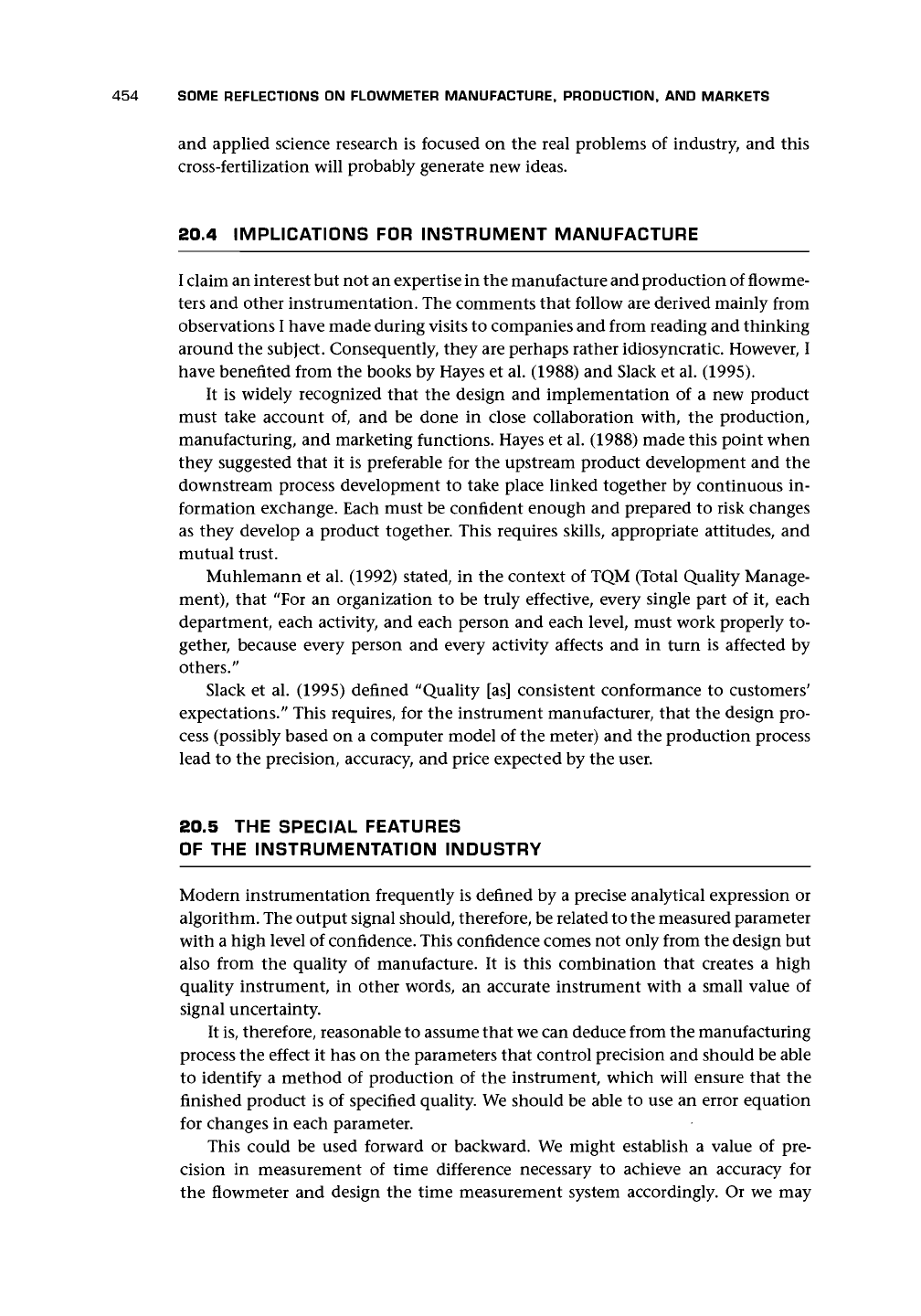
454 SOME REFLECTIONS ON FLOWMETER MANUFACTURE, PRODUCTION, AND MARKETS
and applied science research is focused on the real problems of industry, and this
cross-fertilization will probably generate new ideas.
20.4 IMPLICATIONS FOR INSTRUMENT MANUFACTURE
I
claim an interest but not an expertise in the manufacture and production of flowme-
ters and other instrumentation. The comments that follow are derived mainly from
observations I have made during visits to companies and from reading and thinking
around the subject. Consequently, they are perhaps rather idiosyncratic. However, I
have benefited from the books by Hayes et al. (1988) and Slack et al. (1995).
It is widely recognized that the design and implementation of a new product
must take account of, and be done in close collaboration with, the production,
manufacturing, and marketing functions. Hayes et al. (1988) made this point when
they suggested that it is preferable for the upstream product development and the
downstream process development to take place linked together by continuous in-
formation exchange. Each must be confident enough and prepared to risk changes
as they develop a product together. This requires skills, appropriate attitudes, and
mutual trust.
Muhlemann et al. (1992) stated, in the context of TQM (Total Quality Manage-
ment),
that "For an organization to be truly effective, every single part of it, each
department, each activity, and each person and each level, must work properly to-
gether, because every person and every activity affects and in turn is affected by
others."
Slack et al. (1995) denned "Quality [as] consistent conformance to customers'
expectations." This requires, for the instrument manufacturer, that the design pro-
cess (possibly based on a computer model of the meter) and the production process
lead to the precision, accuracy, and price expected by the user.
20.5 THE SPECIAL FEATURES
OF THE INSTRUMENTATION INDUSTRY
Modern instrumentation frequently is denned by a precise analytical expression or
algorithm. The output signal should, therefore, be related to the measured parameter
with a high level of confidence. This confidence comes not only from the design but
also from the quality of manufacture. It is this combination that creates a high
quality instrument, in other words, an accurate instrument with a small value of
signal uncertainty.
It
is,
therefore, reasonable to assume that we can deduce from the manufacturing
process the effect it has on the parameters that control precision and should be able
to identify a method of production of the instrument, which will ensure that the
finished product is of specified quality. We should be able to use an error equation
for changes in each parameter.
This could be used forward or backward. We might establish a value of pre-
cision in measurement of time difference necessary to achieve an accuracy for
the flowmeter and design the time measurement system accordingly. Or we may