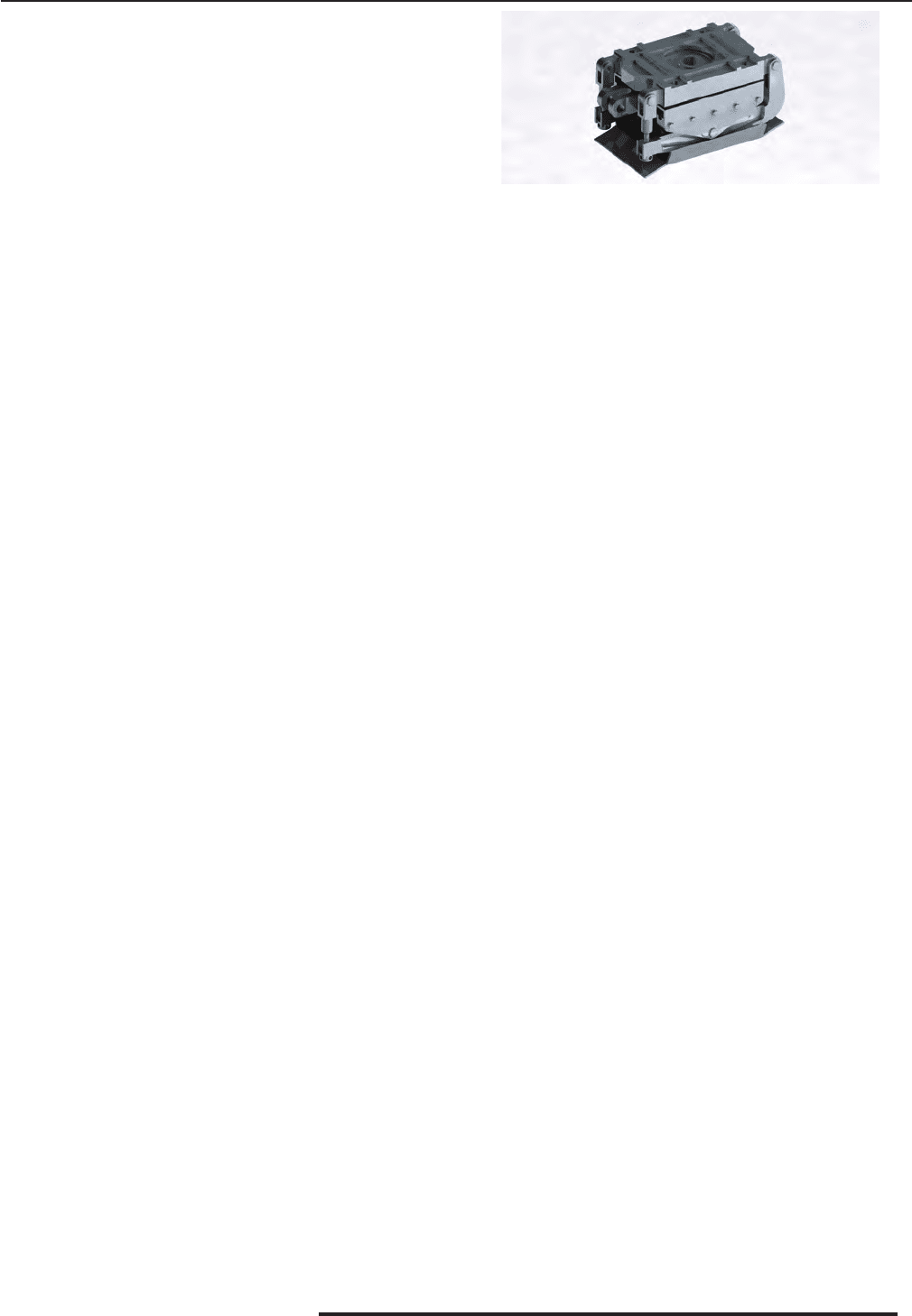
I l%2 ++30#(7%1* ? ( #.0-.03$- ? /0.,;8+%--.12</2010
2
182
МАШИНОВЕДЕНИЕ
вижной плиты позволяет увеличить минимум в 3
раза площадь ее рабочей поверхности, перекрываю-
щей в процессе работы затвора сталевыпускное от-
верстие конвертера, что дает возможность во столь-
ко же раз повысить кратность применения шиберного
устройства до очередной замены. Электромеханиче-
ский привод затвора, связанный с помощью кардан-
ного вала с тихоходной конической зубчатой пере
да-
чей, закреплен на днище корпуса конвертера и поэ-
тому не подвержен интенсивному тепловому воздей-
ствию [5].
