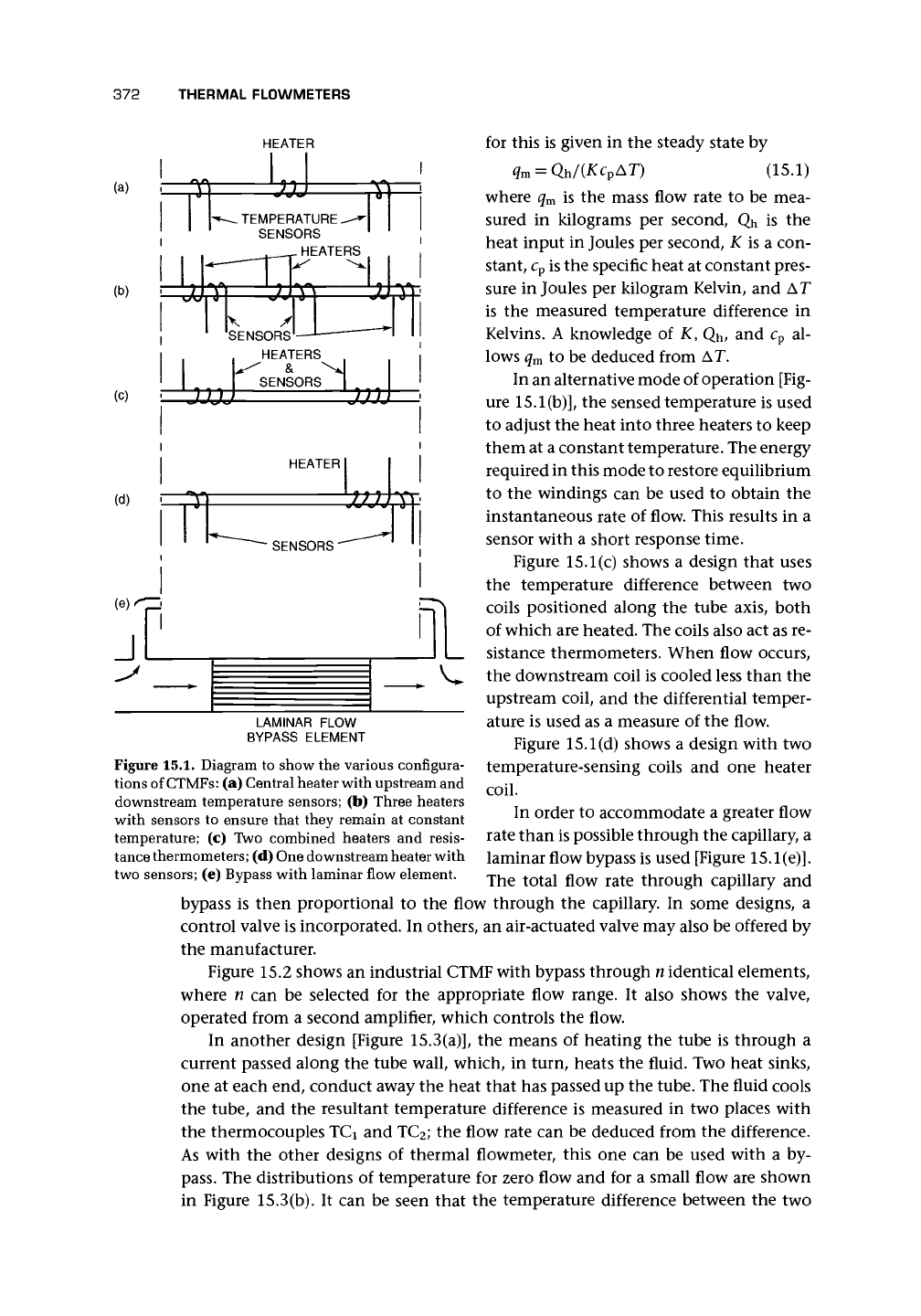
372
THERMAL FLOWMETERS
HEATER
(a)
(b)
TEMPERATURE^-
SENSORS
HEATERS
(c)
(d)
LAMINAR FLOW
BYPASS ELEMENT
Figure 15.1. Diagram to show the various configura-
tions of CTMFs: (a) Central heater with upstream and
downstream temperature sensors; (b) Three heaters
with sensors to ensure that they remain at constant
temperature; (c) Two combined heaters and resis-
tance thermometers; (d) One downstream heater with
two sensors; (e) Bypass with laminar flow element.
for this is given in the steady state by
q
m
= Qh/(Kc
v
AT) (15.1)
where q
m
is the mass flow rate to be mea-
sured in kilograms per second, Qh is the
heat input in Joules per second, K is a con-
stant, c
p
is the specific heat at constant pres-
sure in Joules per kilogram Kelvin, and AT
is the measured temperature difference in
Kelvins. A knowledge of K, Qh, and c
p
al-
lows q
m
to be deduced from AT.
In an alternative mode of operation [Fig-
ure 15.1(b)], the sensed temperature is used
to adjust the heat into three heaters to keep
them at a constant temperature. The energy
required in this mode to restore equilibrium
to the windings can be used to obtain the
instantaneous rate of flow. This results in a
sensor with a short response time.
Figure 15.1(c) shows a design that uses
the temperature difference between two
coils positioned along the tube axis, both
of which are heated. The coils also act as re-
sistance thermometers. When flow occurs,
the downstream coil is cooled less than the
upstream coil, and the differential temper-
ature is used as a measure of the flow.
Figure 15.1(d) shows a design with two
temperature-sensing coils and one heater
coil.
In order to accommodate a greater flow
rate than is possible through the capillary, a
laminar flow bypass is used [Figure 15.1(e)].
The total flow rate through capillary and
bypass is then proportional to the flow through the capillary. In some designs, a
control valve is incorporated. In others, an air-actuated valve may also be offered by
the manufacturer.
Figure 15.2 shows an industrial CTMF with bypass through n identical elements,
where n can be selected for the appropriate flow range. It also shows the valve,
operated from a second amplifier, which controls the flow.
In another design [Figure 15.3(a)], the means of heating the tube is through a
current passed along the tube wall, which, in turn, heats the fluid. Two heat sinks,
one at each end, conduct away the heat that has passed up the tube. The fluid cools
the tube, and the resultant temperature difference is measured in two places with
the thermocouples TCi and TC
2
; the flow rate can be deduced from the difference.
As with the other designs of thermal flowmeter, this one can be used with a by-
pass.
The distributions of temperature for zero flow and for a small flow are shown
in Figure 15.3(b). It can be seen that the temperature difference between the two