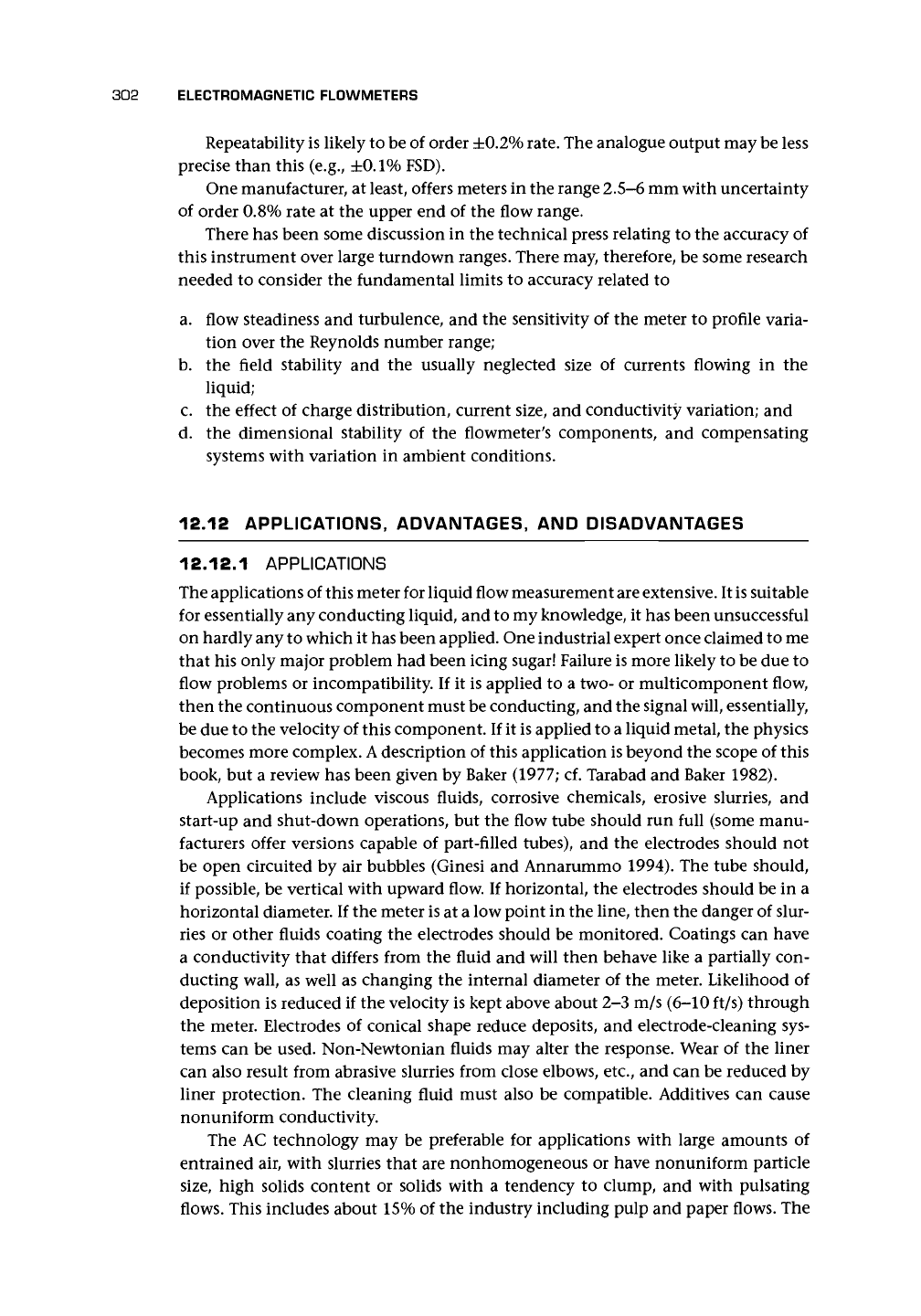
302 ELECTROMAGNETIC FLOWMETERS
Repeatability is likely to be of order ±0.2% rate. The analogue output may be less
precise than this (e.g., ±0.1% FSD).
One manufacturer, at least, offers meters in the range 2.5-6 mm with uncertainty
of order 0.8% rate at the upper end of the flow range.
There has been some discussion in the technical press relating to the accuracy of
this instrument over large turndown ranges. There may, therefore, be some research
needed to consider the fundamental limits to accuracy related to
a. flow steadiness and turbulence, and the sensitivity of the meter to profile varia-
tion over the Reynolds number range;
b.
the field stability and the usually neglected size of currents flowing in the
liquid;
c. the effect of charge distribution, current size, and conductivity variation; and
d. the dimensional stability of the flowmeter
;
s components, and compensating
systems with variation in ambient conditions.
12.12 APPLICATIONS, ADVANTAGES, AND DISADVANTAGES
12.12.1 APPLICATIONS
The applications of this meter for liquid flow measurement are extensive. It
is
suitable
for essentially any conducting liquid, and to my knowledge, it has been unsuccessful
on hardly any to which it has been applied. One industrial expert once claimed to me
that his only major problem had been icing sugar! Failure is more likely to be due to
flow problems or incompatibility. If it is applied to a two- or multicomponent flow,
then the continuous component must be conducting, and the signal
will,
essentially,
be due to the velocity of this component. If it is applied to a liquid metal, the physics
becomes more complex.
A
description of this application is beyond the scope of this
book, but a review has been given by Baker (1977; cf. Tarabad and Baker 1982).
Applications include viscous fluids, corrosive chemicals, erosive slurries, and
start-up and shut-down operations, but the flow tube should run full (some manu-
facturers offer versions capable of part-filled tubes), and the electrodes should not
be open circuited by air bubbles (Ginesi and Annarummo 1994). The tube should,
if possible, be vertical with upward flow. If horizontal, the electrodes should be in a
horizontal diameter. If the meter is at a low point in the line, then the danger of slur-
ries or other fluids coating the electrodes should be monitored. Coatings can have
a conductivity that differs from the fluid and will then behave like a partially con-
ducting wall, as well as changing the internal diameter of the meter. Likelihood of
deposition is reduced if the velocity is kept above about 2-3 m/s (6-10 ft/s) through
the meter. Electrodes of conical shape reduce deposits, and electrode-cleaning sys-
tems can be used. Non-Newtonian fluids may alter the response. Wear of the liner
can also result from abrasive slurries from close elbows, etc., and can be reduced by
liner protection. The cleaning fluid must also be compatible. Additives can cause
nonuniform conductivity.
The AC technology may be preferable for applications with large amounts of
entrained air, with slurries that are nonhomogeneous or have nonuniform particle
size,
high solids content or solids with a tendency to clump, and with pulsating
flows. This includes about 15% of the industry including pulp and paper flows. The