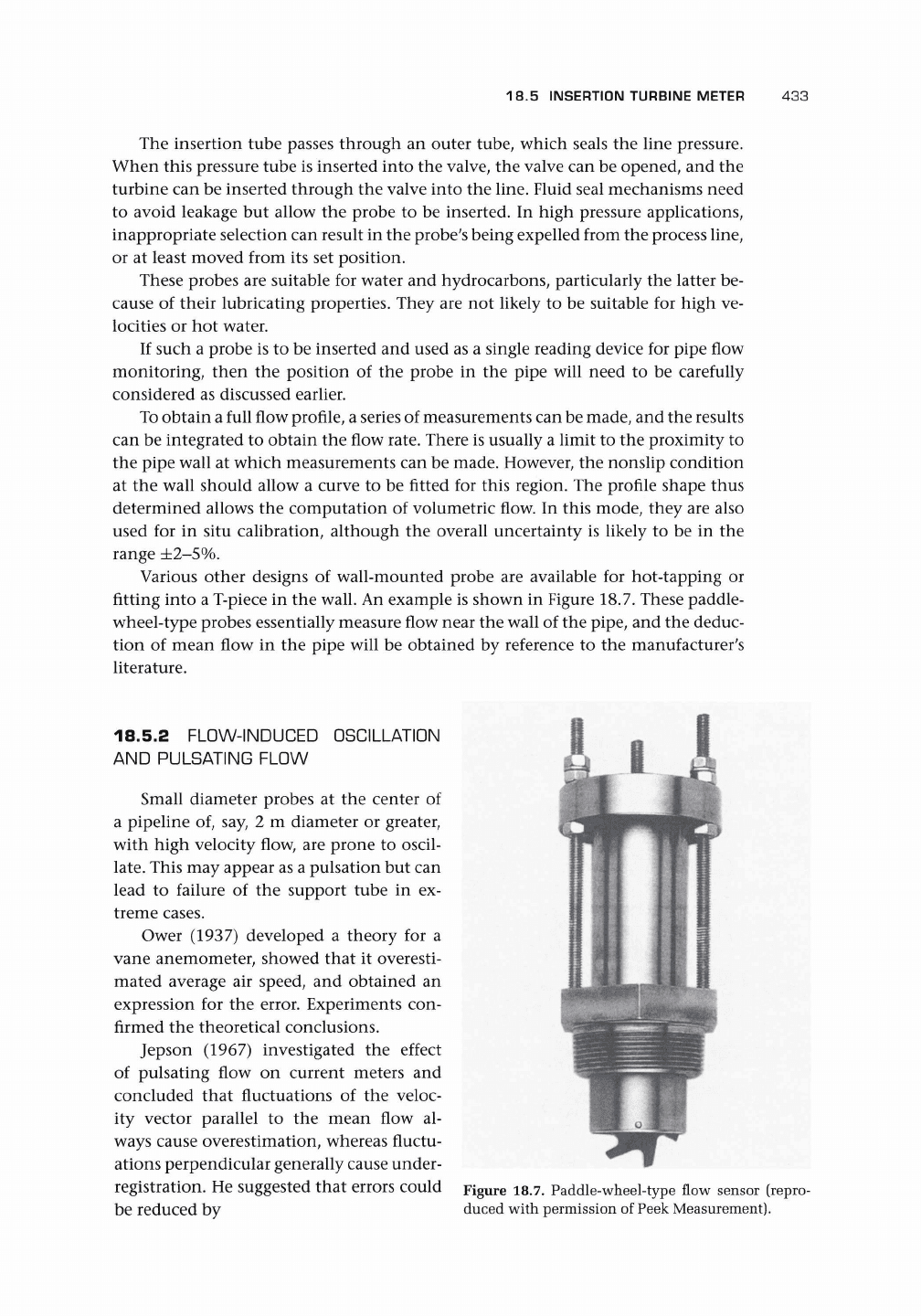
18.5 INSERTION TURBINE METER
433
The insertion tube passes through an outer tube, which seals the line pressure.
When this pressure tube is inserted into the valve, the valve can be opened, and the
turbine can be inserted through the valve into the line. Fluid seal mechanisms need
to avoid leakage but allow the probe to be inserted. In high pressure applications,
inappropriate selection can result in the probe's being expelled from the process line,
or at least moved from its set position.
These probes are suitable for water and hydrocarbons, particularly the latter be-
cause of their lubricating properties. They are not likely to be suitable for high ve-
locities or hot water.
If such a probe is to be inserted and used as a single reading device for pipe flow
monitoring, then the position of the probe in the pipe will need to be carefully
considered as discussed earlier.
To obtain a full flow profile, a series of measurements can be made, and the results
can be integrated to obtain the flow rate. There is usually a limit to the proximity to
the pipe wall at which measurements can be made. However, the nonslip condition
at the wall should allow a curve to be fitted for this region. The profile shape thus
determined allows the computation of volumetric flow. In this mode, they are also
used for in situ calibration, although the overall uncertainty is likely to be in the
range
±2-5%.
Various other designs of wall-mounted probe are available for hot-tapping or
fitting into a T-piece in the wall. An example is shown in Figure 18.7. These paddle-
wheel-type probes essentially measure flow near the wall of the pipe, and the deduc-
tion of mean flow in the pipe will be obtained by reference to the manufacturer's
literature.
18.5.2 FLOW-INDUCED OSCILLATION
AND PULSATING FLOW
Small diameter probes at the center of
a pipeline of, say, 2 m diameter or greater,
with high velocity flow, are prone to oscil-
late.
This may appear as a pulsation but can
lead to failure of the support tube in ex-
treme cases.
Ower (1937) developed a theory for a
vane anemometer, showed that it overesti-
mated average air speed, and obtained an
expression for the error. Experiments con-
firmed the theoretical conclusions.
Jepson (1967) investigated the effect
of pulsating flow on current meters and
concluded that fluctuations of the veloc-
ity vector parallel to the mean flow al-
ways cause overestimation, whereas fluctu-
ations perpendicular generally cause under-
registration. He suggested that errors could
be reduced by
Figure 18.7. Paddle-wheel-type flow sensor (repro-
duced with permission of Peek Measurement).