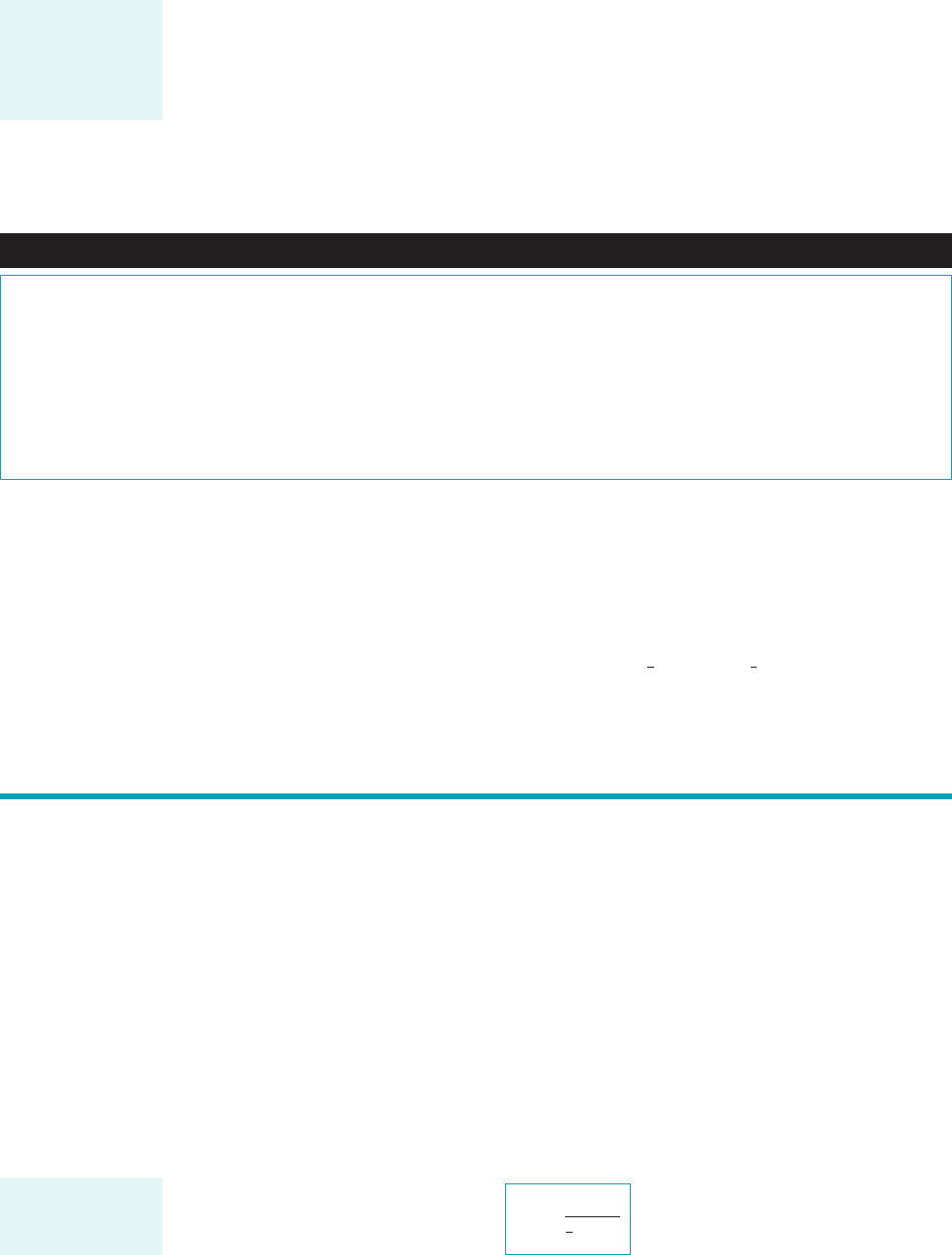
numerical calculations. As a result it is possible to predict the aerodynamic drag on cars of a wide
variety of body styles.
As is indicated in Fig. 9.27, the drag coefficient for cars has decreased rather continuously
over the years. This reduction is a result of careful design of the shape and the details 1such as
window molding, rear view mirrors, etc.2. An additional reduction in drag has been accomplished
by a reduction of the projected area. The net result is a considerable increase in the gas mileage,
especially at highway speeds. Considerable additional information about the aerodynamics of
road vehicles can be found in the literature 1Ref. 302.
The effect of several important parameters 1shape, Re, Ma, Fr, and roughness2on the drag co-
efficient for various objects has been discussed in this section. As stated previously, drag coefficient
information for a very wide range of objects is available in the literature. Some of this information
is given in Figs. 9.28, 9.29, and 9.30 below for a variety of two- and three-dimensional, natural and
man-made objects. Recall that a drag coefficient of unity is equivalent to the drag produced by the
dynamic pressure acting on an area of size A. That is, if Typical
nonstreamlined objects have drag coefficients on this order.
C
D
⫽ 1.d ⫽
1
2
rU
2
AC
D
⫽
1
2
rU
2
A
9.4 Lift 509
Fluids in the News
At 10,240 mpg it doesn’t cost much to “fill ’er up” Typical
gas consumption for a Formula 1 racer, a sports car, and a sedan
is approximately 2 mpg, 15 mpg, and 30 mpg, respectively.
Thus, just how did the winning entry in the 2002 Shell Eco-
Marathon achieve an incredible 10,240 mpg? To be sure, this
vehicle is not as fast as a Formula 1 racer (although the rules re-
quire it to average at least 15 mph) and it can’t carry as large a
load as your family sedan can (the vehicle has barely enough
room for the driver). However, by using a number of clever
engineering design considerations, this amazing fuel efficiency
was obtained. The type (and number) of tires, the appropriate
engine power and weight, the specific chassis design, and the
design of the body shell are all important and interrelated con-
siderations. To reduce drag, the aerodynamic shape of the high-
efficiency vehicle was given special attention through theoreti-
cal considerations and wind tunnel model testing. The result is
an amazing vehicle that can travel a long distance without hear-
ing the usual “fill ’er up.” (See Problem 9.90.)
As is indicated in Section 9.1, any object moving through a fluid will experience a net force
of the fluid on the object. For objects symmetrical perpendicular to the upstream flow, this force
will be in the direction of the free stream—a drag, If the object is not symmetrical 1or if it
does not produce a symmetrical flow field, such as the flow around a rotating sphere2, there
may also be a force normal to the free stream—a lift, Considerable effort has been put forth
to understand the various properties of the generation of lift. Some objects, such as an airfoil,
are designed to generate lift. Other objects are designed to reduce the lift generated. For exam-
ple, the lift on a car tends to reduce the contact force between the wheels and the ground, caus-
ing reduction in traction and cornering ability. It is desirable to reduce this lift.
9.4.1 Surface Pressure Distribution
The lift can be determined from Eq. 9.2 if the distributions of pressure and wall shear stress around
the entire body are known. As is indicated in Section 9.1, such data are usually not known. Typi-
cally, the lift is given in terms of the lift coefficient,
(9.39)C
L
⫽
l
1
2
rU
2
A
l.
d.
9.4 Lift
The lift coefficient
is a dimensionless
form of the lift.
Considerable effort
has gone into re-
ducing the aerody-
namic drag of auto-
mobiles.
JWCL068_ch09_461-533.qxd 9/23/08 11:48 AM Page 509