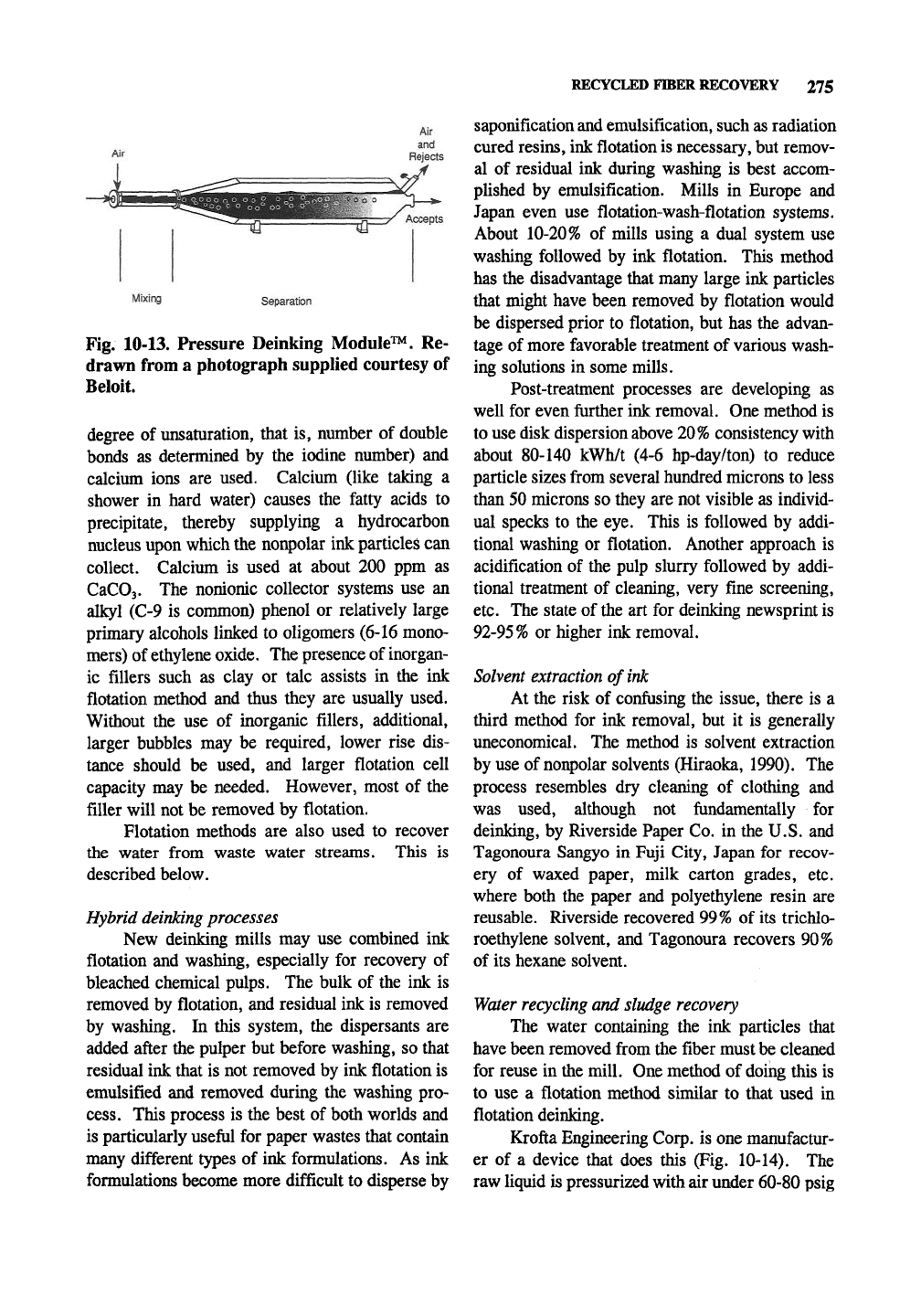
RECYCLED FIBER RECOVERY 275
Mixing
Separation
Fig. 10-13. Pressure Deinking Module™. Re-
drawn from a photograph supplied courtesy of
Beloit.
degree of unsaturation, that is, number of double
bonds as determined by the iodine number) and
calcium ions are used. Calcium (like taking a
shower in hard water) causes the fatty acids to
precipitate, thereby supplying a hydrocarbon
nucleus upon which the nonpolar ink particles can
collect. Calcium is used at about 200 ppm as
CaCOj.
The nonionic collector systems use an
alkyl (C-9 is common) phenol or relatively large
primary alcohols linked to oligomers (6-16 mono-
mers) of ethylene oxide. The presence of inorgan-
ic fillers such as clay or talc assists in the ink
flotation method and thus they are usually used.
Without the use of inorganic fillers, additional,
larger bubbles may be required, lower rise dis-
tance should be used, and larger flotation cell
capacity may be needed. However, most of the
filler will not be removed by flotation.
Flotation methods are also used to recover
the water from waste water streams. This is
described below.
Hybrid
deinking
processes
New deinking mills may use combined ink
flotation and washing, especially for recovery of
bleached chemical pulps. The bulk of the ink is
removed by flotation, and residual ink is removed
by washing. In this system, the dispersants are
added after the pulper but before washing, so that
residual ink that is not removed by ink flotation is
emulsified and removed during the washing pro-
cess.
This process is the best of both worlds and
is particularly useful for paper wastes that contain
many different types of ink formulations. As ink
formulations become more difficult to disperse by
saponification and emulsification, such as radiation
cured resins, ink flotation is necessary, but remov-
al of residual ink during washing is best accom-
plished by emulsification. Mills in Europe and
Japan even use flotation-wash-flotation systems.
About 10-20% of mills using a dual system use
washing followed by ink flotation. This method
has the disadvantage that many large ink particles
that might have been removed by flotation would
be dispersed prior to flotation, but has the advan-
tage of more favorable treatment of various wash-
ing solutions in some mills.
Post-treatment processes are developing as
well for even fiirther ink removal. One method is
to use disk dispersion above 20% consistency with
about 80-140 kWh/t (4-6 hp-day/ton) to reduce
particle sizes from several hundred microns to less
than 50 microns so they are not visible as individ-
ual specks to the eye. This is followed by addi-
tional washing or flotation. Another approach is
acidification of the pulp slurry followed by addi-
tional treatment of cleaning, very fine screening,
etc.
The state of the art for deinking newsprint is
92-95%
or higher ink removal.
Solvent extraction of
ink
At the risk of confiising the issue, there is a
third method for ink removal, but it is generally
uneconomical. The method is solvent extraction
by use of nonpolar solvents (Hiraoka, 1990). The
process resembles dry cleaning of clothing and
was used, although not fundamentally for
deinking, by Riverside Paper Co. in the U.S. and
Tagonoura Sangyo in Fuji City, Japan for recov-
ery of waxed paper, milk carton grades, etc.
where both the paper and polyethylene resin are
reusable. Riverside recovered 99% of its trichlo-
roethylene solvent, and Tagonoura recovers 90%
of its hexane solvent.
Water recycling and sludge recovery
The water containing the ink particles that
have been removed from the fiber must
be
cleaned
for reuse in the mill. One method of doing this is
to use a flotation method similar to that used in
flotation deinking.
Krofta Engineering Corp. is one manufactur-
er of a device that does this (Fig. 10-14). The
raw liquid is pressurized with air under 60-80 psig