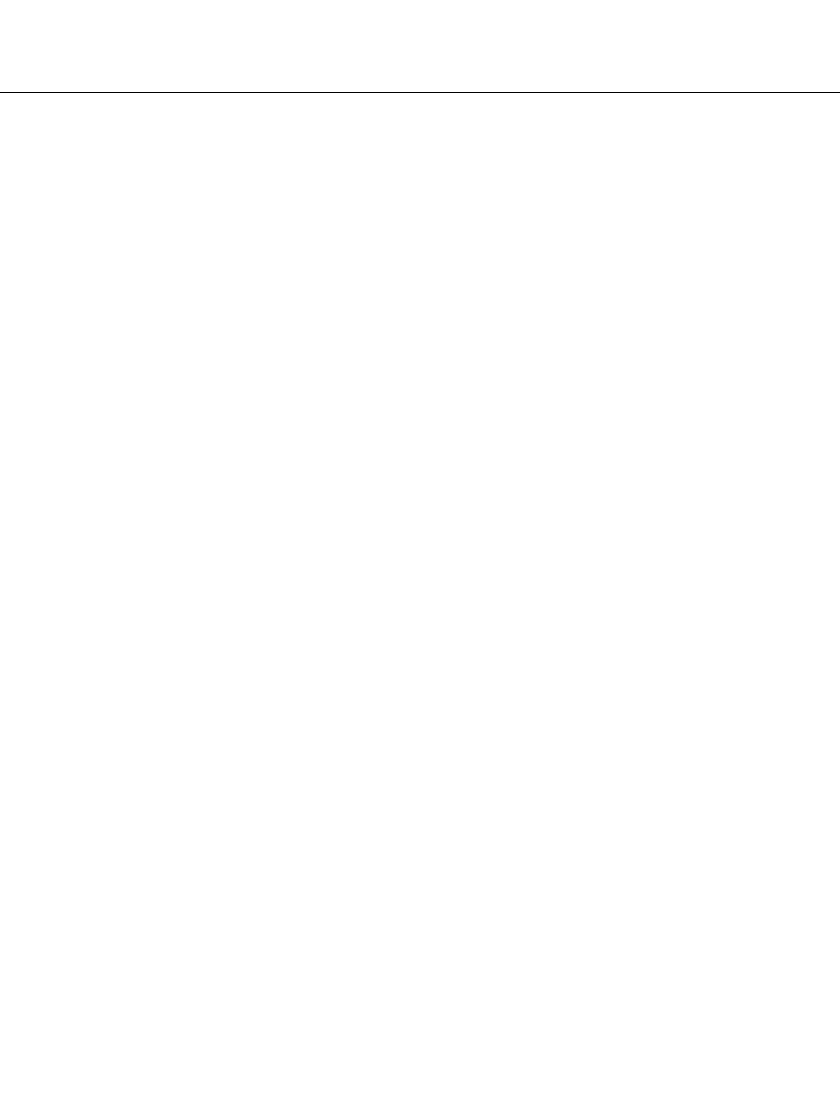
23.54 CHAPTER TWENTY-THREE
23.6 STATIONARY BATTERIES: CONSTRUCTION AND
PERFORMANCE
23.6.1 Construction
Designs for stationary batteries have changed much more slowly than those for SLI and
traction batteries. This is not surprising in light of the much longer service life of the sta-
tionary batteries. Heavy, thick plates (including Plante´ as well as pasted Faure and tubular
positives) with high paste density are generally used.
24
Curing is very important, and pasted
plates are usually carefully dried to prevent cracks and degradation of the grid-paste interface.
The stationary battery is designed with excess electrolyte (highly flooded) to minimize
maintenance and the watering interval and is generally positive-plate-limited in capacity
(compared with traction batteries, for example, which are electrolyte- or acid-limited). The
stationary batteries are capable of being floated and moderately overcharged.
The thick-plate design of stationary batteries reflects the fact that high energy and power
densities are not as necessary as is the case for SLI and traction batteries. The overcharge
operation of stationary batteries requires a large electrolyte volume (which can be accom-
modated as the batteries are mounted in fixed positions) and usually nonantimonial lead grids
(to maximize the intervals between watering). The overcharge causes some positive-grid
corrosion, and this is manifested as ‘‘growth’’ or expansion of the grid. The dimensions from
the positive plate to the inside container are scaled so that the positives can grow by up to
10% before the plates touch the container walls. If the growth is greater than 10%, the active
material is sufficiently loose on the grid so that the capacity becomes severely positive-
limited and the battery must be replaced.
The positives are usually supported from hanging lugs or nonconductive rods, which are
borne by the tops of the negatives. The containers are usually transparent thermoplastics
(acrylonitrile-butadiene-styrene, styrene-acrylonitrile resin, polycarbonate, PVC), but some
small stationary batteries are built in translucent polyolefin containers similar to those used
for SLI batteries. The stationary batteries were the first application for flame-retardant vent
caps which are now also standard on most SLI batteries.
The positive plate has the greater influence on the performance and life of the battery. A
variety of positives are used, depending as much on tradition and custom as on the perform-
ance characteristics. The flat-pasted stationary batteries are popular in the United States
because of their lower costs, lower maintenance, and lower generation of hydrogen. Lead-
calcium tubular plates are now being introduced. For most of the standby emergency appli-
cations the grids are cast in lead-calcium alloy. Plante´ and tubular designs are popular in
Europe because of their longer life. All stationary batteries today use pasted negative plates
generally with n positive plates and n
⫹ 1 negative plates (outside-negative design). This is
done because of the need for proper support of the positives, which tend to grow or expand
during their life. One design used by some manufacturers is to make the two outermost
negative plates thinner than the inside negative plates because the outermost surfaces are not
easily recharged. Figure 23.35 is an illustration of a stationary battery system installation.
A significantly different approach to stationary battery design is the cylindrically shaped
battery of Lucent Technologies (formerly AT&T Bell Laboratories).
25,26
Traditionally, pris-
matic-shaped stationary batteries had failed after 5 to 20 years of service in telephone sys-
tems. The battery, illustrated in Fig. 23.36, incorporates a number of innovations in order to
achieve a battery life initially predicted to be 30 years or longer. These include lattice-type
circular-shaped pure lead grids (cupped at a 10
⬚ angle), plates stacked horizontally one above
the other instead of in the conventional vertical construction, chemically produced tetrabasic
lead sulfate (TTB) positive paste, positives welded around the external plate circumference,
negatives welded to a central conductor core, and heat-sealed copolymer container and cover.
The use of pure lead in place of lead-calcium is to reduce positive-plate grid growth; the