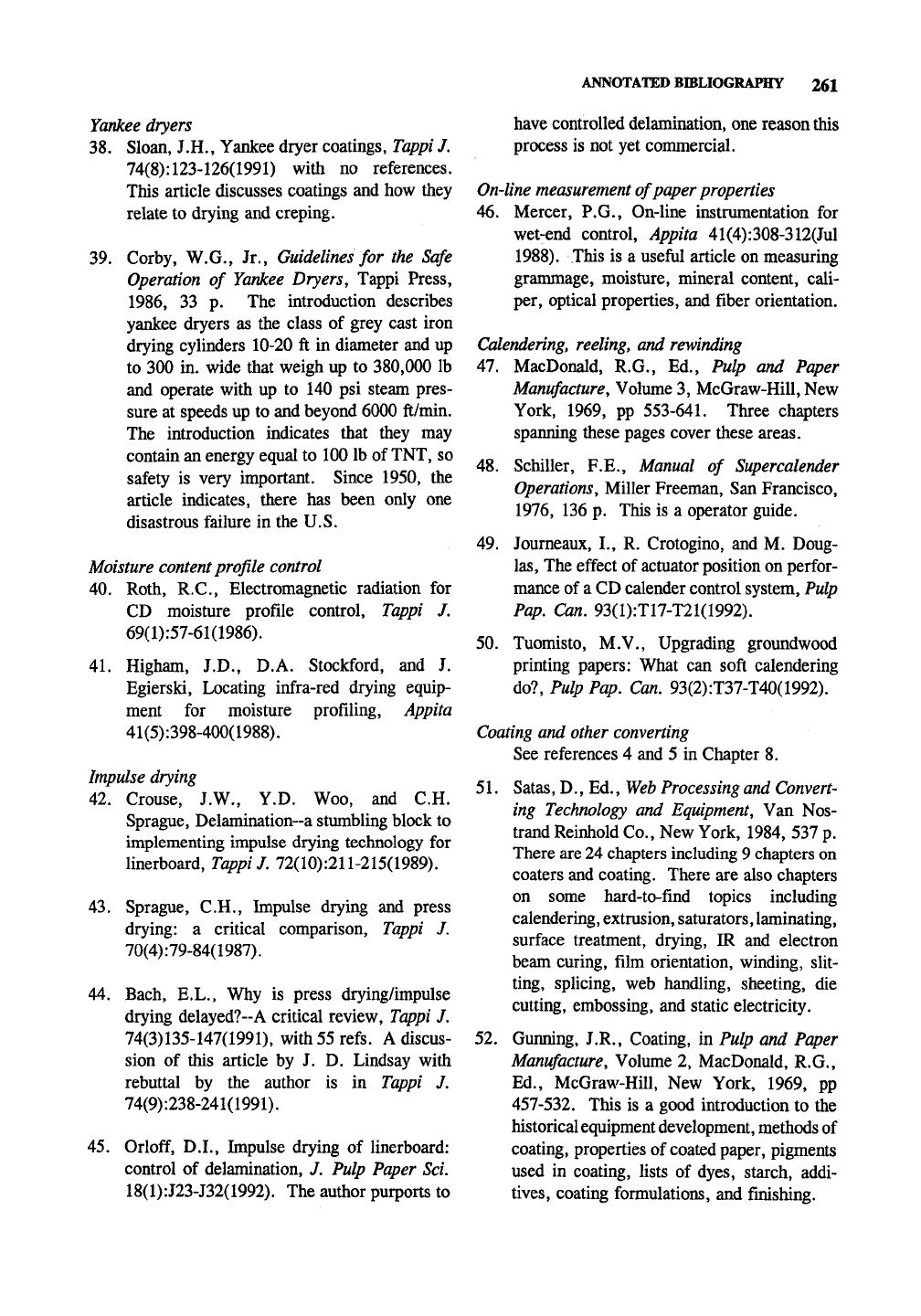
ANNOTATED BIBLIOGRAPHY 261
Yankee
dryers
38.
