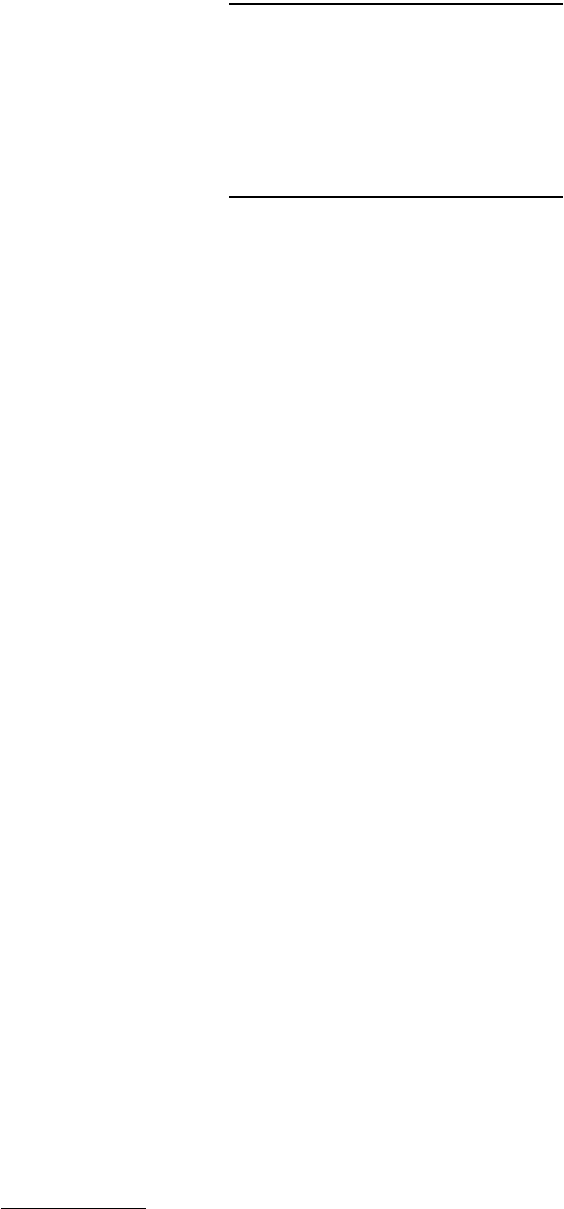
© 1999 by CRC Press LLC
15.2.2 Lattice Structures and Structural Defects
Crystalline as well as amorphous (disordered) materials are regularly used in MST. One important
material in micromechanics of the latter type is glass. Another important material is silicon dioxide, SiO
2
,
which is used in crystalline form (quartz) as well as in amorphous form (for instance, low-temperature
oxide, LTO). Also silicon and most other relevant materials can be grown in both forms. From a
mechanical-strength viewpoint, an amorphous structure is sometimes preferred, due to the lack of active
slip planes for dislocation movement in such structures. In general, however, the strength performance
is more related to the distribution and geometry of microscopic flaws in the material, especially surface
flaws.
It would lead too far in the present context to define all crystalline lattice structures of interest in MST.
For this reason we will confine ourselves to very brief descriptions of two important lattice types: the
diamond lattice type found in crystalline silicon and the zinc blend (ZnS) lattice type found in III-V
semiconductors.
The
diamond structure
is one of the simplest and most symmetric lattice types, and is found in Si and
Ge, for example. It consists of two face-centered cubic (fcc) lattices which are inserted into each other
in such a manner that they are shifted relative to each other by one quarter of a cube edge along all three
principal axes. Each atom is surrounded by four other atoms in a tetragonal configuration.
The
zinc blende structure
is found in III-V compounds such as GaAs, InP, and InSb. It is identical with
the diamond structure apart from the fact that one of the two overlapping fcc lattices consists entirely
of the type III element (e.g., Ga) and the other entirely of the type V element (e.g., As). Every atom of
one kind is tetragonally surrounded by four atoms of the other kind, and crystallographic planes of any
chosen orientation are periodically arranged in parallel pairs consisting of one III-type and one V-type
atomic plane (in some orientations the parallel planes of a pair coincide).
Common crystal defects are
point defects
such as vacancies (one atom is missing), substitutionals (one
atom is replaced by an impurity atom), or interstitials (one atom is “squeezed in” between the ordinary
atoms). Other frequent crystal imperfections are
line defects
, such as dislocations, and more
complex
defects
, such as stacking faults or twins. All types of lattice defects affect the mechanical properties of a
crystal to a greater or lesser extent, but dislocations are the most detrimental of the lattice defects from
a mechanical-strength viewpoint due to their extremely high mobility (when a critical load limit,
the
yield limit,
has been exceeded).
Beyond the basic crystalline lattice structure (and the various types of lattice defects that may be
present in it), a number of
superstructures
can be of major importance to the mechanical behavior. The
grain structure of a polycrystalline material is one superstructure influencing the hardness and the yield
limit of the material, and precipitates of impurities, alloying substances, or intermediary phases are other
examples. The size and shape distribution of geometric flaws, for instance, voids or cracks in the micron
or submicron range, is of crucial importance to the fracture strength of a brittle material. These super-
structures will be discussed in further detail in following sections.
Foreign atoms
of dopants, or contaminants such as oxygen, nitrogen, and carbon, commonly occur in
semiconductor materials, and are of great importance to their electronic properties (Hirsch, 1983;
TABLE 15.1
Melting Points (°C) of a Number
of Semiconductors and Other Materials
Si 1412 Nylon 137–150
Ge 937 Teflon 290
SiC 2537 Stainless steel 1400–1500
BN 4487 Al
2
O
3
2050
AlAs 1737 TiC 3100
GaAs 1238 HfC 3890
GaP 1467 SiO
2
1610
InP 1070 Glass ~700
InSb 536