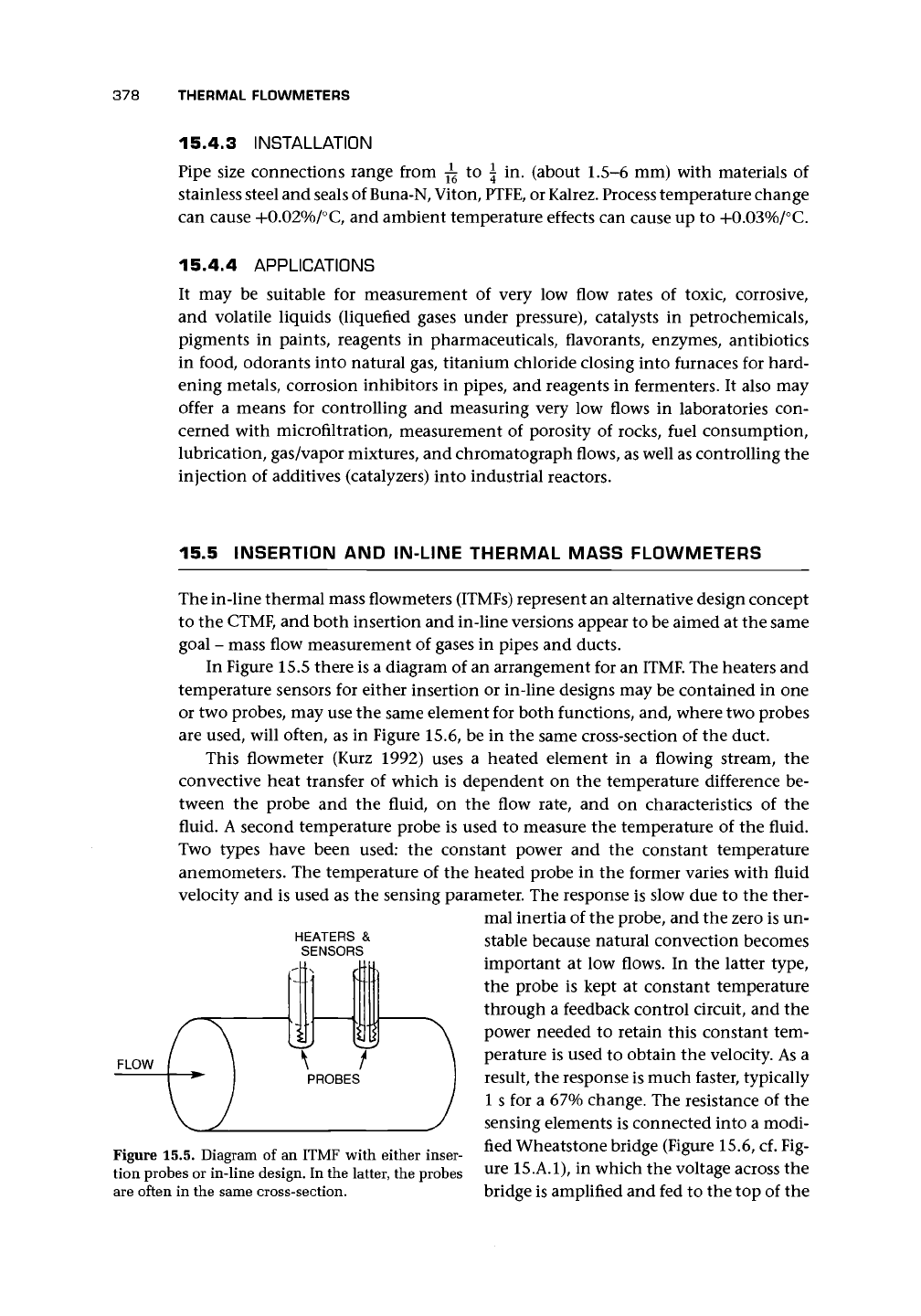
378 THERMAL FLOWMETERS
15.4.3
INSTALLATION
Pipe size connections range from
^ to \
in. (about 1.5-6 mm) with materials of
stainless steel and seals of
Buna-N,
Viton,
PTFE,
or
Kalrez.
Process temperature change
can cause +0.02%/°C, and ambient temperature effects can cause up to +0.03%/°C.
15.4.4
APPLICATIONS
It may
be
suitable
for
measurement
of
very low flow rates
of
toxic, corrosive,
and volatile liquids (liquefied gases under pressure), catalysts
in
petrochemicals,
pigments
in
paints, reagents
in
pharmaceuticals, flavorants, enzymes, antibiotics
in food, odorants into natural gas, titanium chloride closing into furnaces for hard-
ening metals, corrosion inhibitors in pipes, and reagents in fermenters. It also may
offer
a
means
for
controlling and measuring very low flows
in
laboratories con-
cerned with microfiltration, measurement of porosity of rocks, fuel consumption,
lubrication, gas/vapor mixtures, and chromatograph flows, as well as controlling the
injection of additives (catalyzers) into industrial reactors.
15.5 INSERTION AND IN-LINE THERMAL MASS FLOWMETERS
The in-line thermal mass flowmeters (ITMFs) represent an alternative design concept
to the CTMF, and both insertion and in-line versions appear to be aimed at the same
goal
-
mass flow measurement of gases in pipes and ducts.
In Figure 15.5 there is a diagram of an arrangement for an
ITMF.
The heaters and
temperature sensors for either insertion or in-line designs may be contained in one
or two probes, may use the same element for both functions, and, where two probes
are used, will often, as in Figure 15.6, be in the same cross-section of the duct.
This flowmeter (Kurz 1992) uses
a
heated element
in a
flowing stream,
the
convective heat transfer of which is dependent on the temperature difference be-
tween the probe and
the
fluid,
on the
flow rate, and
on
characteristics
of
the
fluid. A second temperature probe is used to measure the temperature of the fluid.
Two types have been used:
the
constant power and
the
constant temperature
anemometers. The temperature of the heated probe in the former varies with fluid
velocity and is used as the sensing parameter. The response is slow due to the ther-
mal inertia of the probe, and the zero is un-
stable because natural convection becomes
important
at
low flows.
In
the latter type,
the probe
is
kept
at
constant temperature
through a feedback control circuit, and the
power needed to retain this constant tem-
perature is used to obtain the velocity. As a
result, the response is much faster, typically
1 s for a 67% change. The resistance of the
sensing elements is connected into a modi-
fied Wheatstone bridge (Figure 15.6, cf. Fig-
ure 15.A.I), in which the voltage across the
bridge is amplified and fed to the top of the
HEATERS
&
SENSORS
Figure 15.5. Diagram of an ITMF with either inser-
tion probes or in-line design. In the latter, the probes
are often in the same cross-section.