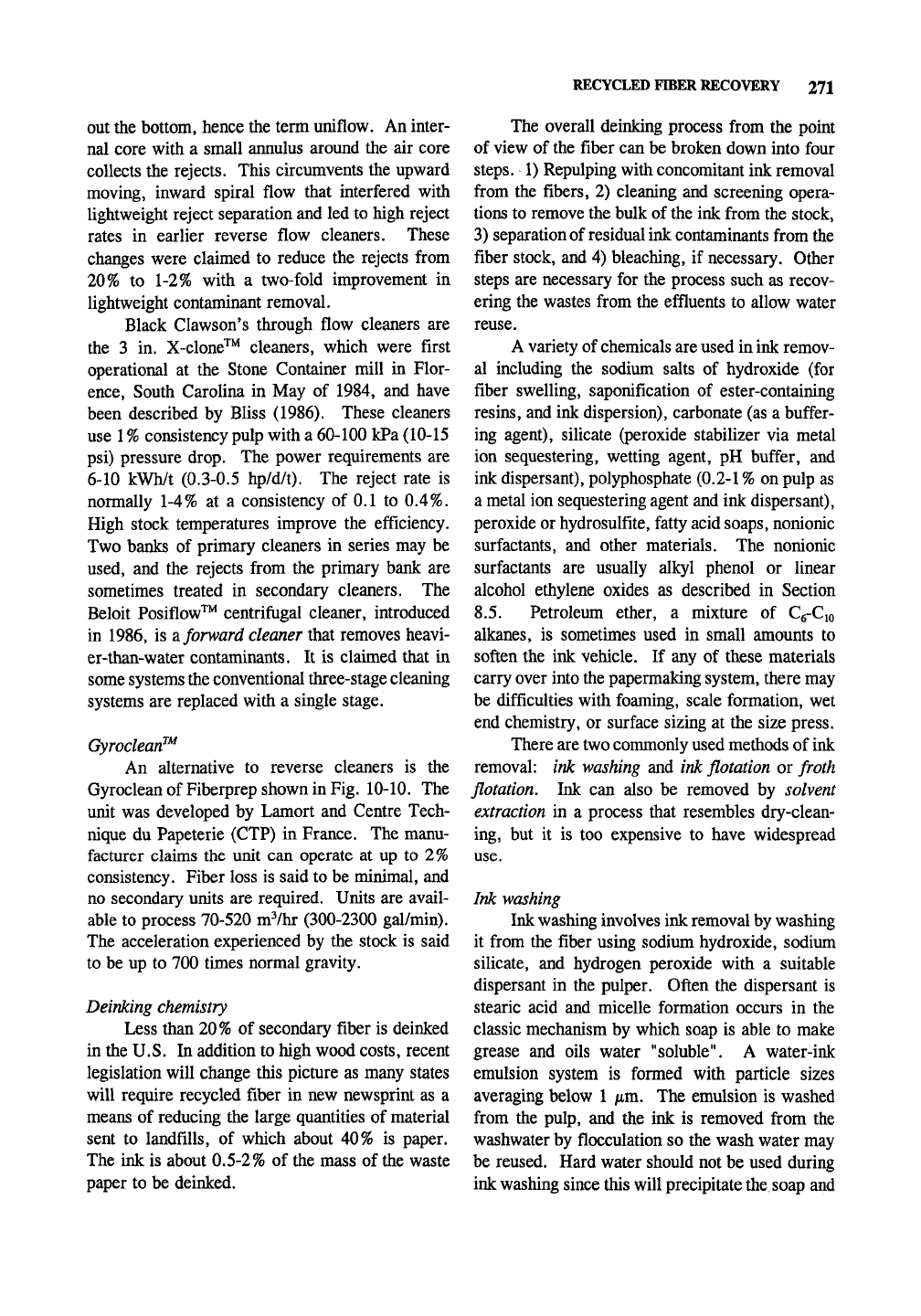
RECYCLED FIBER RECOVERY 271
out the bottom, hence the term uniflow. An inter-
nal core with a small annulus around the air core
collects the rejects. This circumvents the upward
moving, inward spiral flow that interfered with
lightweight reject separation and led to high reject
rates in earlier reverse flow cleaners. These
changes were claimed to reduce the rejects from
20%
to 1-2% with a two-fold improvement in
lightweight contaminant removal.
