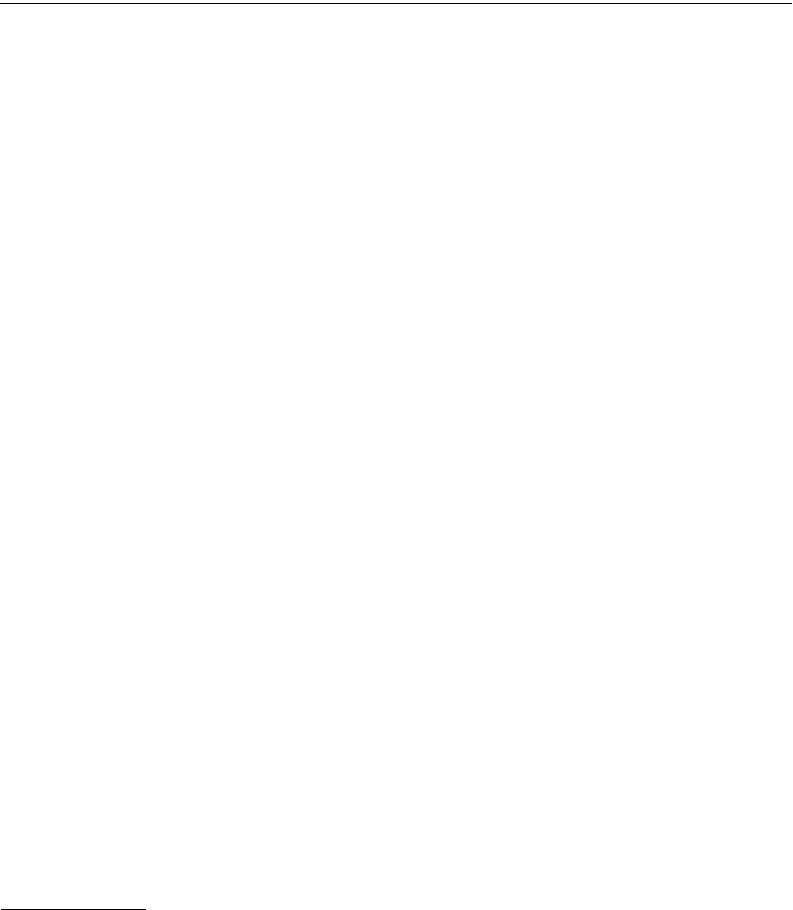
© 1999 by CRC Press LLC
is illustrated in terms of a reinforcement factor f, which is larger than unity for strengthening and lower
than unity for weakening (Johansson et al., 1989). From this table it is seen that magnetron-sputtered
TiN can have a disastrous effect on the strength of the beams, whereas Al deposited by the same method
has shown a somewhat strengthening effect in one case. It should be pointed out, however, that the effect
of an Al coating is temperature dependent. High deposition or annealing temperatures may cause
diffusion of Al into the Si substrate — so-called spiking — which is detrimental to the strength. This
effect can be avoided by special measures.
Various types of crack initiation in layer composites are discussed by Johansson et al. (1989) in terms
of the fracture toughness concept. Fracture toughnesses are not easily determined for thin coatings. There
are, however, two interesting reports on a fracture toughness measurement on a released polysilicon film
(Fan et al.,1990a; Kahn et al., 1996). In the experiment of Fan et al. (1990a) the test load was provided
by the internal stress of the system itself and in the other case by an external probe.
15.8 Testing
15.8.1 General Test Structures and Testing Methods
In micromechanical property characterization the most common specimen structures are free-standing
cantilever beams, bridges, or membranes. They are either a single-layer type, bulk or surface microma-
chined, or a two-layer type. In the latter case a thin substrate structure, e.g., a cantilever beam of silicon,
may have been produced by bulk or surface micromachining prior to the deposition of the film. Alter-
natively, the film can first be deposited on the whole wafer, and the two-layer test structure fabricated
by surface micromachining or combined surface and bulk micromachining.
Evaluation of elasticity properties, internal stresses, fracture properties, and, to some extent, plasticity
properties by measurements on micromachined structures is performed by three main methods: (1) static
deflection, i.e., a micromachined layer is deflected out-of-plane by external or internal forces, (2) static
tension or compression, i.e., the structure is longitudinally strained in its plane, and (3) dynamic testing,
usually of resonant structures, i.e., different modes of vibration are somehow excited in the structure.
Since the mechanical properties are of major concern within the field of MST, most measurements
using micromachined structures have been made on materials used for MST, primarily silicon. However,
investigations on polymers, metals, and ceramic materials have also been performed, and the present
subsection aims to review these. We start with static or quasi-static measuring techniques, then proceed
to dynamic testing.
15.8.2 Elasticity Testing by Static Techniques
Several different techniques for measuring elastic properties of micromachined structures have been
devised, for example, bending experiments on cantilever beams. Such experiments require high-resolu-
tion micromechanical test equipment capable of simultaneous measurement of applied force and beam
deflection on microsized specimens. Equipment capable of this is the Nanoindenter (Doerner et al., 1987;
Weihs et al., 1988, 1989; Hong et al., 1989; Vinci and Braveman, 1991; ) with a load resolution of 0.25 µN
and a displacement resolution of 0.2 nm.
Using the Nanoindenter on single-layer beams, E values in reasonable agreement with literature data
have been measured for Si, thermal and low-temperature SiO
2
, and for Au (Weihs et al., 1988, 1989).
The same technique has also been used to determine E values of nitride films in SiN
x
/SiO
2
two-layer
beams (Hong et al., 1989).
As will be further discussed below, from an error analysis viewpoint the best way to measure elastic
moduli is by direct tensile testing. Several investigations have been carried out in this field during the
last years. The most difficult part during a tensile test on a microscale is to measure the true strain in
the test specimen. A solution to that problem was presented by Sharpe et al. (1997) where thin gold lines
were deposited in a square shape onto surface-micromachined polysilicon test specimens. By using an