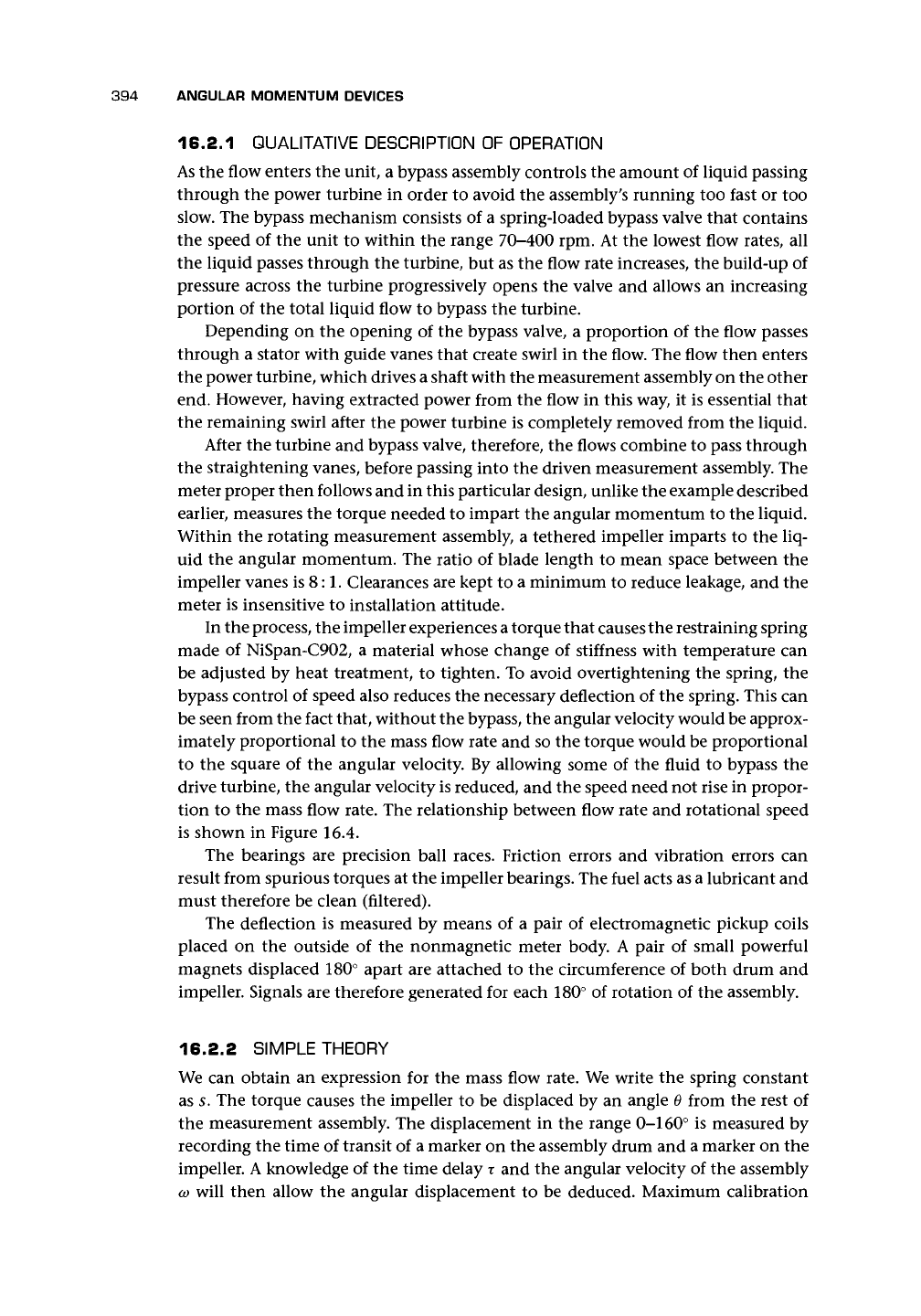
394 ANGULAR MOMENTUM DEVICES
16.2.1 QUALITATIVE DESCRIPTION
OF
OPERATION
As the flow enters the unit, a bypass assembly controls the amount of liquid passing
through the power turbine in order to avoid the assembly's running too fast or too
slow. The bypass mechanism consists of a spring-loaded bypass valve that contains
the speed of the unit to within the range 70-400 rpm. At the lowest flow rates, all
the liquid passes through the turbine, but as the flow rate increases, the build-up of
pressure across the turbine progressively opens the valve and allows an increasing
portion of the total liquid flow to bypass the turbine.
Depending on the opening of the bypass valve, a proportion of the flow passes
through a stator with guide vanes that create swirl in the flow. The flow then enters
the power turbine, which drives a shaft with the measurement assembly on the other
end. However, having extracted power from the flow in this way, it is essential that
the remaining swirl after the power turbine is completely removed from the liquid.
After the turbine and bypass valve, therefore, the flows combine to pass through
the straightening vanes, before passing into the driven measurement assembly. The
meter proper then follows and in this particular design, unlike the example described
earlier, measures the torque needed to impart the angular momentum to the liquid.
Within the rotating measurement assembly, a tethered impeller imparts to the liq-
uid the angular momentum. The ratio of blade length to mean space between the
impeller vanes is 8:1. Clearances are kept to a minimum to reduce leakage, and the
meter is insensitive to installation attitude.
In the process, the impeller experiences a torque that causes the restraining spring
made of NiSpan-C902, a material whose change of stiffness with temperature can
be adjusted by heat treatment, to tighten. To avoid overtightening the spring, the
bypass control of speed also reduces the necessary deflection of the spring. This can
be seen from the fact that, without the bypass, the angular velocity would be approx-
imately proportional to the mass flow rate and so the torque would be proportional
to the square of the angular velocity. By allowing some of the fluid to bypass the
drive turbine, the angular velocity is reduced, and the speed need not rise in propor-
tion to the mass flow rate. The relationship between flow rate and rotational speed
is shown in Figure 16.4.
The bearings are precision ball races. Friction errors and vibration errors can
result from spurious torques at the impeller bearings. The fuel acts as a lubricant and
must therefore be clean (filtered).
The deflection is measured by means of a pair of electromagnetic pickup coils
placed on the outside of the nonmagnetic meter body. A pair of small powerful
magnets displaced 180° apart are attached to the circumference of both drum and
impeller. Signals are therefore generated for each 180° of rotation of the assembly.
16.2.2 SIMPLE THEORY
We can obtain an expression for the mass flow rate. We write the spring constant
as s. The torque causes the impeller to be displaced by an angle 0 from the rest of
the measurement assembly. The displacement in the range 0-160° is measured by
recording the time of transit of a marker on the assembly drum and a marker on the
impeller. A knowledge of the time delay r and the angular velocity of the assembly
co
will then allow the angular displacement to be deduced. Maximum calibration