Black Clawson's through flow cleaners are
the 3 in. X-clone'^^ cleaners, which were first
operational at the Stone Container mill in Flor-
ence,
South Carolina in May of 1984, and have
been described by Bliss (1986). These cleaners
use
1 %
consistency pulp with a 60-100 kPa (10-15
psi) pressure drop. The power requirements are
6-10 kWh/t (0.3-0.5 hp/d/t). The reject rate is
normally 1-4% at a consistency of 0.1 to 0.4%.
High stock temperatures improve the efficiency.
Two banks of primary cleaners in series may be
used, and the rejects from the primary bank are
sometimes treated in secondary cleaners. The
Beloit Posiflow"^^ centrifugal cleaner, introduced
in 1986, is
SL
forward cleaner that removes heavi-
er-than-water contaminants. It is claimed that in
some systems the conventional three-stage cleaning
systems are replaced with a single stage.
Gyrodean™
An alternative to reverse cleaners is the
Gyroclean of Fiberprep shown in Fig. 10-10. The
unit was developed by Lamort and Centre Tech-
nique du Papeterie (CTP) in France. The manu-
facturer claims the unit can operate at up to 2%
consistency. Fiber loss is said to be minimal, and
no secondary units are required. Units are avail-
able to process 70-520 mVhr (300-2300 gal/min).
The acceleration experienced by the stock is said
to be up to 700 times normal gravity.
Deinking chemistry
Less than 20% of secondary fiber is deinked
in the U.S. In addition to high wood costs, recent
legislation will change this picture as many states
will require recycled fiber in new newsprint as a
means of reducing the large quantities of material
sent to landfills, of which about 40% is paper.
The ink is about 0.5-2% of the mass of the waste
paper to be deinked.
The overall deinking process from the point
of view of the fiber can be broken down into four
steps.
1) Repulping with concomitant ink removal
from the fibers, 2) cleaning and screening opera-
tions to remove the bulk of the ink from the stock,
3) separation of residual ink contaminants from the
fiber stock, and 4) bleaching, if necessary. Other
steps are necessary for the process such as recov-
ering the wastes from the effluents to allow water
reuse.
A variety of chemicals are used in ink remov-
al including the sodium salts of hydroxide (for
fiber swelling, saponification of ester-containing
resins,
and ink dispersion), carbonate (as a buffer-
ing agent), silicate (peroxide stabilizer via metal
ion sequestering, wetting agent, pH buffer, and
ink dispersant), polyphosphate
(0.2-1 %
on pulp as
a metal ion sequestering agent and ink dispersant),
peroxide or hydrosulfite, fatty acid soaps, nonionic
surfactants, and other materials. The nonionic
surfactants are usually alkyl phenol or linear
alcohol ethylene oxides as described in Section
8.5. Petroleum ether, a mixture of Cg-Cio
alkanes, is sometimes used in small amounts to
soften the ink vehicle. If any of these materials
carry over into the papermaking system, there may
be difficulties with foaming, scale formation, wet
end chemistry, or surface sizing at the size press.
There are two commonly used methods of ink
removal: ink washing and ink flotation ov froth
flotation. Ink can also be removed by solvent
extraction in a process that resembles dry-clean-
ing, but it is too expensive to have widespread
use.
Ink washing
Ink washing involves ink removal by washing
it from the fiber using sodium hydroxide, sodium
silicate, and hydrogen peroxide with a suitable
dispersant in the pulper. Often the dispersant is
stearic acid and micelle formation occurs in the
classic mechanism by which soap is able to make
grease and oils water "soluble". A water-ink
emulsion system is formed with particle sizes
averaging below 1 fim. The emulsion is washed
from the pulp, and the ink is removed from the
washwater by flocculation so the wash water may
be reused. Hard water should not be used during
ink washing since this will precipitate the soap and