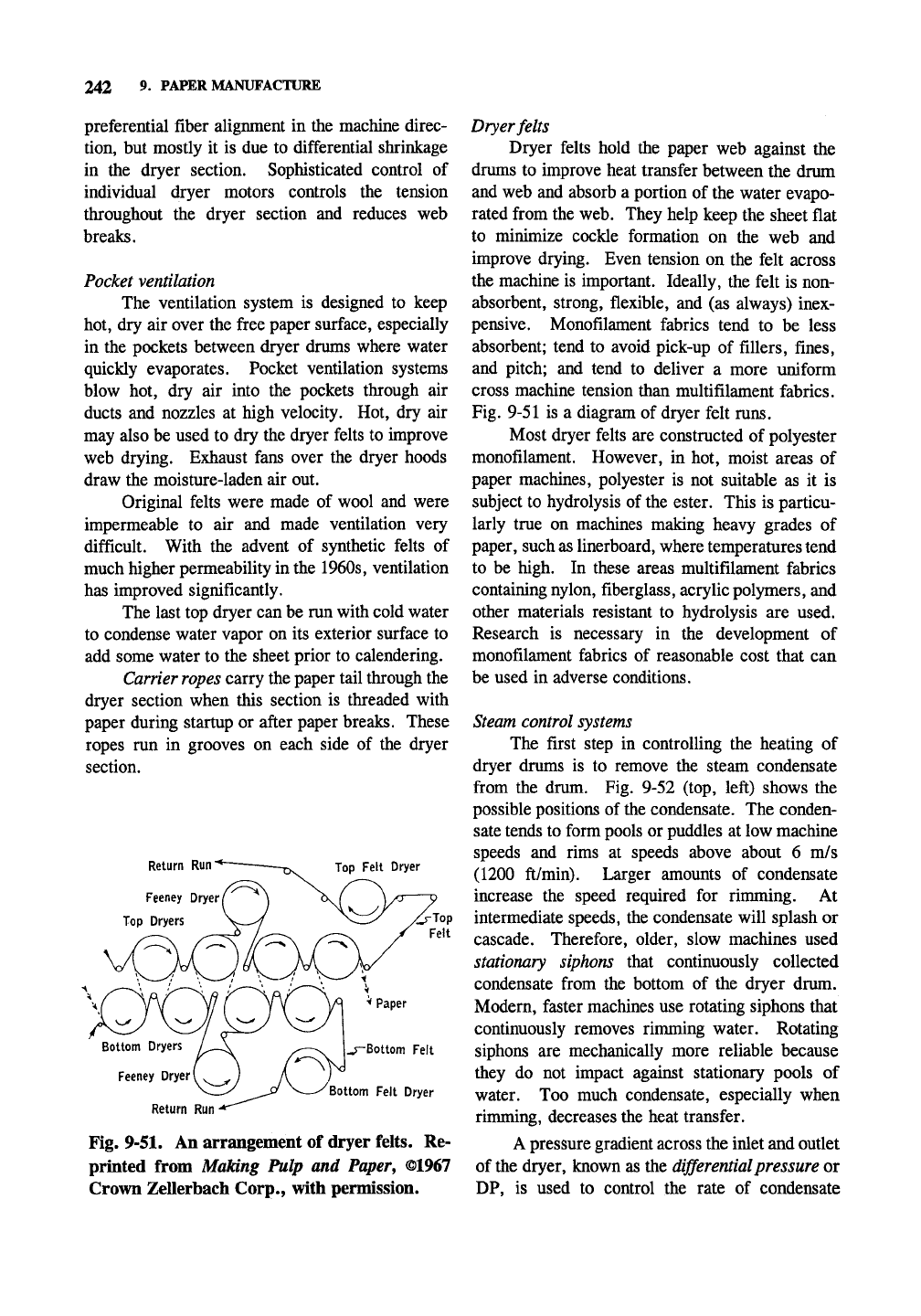
242
9,
PAPER MANUFACTURE
preferential fiber alignment in the machine direc-
tion, but mostly it is due to differential shrinkage
in the dryer section. Sophisticated control of
individual dryer motors controls the tension
throughout the dryer section and reduces web
breaks.
Pocket ventilation
The ventilation system is designed to keep
hot, dry air over the free paper surface, especially
in the pockets between dryer drums where water
quickly evaporates. Pocket ventilation systems
blow hot, dry air into the pockets through air
ducts and nozzles at high velocity. Hot, dry air
may also be used to dry the dryer felts to improve
web drying. Exhaust fans over the dryer hoods
draw the moisture-laden air out.
Original felts were made of wool and were
impermeable to air and made ventilation very
difficult. With the advent of synthetic felts of
much higher permeability in the 1960s, ventilation
has improved significantly.
The last top dryer can be run with cold water
to condense water vapor on its exterior surface to
add some water to the sheet prior to calendering.
Carrier
ropes
carry the paper tail through the
dryer section when this section is threaded with
paper during startup or after paper breaks. These
ropes run in grooves on each side of the dryer
section.
Return
Run
Top Felt Dryer
Bottom Dryers
Feeney Dryer
Return
Run
^r-Bottom Felt
Bottom Felt Dryer
Fig. 9-51. An arrangement of dryer felts. Re-
printed from Making Pulp and
Paper^
©1967
Crown Zellerbach Corp., with permission.
Dryerfelts
Dryer felts hold the paper web against the
drums to improve heat transfer between the drum
and web and absorb a portion of the water evapo-
rated from the web. They help keep the sheet flat
to minimize cockle formation on the web and
improve drying. Even tension on the felt across
the machine is important. Ideally, the felt is non-
absorbent, strong, flexible, and (as always) inex-
pensive. Monofilament fabrics tend to be less
absorbent; tend to avoid pick-up of fillers, fines,
and pitch; and tend to deliver a more uniform
cross machine tension than multifilament fabrics.
Fig. 9-51 is a diagram of dryer felt runs.
Most dryer felts are constructed of polyester
monofilament. However, in hot, moist areas of
paper machines, polyester is not suitable as it is
subject to hydrolysis of the ester. This is particu-
larly true on machines making heavy grades of
paper, such
as
linerboard, where temperatures tend
to be high. In these areas multifilament fabrics
containing nylon, fiberglass, acrylic polymers, and
other materials resistant to hydrolysis are used.
Research is necessary in the development of
monofilament fabrics of reasonable cost that can
be used in adverse conditions.
Steam control systems
The first step in controlling the heating of
dryer drums is to remove the steam condensate
from the drum. Fig. 9-52 (top, left) shows the
possible positions of the condensate. The conden-
sate tends to form pools or puddles at low machine
speeds and rims at speeds above about 6 m/s
(1200 ft/min). Larger amounts of condensate
increase the speed required for rimming. At
intermediate speeds, the condensate will splash or
cascade. Therefore, older, slow machines used
stationary siphons that continuously collected
condensate from the bottom of the dryer drum.
Modern, faster machines use rotating siphons that
continuously removes rimming water. Rotating
siphons are mechanically more reliable because
they do not impact against stationary pools of
water. Too much condensate, especially when
rimming, decreases the heat transfer.
A pressure gradient across the inlet and outlet
of the dryer, known as the differential pressure or
DP,
is used to control the rate of condensate