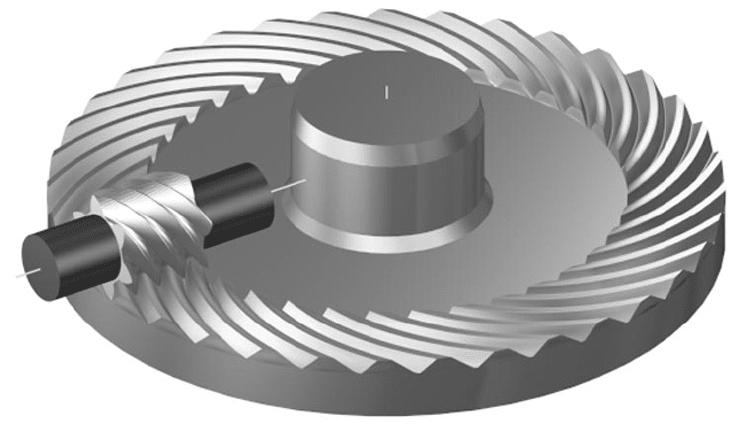
NASA RP–1406 71
2.7 Face Worm-Gear Drives
The face-gear drives discussed in this section were formed by a cylindrical or conical worm and a face gear.
These types of gear drives were invented by O.E. Saari and are described in Saari (1954, 1960). They were the
subject of research conducted by the inventor and other researchers whose results are presented in Goldfarb and
Spiridonov (1996), Kovtushenko, Lagutin, and Yatsin (1994), and in many other papers. This section presents
the results of research conducted at the Gear Research Laboratory of the University of Illinois at Chicago by
F.L. Litvin, A. Egelja, and M. De Donno. The goals of the research projects were (1) to provide a computerized
design that enables one to avoid the undercutting and pointing of face worm gears, (2) to effect the localization
of bearing contact, and (3) to accomplish a reduction in magnitude and a transformation of the shape of the
transmission error function into a favorable one (see section 1.14). The cause of the the transmission errors was
considered to be misalignment. Special attention was given to the simulation of meshing and the contact of
misaligned gear drives by developed TCA (Tooth Contact Analysis) computer programs.
Saari’s invention was limited to the application of ZA-worms (with straight-line profiles in the axial section)
and the transformation of rotation between crossed axes only. The research of Litvin, Egelja, and
De Donno was extended to the application of other types of worm thread surfaces and the transformation of
rotation between intersected axes (in addition to the case of the crossed axes of rotation).
Figures 2.7.1 and 2.7.2 show respectively (1) a face worm-gear drive with a cylindrical worm and intersected
axes of rotation and (2) a face worm-gear drive with a conical worm and crossed axes of rotation.
We have to emphasize that pointing is much easier to avoid in face worm-gear drives in comparison with
conventional face-gear drives because of the application of screw thread surfaces with different pressure angles
for the driving and coast tooth sides and relatively small lead angle values. The width of the topland of a face
worm-gear varies in a permissible range and does not equal zero.
A detailed investigation to detect singularities based on the ideas presented in sections 1.4, 1.6, and 1.7
enabled us to discover that the singular points on a face worm-gear tooth surface form an envelope E
r
to the
contact lines that is simultaneously the edge of regression (fig. 2.7.3). Eliminating E
r
from the surface of the
face gear guarantees the avoidance of undercutting.
One of the important problems in designing face worm-gear drives is the localization of bearing contact and
the predesign of a parabolic function of transmission errors. Based on the initial results of completed
investigations, the authors of these research projects consider a promising solution to be the combination of
profile and longitudinal deviations of the worm thread surface. These deviations are with respect to the
Figure 2.7.1.—Face worm-gear drive with intersected axes.