Sloan, J.H., Yankee dryer coatings,
Tappi
7.
74(8):
123-126(1991) with no references.
This article discusses coatings and how they
relate to drying and creping.
39.
Corby, W.G., Jr.,
Guidelines
for the Safe
Operation of Yankee Dryers, Tappi Press,
1986, 33 p. The introduction describes
yankee dryers as the class of grey cast iron
drying cylinders 10-20 ft in diameter and up
to 300 in. wide that weigh up to 380,000 lb
and operate with up to 140 psi steam pres-
sure at speeds up to and beyond 6000 ft/min.
The introduction indicates that they may
contain an energy equal to 100 lb of
TNT,
so
safety is very important. Since 1950, the
article indicates, there has been only one
disastrous failure in the U.S.
Moisture content profile control
40.
Roth, R.C., Electromagnetic radiation for
CD moisture profile control, Tappi J.
69(1):57-61(1986).
41.
Higham, J.D., D.A. Stockford, and J.
Egierski, Locating infra-red drying equip-
ment for moisture profiling, Appita
41(5):398-400(1988).
Impulse
drying
42.
Crouse, J.W., Y.D. Woo, and C.H.
Sprague, Delamination-a stumbling block to
implementing impulse drying technology for
linerboard,
Tappi
J.
72(10):211-215(1989).
43.
Sprague, C.H., Impulse drying and press
drying: a critical comparison, Tappi J.
70(4):79-84(1987).
44.
Bach, E.L., Why is press drying/impulse
drying delayed?-A critical review, Tappi J.
74(3)135-147(1991), with 55 refs. A discus-
sion of this article by J. D. Lindsay with
rebuttal by the author is in Tappi 7.
74(9):238-241(1991).
45.
Orloff,
D.L, Impulse drying of linerboard:
control of delamination, J. Pulp Paper Sci.
18(1):J23-J32(1992). The author purports to
have controlled delamination, one
reason
this
process is not yet commercial.
On-line measurement
of paper properties
46.
Mercer, P.O., On-line instrumentation for
wet-end control, Appita 41(4):308-312(Jul
1988).
This is a usefiil article on measuring
grammage, moisture, mineral content, cali-
per, optical properties, and fiber orientation.
Calendering,
reeling, and
rewinding
47.
MacDonald, R.G., Ed., Pulp and Paper
Manufacture,
Volume 3, McGraw-Hill, New
York, 1969, pp 553-641. Three chapters
spanning these pages cover these areas.
48.
Schiller, F.E., Manual of Supercalender
Operations, Miller Freeman, San Francisco,
1976, 136 p. This is a operator guide.
49.
Journeaux, I., R. Crotogino, and M. Doug-
las,
The effect of actuator position on perfor-
mance of
a
CD calender control system. Pulp
Pap.
Can. 93(1):T17-T21(1992).
50.
Tuomisto, M.V., Upgrading groundwood
printing papers: What can soft calendering
do?.
Pulp Pap. Can. 93(2):T37-T40(1992).
Coating
and other
converting
See references 4 and 5 in Chapter 8.
51.
Satas, D., Ed.,
Web Processing and
Convert-
ing Technology and Equipment, Van Nos-
trand Reinhold Co., New York, 1984, 537 p.
There are 24 chapters including 9 chapters on
coaters and coating. There are also chapters
on some hard-to-find topics including
calendering, extrusion,
saturators,
laminating,
surface treatment, drying, IR and electron
beam curing, film orientation, winding, slit-
ting, splicing, web handling, sheeting, die
cutting, embossing, and static electricity.
52.
Gunning, J.R., Coating, in Pulp and Paper
Manufacture,
Volume 2, MacDonald, R.G.,
Ed.,
McGraw-Hill, New York, 1969, pp
457-532.
This is a good introduction to the
historical
equipment
development, methods of
coating, properties of
coated
paper,
pigments
used in coating, lists of dyes, starch, addi-
tives,
coating formulations, and finishing.