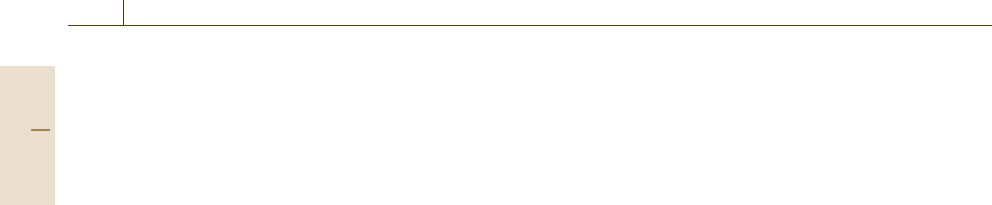
392 Part C Materials Properties Measurement
In the case of steel, E is nearly 200 GPa and ν is ap-
proximately 0.3. The elastic strain in steels is usually
less than 1%, which is very small compared with the
uniform elongation of the order of 10%. We note here
that the constant-volume assumption is not applicable
to elastic deformation.
Yield Strength
Special measurements such as those based on strain
gages are required for the measurement of elastic strains
less than 0.01 so that the yield strength (YS)isde-
termined for mechanical design using the conventional
tensile test. In the case of discontinuous yielding ob-
served in mild steel, as shown in Fig. 7.38a, the upper or
lower yield point is observed on the stress–strain curve
and used as the yield strength in engineering. After the
upper yield point, a plastic-deformation regime called
the Luders band appears and spreads within the speci-
men gage volume under the lower yield stress. Since the
upper yield strength is strongly dependent on the ten-
sile speed, i. e., the strain rate, the lower yield strength
is more popularly used. The strain during this hetero-
geneous deformation is called the Luders elongation,
which is also dependent on grain size.
On the other hand, Fig. 7.38b shows the case of
continuous yielding, which is observed in many met-
als and alloys such as aluminum, austenitic stainless
steel etc. 0.2% proof stress is usually employed, which
means a plastic (permanent) strain of 0.2% remains af-
ter unloading. Usually the elastic linear line is shifted by
0.2% and the intersection with the stress–strain curve is
found. Macroscopic yielding can be observed to take
place at this point. Although 0.2% strain is the choice
for engineering, other strains, for instance 0.1%, are
employed in other industrial fields.
Tensile Strength
The maximum stress appearing in Fig. 7.38 is deter-
mined by the tensile strength (TS), frequently called the
ultimate tensile strength (UTS). In the case of an ex-
treme design that allows plastic flow, TS is employed as
the design strength.
Ductility
Parameters to describe the ductility includes uniform
elongation, total elongation and reduction in area af-
ter fracture. Uniform elongation is important for plastic
forming etc. and is determined as the strain at the tensile
strength. After the tensile strength, local deformation,
i. e. necking, starts. The total strain is given as the strain
to fracture in Fig. 7.41. It should be noted that the to-
tal elongation is dependent on the gage length adopted.
Therefore, fracture strain (ε
f
) is sometimes used, which
is defined as ln(A
0
/A
f
), where A
f
refers to the smallest
area in the necked region after fracture. Conventionally,
the reduction in area (ϕ)definedby[(A
0
− A
f
)/A
0
]×
100% is used. The extreme case observed in a pure
metal is a point fracture, where A
f
=0.
Workhardening Exponent (n-Value)
The true stress–strain curve shown in Fig. 7.41 is often
fitted by using the following Hollomon’s equation
σ
∗
= K(ε
∗
)
n
, (7.53)
where K and n stand for the strengthening factor
and the workhardening exponent (n-value), respec-
tively. By taking two measuring points or by using
the least-squares method for ln σ
∗
versus ln ε
∗
within
an appropriate strain regime, these K and n values
are determined. The n-value is important because it is
equivalent with uniform elongation. The plastic insta-
bility condition, i. e., the onset of necking can be given
by
dF = σ
∗
dA + A dσ
∗
=0 , (7.54)
where F is the applied tensile load. This equation
is rewritten by σ
∗
= dσ
∗
/dε
∗
under the assumption
of constant volume and therefore ε
∗
= n is obtained.
Alargen-value means excellent plastic formability.
Rankford Value (Plastic Anisotropy: r-Value)
Another parameter that indicates the plastic formability,
and which is also obtained by the tension test for sheet
metals and alloys, is the r-value. When tensile strain
reaches 10–20%, the strain for a thickness of ε
t
and the
strain for a width of ε
w
are measured and the r-value is
determined by
r =ε
w
/ε
t
. (7.55)
If the assumption of constant volume is used, this be-
comes
r =ln(W
0
/W)/ ln(LW/L
0
W
0
) , (7.56)
where W
0
, L
0
and W, L refer to the width and gage
length in the tensile direction before and after the ten-
sion test, respectively. These values are much more eas-
ily measured precisely than the thickness because most
cases use thin sheets. In an isotropic material, the r-value
equals unity. Commercially available materials gener-
ally show anisotropic feature in plastic flow because of
their texture. Materials with high r-values are desirable
Part C 7.4