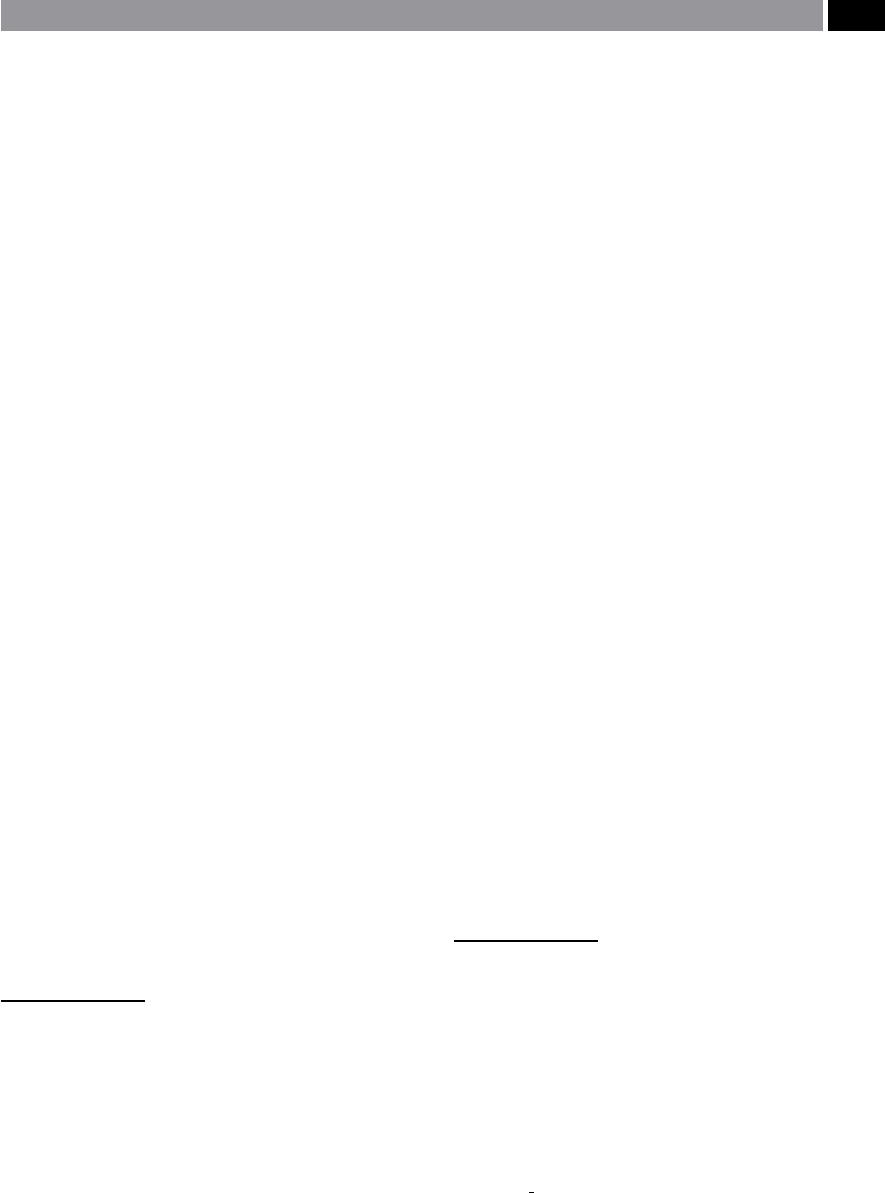
1. Roughness – comprising of surface irregularities
occurring due to the mechanism of the machining
production process and its associated cutting insert
geometry,
2. Waviness – that surface texture element upon
which roughness is superimposed, created by fac-
tors such as the: machine tool, or workpiece deec-
tions, vibrations and chatter, material strain and
other extraneous eects,
3. Prole – represents the overall shape of the ma-
chined surface – ignoring any roughness and wavi-
ness variations present, being the result of perhaps
the long-frequency machine tool slideway errors.
