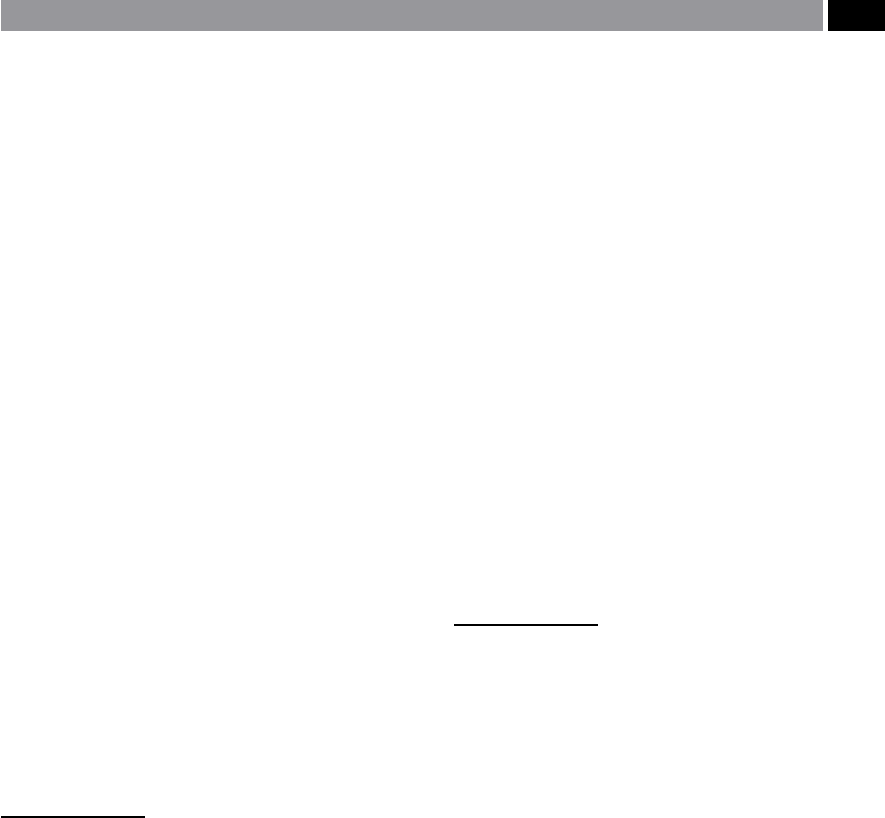
mentally increased to point ‘e’
34
– this being a ‘safe-
limit’ for the optimum machining operation.
7.4 Milled Roundness –
Interpolated Diameters
Circular features such as bosses, circular rebates, etc.,
can be CNC milled by utilising a specic word-ad-
dress ‘
circular interpolation’
35
command. is CNC
function creates precise and accurate circular control
in two slideways simultaneously, while the milling
cutter mills around the workpiece, as depicted in Fig.
158. Here, the milling cutter’s rigidity plays an impor-
tant role in the quality of the nal machined feature,
this being based upon the ‘
rigidity square rule’
36
. e
deected milling cutter illustrated in Fig. 158-right,
having lack-of-rigidity will produce some unwanted
eects on the nal milled part. Cutter deection not
only introduces the potential for chatter vibration,
but if used to mill up to square shoulder, its deection
distorts the component geometry and introduces har-
monic variation to the circular interpolated feature.
So that minimal change takes place in a milled prole,
it is advisable to keep to cutter lengths having short
34 Generally-speaking, it is not advisable to attempt to maintain
both the D
OC
and the total cut width at the stability thresh-
old , because any variation in the: workpiece aecting its cut-
ting stiness ‘K
s
’; speed errors; or perhaps small changes in
the overall dynamic characteristics of the machining system,
could result in crossing the stability limit, creating severe
chatter. For example, in a milling application, the amplitude
of chatter vibration can be limited by a provisional feed per
tooth reduction , until an established and desired speed has
been achieved oering a stable D
OC
.
35 ‘Circular interpolation’ ,
is a block of entered information di-
recting the CNC system to cut, either an arc, or a circle, (e.g.
G02 – in a clockwise, or G03 anti-clockwise direction).
36 ‘Rigidity square rule’ – for milling cutters states: ‘Cutter rigid-
ity decreases by the ‘square’* of the distance from the holder’
(Smith, 1993, et al.).
*
For example, if a cutter ‘stood-out’ from its respective tool-
holder by 50 mm to mill a circular feature (Fig.158 – le), then,
if all other machining conditions remained the same and, then
cutter was replaced by one of 100 mm long (Fig. 158 – right),
it would now be 4 times less rigid, causing serious tool deec-
tion.
stand-o distances, conducive with correct and cur-
rent operational practices.
ere are several distinct problems involved in the
milling high-quality circular interpolated features and,
a slight digression into basic machine tool induced-er-
rors is necessary to clarify the circumstances for the
problems exhibited in Fig. 159. Most of today’s ma-
chine tools have what is termed ‘orthogonally-orien-
tated axes’
37
and in the case of the popular three-axis
vertical machining centre congurations, if the axes
have not been recently calibrated, then considerable
‘error’
38
can be introduced into the nal milled part
features. It has been well-proven that a machine tool
equipped with three orthogonal sideways: ‘X-axis’;
‘Y-axis’ – in the horizontal plane, together with the
‘Z-axis’ – in the vertical plane, can introduce up to 21
kinematic ‘errors’ into the cutting process. e kine-
matics for any machine tool are quite complex, when it
has the ability to provide motion to all its axes simulta-
neously, although these errors are oen small, they are
37 ‘Orthogonally-orientated axes’ , (is briey mentioned in Foot-
note 2) refers to the fact that each axis is positioned at 90° with
respect to each other, oen situated on top of another axis.
For example, on a typical 3-axis vertical machining centre,
the ‘Y-axis’ sits on top of the ‘X-axis’ , but at right-angles to it,
conversely, the ‘Z-axis’ is situated at 90° to these axes – hence
the term ‘orthogonal’.
NB Non-orthogonal machine tools exist, oen having com-
plex ‘kinematics’* between ve and six axes. erefore with
these machine tools, in order to machine (i.e. mill) a straight-
line. all the axes must be in synchronised control to achieve
this linear action.
*Kinematics, comes from the Greek word ‘Kinesis’ , which
means ‘Motion’. It can be dened as: ‘e study of motion with-
out regard for the cause‘ (Lombardi, 2001). In machine tool
terminology, it refers to the translational eects of both lin-
ear and angular motions. It is principally concerned with the
eects of the ‘degrees of freedom’ for a ‘free-body’ in three-di-
mensional space (also see: Footnote 47, in Chapter 3).
38 ‘Error’ is now not considered as an appropriate metrological
term for any form of calibration, the recommended term to-
day, is: ‘uncertainty’*.
*‘Uncertainty’ , has been simply dened as: ‘e doubt that
exists about the result of any measurement’ (Bell/NPL, 1999).
is is why today, uncertainty in measurement is a combina-
tion of many factors, some physical, while others are induced.
Hence, another term, along with all of these uncertainty fac-
tors has been coined, which is its ‘Uncertainty budget’ – this
being a simple mathematical calculation, based upon a sum-
mary of these uncertainty calculations.
Machinability and Surface Integrity 301