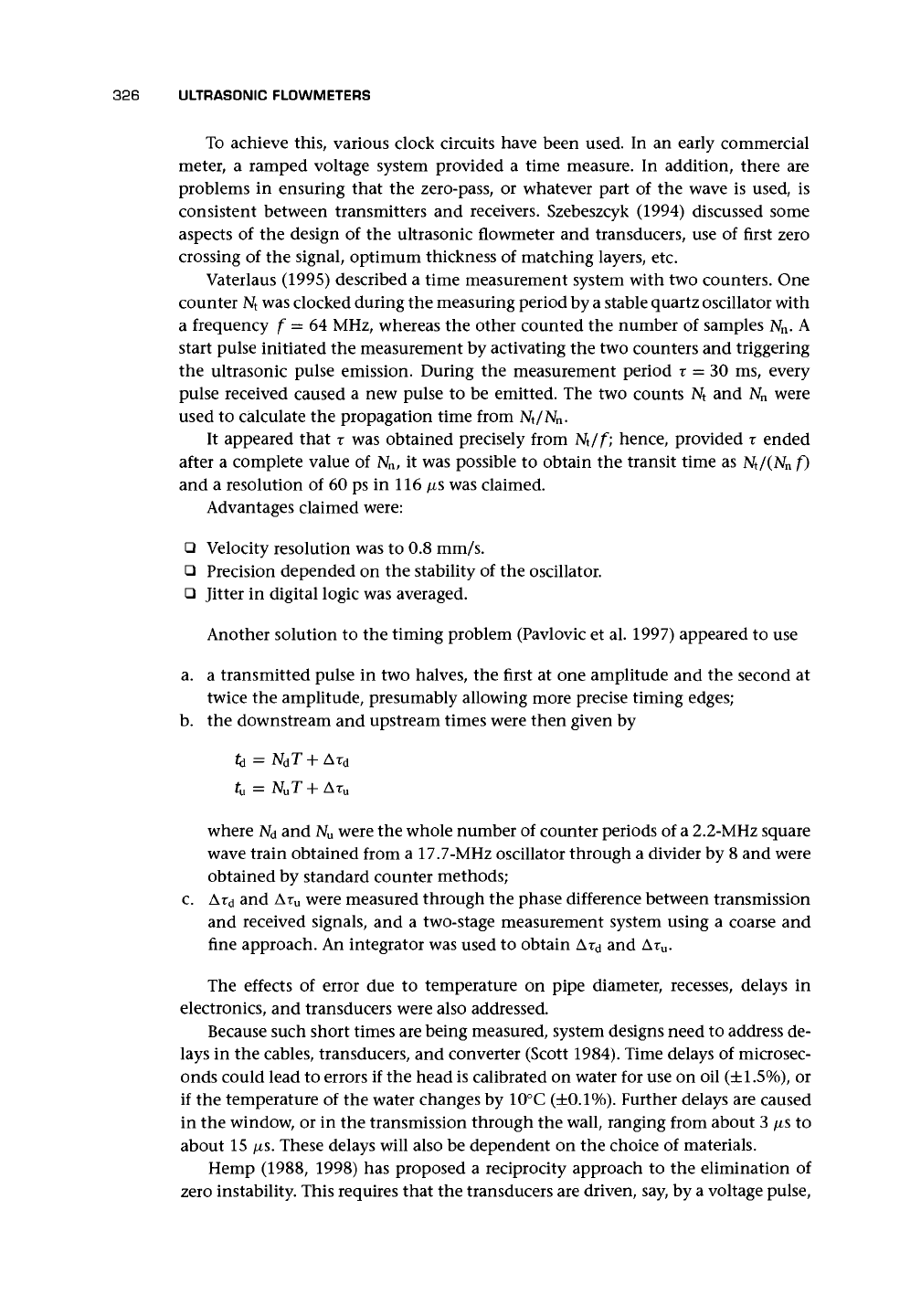
326 ULTRASONIC FLOWMETERS
To achieve this, various clock circuits have been used. In an early commercial
meter, a ramped voltage system provided a time measure. In addition, there are
problems in ensuring that the zero-pass, or whatever part of the wave is used, is
consistent between transmitters and receivers. Szebeszcyk (1994) discussed some
aspects of the design of the ultrasonic flowmeter and transducers, use of first zero
crossing of the signal, optimum thickness of matching layers, etc.
Vaterlaus (1995) described a time measurement system with two counters. One
counter N
t
was clocked during the measuring period by a stable quartz oscillator with
a frequency f
—
64 MHz, whereas the other counted the number of samples N
n
. A
start pulse initiated the measurement by activating the two counters and triggering
the ultrasonic pulse emission. During the measurement period r = 30 ms, every
pulse received caused a new pulse to be emitted. The two counts N
t
and N
n
were
used to calculate the propagation time from
N
t
/N
n
.
It appeared that x was obtained precisely from N
t
/f; hence, provided x ended
after a complete value of N
n
, it was possible to obtain the transit time as
N
t
/(N
n
f)
and a resolution of 60 ps in 116 /xs was claimed.
Advantages claimed were:
• Velocity resolution was to 0.8 mm/s.
• Precision depended on the stability of the oscillator.
• Jitter in digital logic was averaged.
Another solution to the timing problem (Pavlovic et al. 1997) appeared to use
a. a transmitted pulse in two halves, the first at one amplitude and the second at
twice the amplitude, presumably allowing more precise timing edges;
b.
the downstream and upstream times were then given by
t&
= N
d
T+ Ar
d
ta = N
U
T + Ar
u
where N
d
and N
u
were the whole number of counter periods of a 2.2-MHz square
wave train obtained from a 17.7-MHz oscillator through a divider by 8 and were
obtained by standard counter methods;
c. Ard and Ar
u
were measured through the phase difference between transmission
and received signals, and a two-stage measurement system using a coarse and
fine approach. An integrator was used to obtain Aid and Ar
u
.
The effects of error due to temperature on pipe diameter, recesses, delays in
electronics, and transducers were also addressed.
Because such short times are being measured, system designs need to address de-
lays in the cables, transducers, and converter (Scott 1984). Time delays of microsec-
onds could lead to errors if the head is calibrated on water for use on oil (±1.5%), or
if the temperature of the water changes by 10°C (±0.1%). Further delays are caused
in the window, or in the transmission through the wall, ranging from about 3 /is to
about 15 /xs. These delays will also be dependent on the choice of materials.
Hemp (1988, 1998) has proposed a reciprocity approach to the elimination of
zero instability. This requires that the transducers are driven, say, by a voltage pulse,