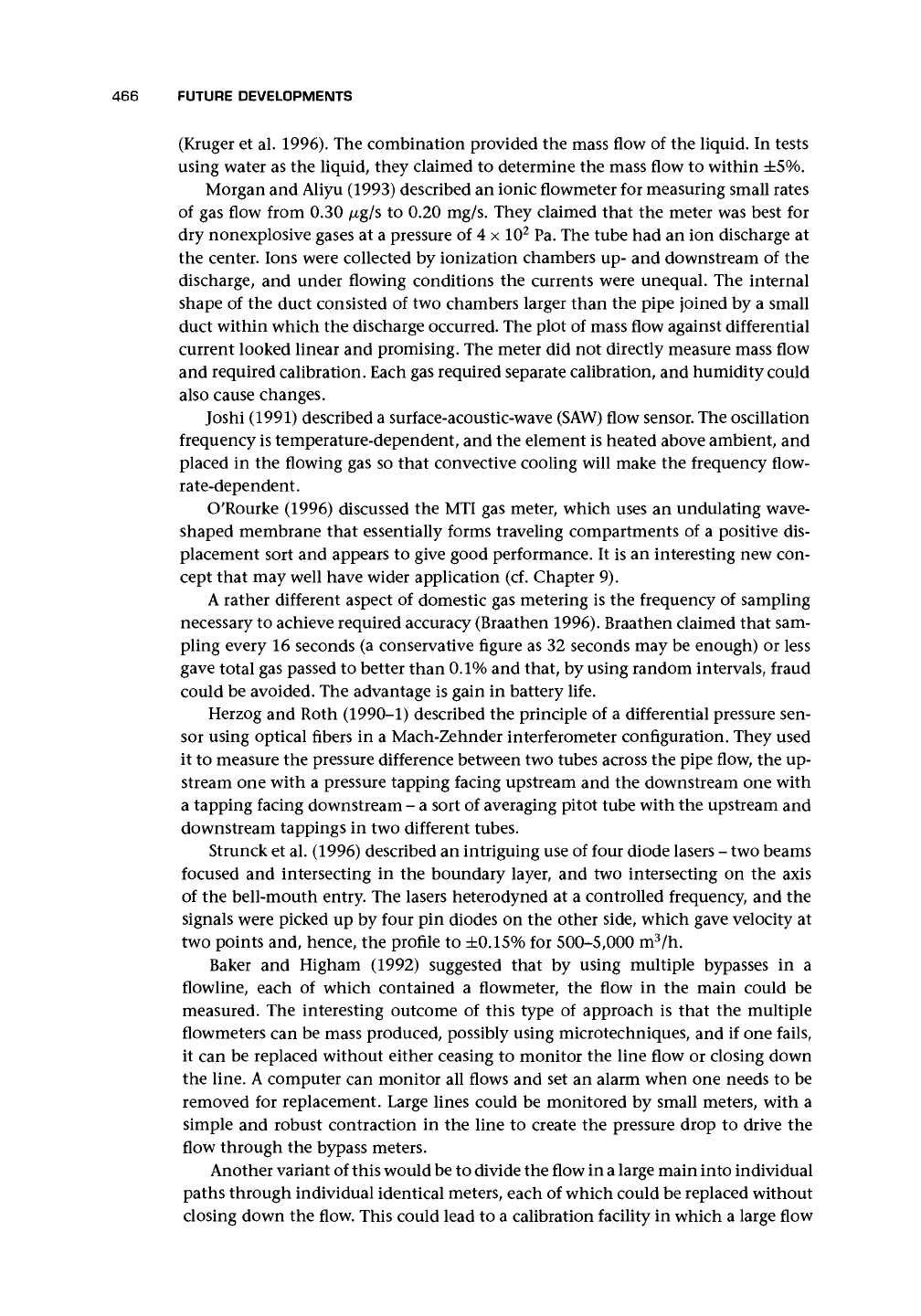
466 FUTURE DEVELOPMENTS
(Kruger et al. 1996). The combination provided the mass flow of the liquid. In tests
using water as the liquid, they claimed to determine the mass flow to within ±5%.
Morgan and Aliyu (1993) described an ionic flowmeter for measuring small rates
of gas flow from 0.30 /ig/s to 0.20 mg/s. They claimed that the meter was best for
dry nonexplosive gases at a pressure of 4 x 10
2
Pa. The tube had an ion discharge at
the center. Ions were collected by ionization chambers up- and downstream of the
discharge, and under flowing conditions the currents were unequal. The internal
shape of the duct consisted of two chambers larger than the pipe joined by a small
duct within which the discharge occurred. The plot of mass flow against differential
current looked linear and promising. The meter did not directly measure mass flow
and required calibration. Each gas required separate calibration, and humidity could
also cause changes.
Joshi (1991) described a surface-acoustic-wave (SAW) flow sensor. The oscillation
frequency is temperature-dependent, and the element is heated above ambient, and
placed in the flowing gas so that convective cooling will make the frequency flow-
rate-dependent.
O'Rourke (1996) discussed the MTI gas meter, which uses an undulating wave-
shaped membrane that essentially forms traveling compartments of a positive dis-
placement sort and appears to give good performance. It is an interesting new con-
cept that may well have wider application (cf. Chapter 9).
A rather different aspect of domestic gas metering is the frequency of sampling
necessary to achieve required accuracy (Braathen 1996). Braathen claimed that sam-
pling every 16 seconds (a conservative figure as 32 seconds may be enough) or less
gave total gas passed to better than
0.1%
and that, by using random intervals, fraud
could be avoided. The advantage is gain in battery life.
Herzog and Roth (1990-1) described the principle of a differential pressure sen-
sor using optical fibers in a Mach-Zehnder interferometer configuration. They used
it to measure the pressure difference between two tubes across the pipe flow, the up-
stream one with a pressure tapping facing upstream and the downstream one with
a tapping facing downstream - a sort of averaging pitot tube with the upstream and
downstream tappings in two different tubes.
Strunck et al. (1996) described an intriguing use of four diode lasers - two beams
focused and intersecting in the boundary layer, and two intersecting on the axis
of the bell-mouth entry. The lasers heterodyned at a controlled frequency, and the
signals were picked up by four pin diodes on the other side, which gave velocity at
two points and, hence, the profile to ±0.15% for 500-5,000 m
3
/h.
Baker and Higham (1992) suggested that by using multiple bypasses in a
flowline, each of which contained a flowmeter, the flow in the main could be
measured. The interesting outcome of this type of approach is that the multiple
flowmeters can be mass produced, possibly using microtechniques, and if one fails,
it can be replaced without either ceasing to monitor the line flow or closing down
the line. A computer can monitor all flows and set an alarm when one needs to be
removed for replacement. Large lines could be monitored by small meters, with a
simple and robust contraction in the line to create the pressure drop to drive the
flow through the bypass meters.
Another variant of this would be to divide the flow in a large main into individual
paths through individual identical meters, each of which could be replaced without
closing down the flow. This could lead to a calibration facility in which a large flow