Резкое сокращение межплавочного периода ду-
говых сталеплавильных печей, функционирующих в
комплексе с установками «ковш-печь» и высокоско-
ростными МНЛЗ, обеспечивающими литье заготовок
длинными сериями, потребовало уменьшения про-
должительности подготовки к работе разливочных
устройств с 3 ч до 25–30 мин. Эт
о стало возможным с
разработкой шиберных затворов кассетного типа, по-
зволяющих существенно повысить оборачиваемость
ковшей за счет возможности замены отработанного
комплекта огнеупорных изделий без снятия затвора с
ковша и отправки его в шиберную мастерскую. При
создании таких разливочных систем учитывали то
обстоятельство, что из-за увеличения продолжитель-
ности нах
ождения металлического расплава в ковше
в случае выполнения в нем технологических опера-
ций по раскислению, легированию и рафинированию
возникают значительные деформации деталей затво-
ра, вызванные их нагревом. Поэтому опорные узлы
подвижной части затвора должны не только обеспе-
чивать компенсацию этих деформаций, а и сохранять
надежный контакт рабочих поверхностей огнеупор-
ных плит, исклю
чающий появление зазора между
ними даже в случае действия расклинивающей силы,
возникающей во время разрушения подвижной пли-
той металлической корочки, часто образующейся на
стенках сталевыпускного канала.
Предотвращение коробления деталей в условиях
интенсивного теплового воздействия в новых ковшо-
вых затворах, разработанных специалистами запад-
ноевропейских фирм, достигнуты путем примене-
ния массивных и ж
естких корпусов коробчатой фор-
мы, изготовленных из жаропрочной стали. Задача по
обеспечению постоянного и равномерного прижатия
огнеупорных плит в них решена за счет использова-
ния блоков тарельчатых или витых пружин, воздей-
ствующих непосредственно или через специальные
рычаги на опорные элементы подвижной обоймы и
охлаждаемых воздухом, который подают под избы-
точным давлением из це
ховой сети. При этом затво-
ры рассчитаны на комплектацию огнеупорными из-
делиями, отвечающими достаточно жестким требова-
ниям по предельным отклонениям размеров (не бо-
лее 0,1 мм). Такие затворы отличает высокая цена (от
20 до 30 тыс. долл. США), сложность в обслужива-
нии и эксплуатации, обусловленная необходимостью
воздушного охлаждения во время разливки и по
сто-
янного контроля на специальных стендах жесткости
пружин, а также их частой заменой из-за утра-
ты упругих свойств или механического разрушения.
Для выполнения замены вышедших из строя пружин
необходим демонтаж затвора с разливочного ковша,
поскольку упругие элементы размещены в раме раз-
ливочного устройства. Выполнение указанной ре-
монтной операции требует допо
лнительного време-
ни, что негативно сказывается на цикличности про-
цесса подготовки системы затвора к работе. В связи с
этим, в последних модификациях кассетных затворов
западных фирм для облегчения доступа к элементам
прижатия подвижной откидной каретки предусмо-
трена возможность отворота в сторону и самой рамы,
что привело к увеличению массы разливочной систе-
мы в цело
м [6].
Поэтому при создании отечественных кассетных
затворов нового поколения был выбран иной концеп-
туальный подход, основанный на реализации прин-
ципа рациональности проектируемой механической
системы, предполагающего уменьшение до миниму-
ма избыточных (пассивных) связей в кинематической
схеме разливочного устройства (рис. 3). Этого до-
стигли благодаря применению балансирных и шар-
нирных систем прижа
тия подвижной обоймы и раз-
мещению ее на двух линейных подшипниках каче-
ния, что обеспечило самоустановку нижней огнеу-
порной плиты относительно верхней и уменьшение
нагрузки на привод. Ослабления негативного влия-
ния теплового воздействия на работоспособность ме-
ханической системы ковшового затвора добились по-
средством применения полужесткого режима при-
жатия огнеупорных плит с по
мощью двух винтов
и специальных рычагов, допускающих значитель-
ные упругие деформации. При необходимости заме-
ны отработанного комплекта огнеупорных изделий
необходимо ослабить затяжку двух винтов и повер-
нуть подвижную часть затвора на 90
о
относительно
верхней обоймы, обеспечивая тем самым свободный
доступ к керамическим частям разливочного устрой-
ства, закрепленным в его металлических обоймах с
помощью элементов с резьбой. После смены ком-
плекта огнеупоров сборку затвора осуществляют в
обратной последовательности, контролируя с помо-
щью динамометрического ключа требуемый момент
затяжки двух винтов, составляющий 100 Н
.
м.
Результаты промышленного опробования балан-
сирного затвора с болтовым прижатием плит подтвер-
дили правильность принятых технических решений,
позволивших использовать для изготовления разли-
вочного устройства конструкционную сталь взамен
Рис. 3. Ковшовый затвор кассетного типа с балансирной
системой прижатия огнеупорных плит