e above surface topography distinctions tend to be
qualitative – not expressible as a number – yet have
considerable practical importance, being an estab-
lished procedure that is functionally sound. e com-
bination of roughness and waviness surface texture
components, plus the surface’s associated ‘Lay’
43
are
shown in Fig. 160a. e ‘Prole’ is not depicted, as it
is a long-frequency component and at best, only its
partial aect would be present here, on this diagram.
e ‘Lay’ of a surface tends to be either: anisotropic,
or isotropic
44
in nature on a machined surface topog-
raphy. When attempting to characterise the potential
functional performance of a surface, if an anisotropic
‘lay-condition’ occurs, then its presence becomes of
vital importance. If the surface texture instrument’s
stylus direction of the trace’s motion over the assessed
topography is not taken into account, then totally mis-
representative readings result for an anisotropic sur-
face condition occur – as depicted in Fig. 160b. is
is not the case for an isotropic surface topography, as
relatively uniform set of results will be present, regard-
less of the stylus trace direction across the surface (i.e.
43 ‘Lay’ , can simply be dened as: e direction of the dominant
pattern’ (Dagnall, 1998).
44 ‘Anisotropic, or isotropic surfaces, either condition can be in-
dividually represented on all machined surfaces. Anisotropy,
refers to a surface topography having directional properties,
that is a dened ‘Lay’ , being represented by machined feed-
marks (e.g. turned, shaped, planed surfaces, etc.). Conversely,
an isotropic surface is devoid of a predominant ‘Lay’ direc-
tion, invariably having identical surface topography charac-
teristics in all directions (e.g. shot-peening/-blasting and, to a
lesser extent a multi-directional surface-milling, or a radially-
ground surface, etc.).
see Fig. 161a – for an indication of the various clas-
sications for ‘Lay’).
Returning once more to Fig. 160b, as the stylus
trace obliquity changes from trace ‘A’ , inclining to-
ward trace ‘E’ , the surface topography when at ‘E’ has
now become at, giving a totally false impression of
the true nature of the actual surface condition. If this
machined workpiece was to be used in a critical and
highly-stressed in-service environment, then the user
would have a false sense of the component’s potential
fatigue
45
characteristics, potentially resulting in ei-
ther premature failure, or at worst, catastrophic fail-
ure conditions. In Fig. 162, the numerical data (ISO
1302:2001), has been developed to establish and de-
ne relative roughness grades for typical production
processes. However, some caution should be taken
when utilising these values for control of the surface
condition, because they can misrepresent the actual
state of the surface topography, being based solely on a
derived numerical value for height. What is more, the
‘N-number’ has been used to ascertain the arithmetic
roughness ‘Ra’ value – with more being mentioned on
this and other parameters shortly. e actual ‘N-value’
being just one number to cover a spread of potential
‘Ra’ values for that production process. Neverthe-
less, this single numerical value has its merit, in that
it ‘globally-denes’ a roughness value (i.e.‘Ra’) and
its accompanying ‘N-roughness grade’ , which can be
used by a designer to specify in particular a desired
surface condition, this being correlated to a specic
production process. e spread of the roughness for a
specic production process has been established from
experimental data over the years – covering the maxi-
mum expected ‘variance’
46
– which can be modied
45 ‘Fatigue’ , can be dened as: ‘e process of repeated load, or
strain application to a specimen, or component’ (Schaer, et
al., 1999). Hence, any engineering component subjected to
repeated loading over a prescribed time-base, will normally
undergo either partial, or complete fatigue.
46 ‘Variance’ , is a statistical term this being based upon the
standard deviation, which is normally denoted by the Greek
symbol ‘σ’. us, variance can be dened as: ‘e mean of the
squares of the standard deviation’ (Bajpai, et al., 1979).
us, σ = √Variance, or more specically for production op-
erations:
�
s =
�
�n − ċ
n
�
j=
(x
j
−
¯
x)
*s = the standard deviation of a sample from a production
batch run.
Machinability and Surface Integrity 307