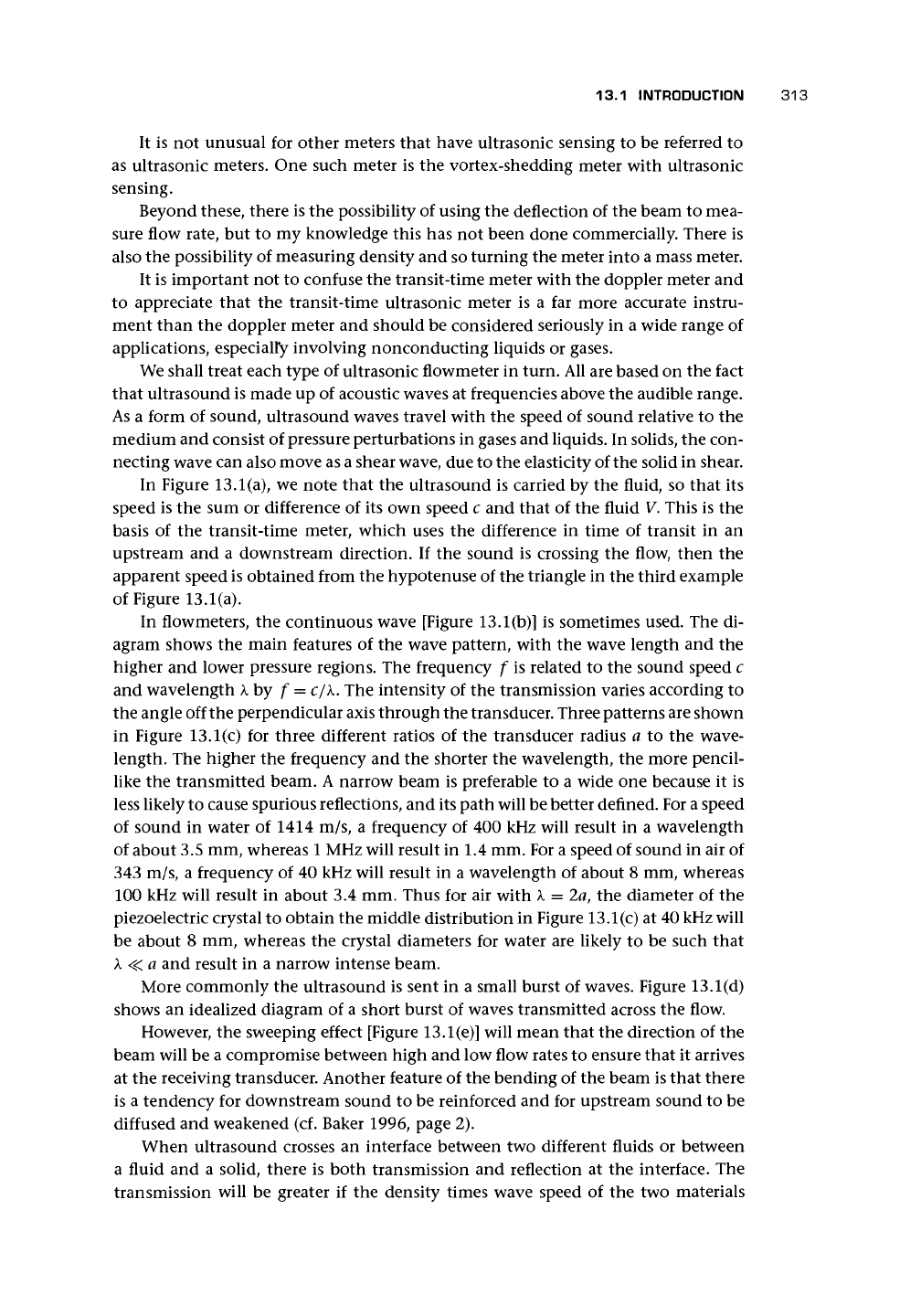
13.1 INTRODUCTION 313
It is not unusual for other meters that have ultrasonic sensing to be referred to
as ultrasonic meters. One such meter is the vortex-shedding meter with ultrasonic
sensing.
Beyond these, there is the possibility of using the deflection of the beam to mea-
sure flow rate, but to my knowledge this has not been done commercially. There is
also the possibility of measuring density and so turning the meter into a mass meter.
It is important not to confuse the transit-time meter with the doppler meter and
to appreciate that the transit-time ultrasonic meter is a far more accurate instru-
ment than the doppler meter and should be considered seriously in a wide range of
applications, especially involving nonconducting liquids or gases.
We shall treat each type of ultrasonic flowmeter in turn. All are based on the fact
that ultrasound is made up of acoustic waves at frequencies above the audible range.
As a form of sound, ultrasound waves travel with the speed of sound relative to the
medium and consist of pressure perturbations in gases and liquids. In solids, the con-
necting wave can also move as a shear
wave,
due to the elasticity of the solid in shear.
In Figure 13.1
(a),
we note that the ultrasound is carried by the fluid, so that its
speed is the sum or difference of its own speed c and that of the fluid V. This is the
basis of the transit-time meter, which uses the difference in time of transit in an
upstream and a downstream direction. If the sound is crossing the flow, then the
apparent speed is obtained from the hypotenuse of the triangle in the third example
of Figure 13.1
(a).
In flowmeters, the continuous wave [Figure 13.1(b)] is sometimes used. The di-
agram shows the main features of the wave pattern, with the wave length and the
higher and lower pressure regions. The frequency f is related to the sound speed c
and wavelength k by f = c/k. The intensity of the transmission varies according to
the angle off the perpendicular axis through the transducer. Three patterns are shown
in Figure 13.1(c) for three different ratios of the transducer radius a to the wave-
length. The higher the frequency and the shorter the wavelength, the more pencil-
like the transmitted beam. A narrow beam is preferable to a wide one because it is
less likely to cause spurious reflections, and its path will be better defined. For a speed
of sound in water of 1414 m/s, a frequency of 400 kHz will result in a wavelength
of about 3.5 mm, whereas
1
MHz will result in 1.4 mm. For a speed of sound in air of
343 m/s, a frequency of 40 kHz will result in a wavelength of about 8 mm, whereas
100 kHz will result in about 3.4 mm. Thus for air with k = 2a, the diameter of the
piezoelectric crystal to obtain the middle distribution in Figure 13.1(c) at 40 kHz will
be about 8 mm, whereas the crystal diameters for water are likely to be such that
k < a and result in a narrow intense beam.
More commonly the ultrasound is sent in a small burst of waves. Figure 13.1(d)
shows an idealized diagram of a short burst of waves transmitted across the flow.
However, the sweeping effect [Figure 13.1(e)] will mean that the direction of the
beam will be a compromise between high and low flow rates to ensure that it arrives
at the receiving transducer. Another feature of the bending of the beam is that there
is a tendency for downstream sound to be reinforced and for upstream sound to be
diffused and weakened (cf. Baker 1996, page 2).
When ultrasound crosses an interface between two different fluids or between
a fluid and a solid, there is both transmission and reflection at the interface. The
transmission will be greater if the density times wave speed of the two materials