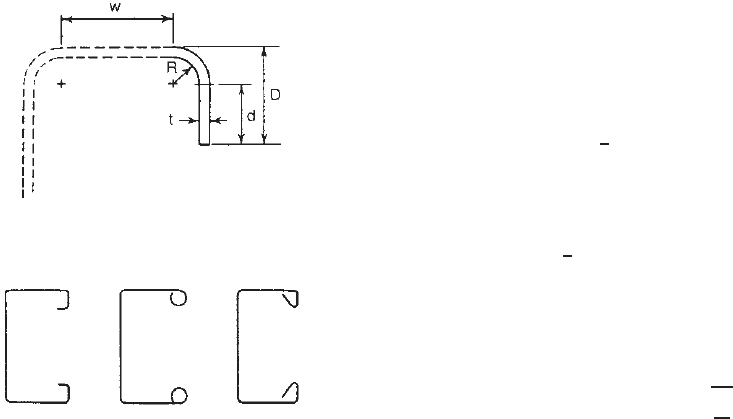
82 3 STRENGTH OF THIN ELEMENTS AND DESIGN CRITERIA
the effective section modulus S
e
in Section 4.2.2, the extreme
tension fiber in Figs. 3.44b and 3.45b shall be taken as the
edge of the effective section closer to the unsupported edge.
(b) Serviceability Determination. The effective width b
d
used
in determining serviceability shall be calculated in accordance
with specification Section B3.2(a), except that f
d1
and f
d2
are
substituted for f
1
and f
2
as shown in Figs. 3.43, 3.44, and 3.45,
respectively, based on the gross section at the load for which
serviceability is determined.
The applications of the above design provisions are
illustrated in Examples 3.7 and 4.2.
3.5.3 Uniformly Compressed Elements with Stiffeners
3.5.3.1 Uniformly Compressed E lements with a Simple
Lip Edge Stiffener An edge stiffener is used to provide
a c ontinuous support along a longitudinal edge of the
compression flange to improve the buckling s tress. Even
though in most cases the edge stiffener takes the form
of a simple lip (Fig. 3.46), other types of stiffeners, as
shown in Fig. 3.47, can also be used for cold-formed steel
members.
3.78,3.173
In order to provide the necessary support for the compres-
sion element, the edge stiffener must possess sufficient
rigidity. Otherwise it may buckle or displace perpendicular
to the plane of the element to be stiffened.
Both theoretical and experimental investigations on the
local stability of flanges stiffened by lips and bulbs have
been conducted in the past.
3.75–3.82,3.217–3.220
The design
requirements included in the 1986 and 1996 editions of the
AISI Specification for uniformly compressed elements with
Figure 3.46 Edge stiffener.
Figure 3.47 Edge stiffeners other than simple lip.
3.78
an edge stiffener are based on the analytical and exper-
imental investigations on adequately stiffened elements,
partially stiffened elements, and unstiffened elements
conducted by Desmond, Pekoz, and Winter
3.75,3.76
with
additional studies carried out by Pekoz and Cohen.
3.17
Those design provisions were developed on the basis of
the critical buckling criterion and the ultimate-strength
criterion. In this design approach, the design requirements
recognize that the needed stiffener rigidity depends on
the width-to-thickness ratio of the plate element being
stiffened. The interaction between the plate element and the
edge stiffener is compensated for in the design equations
for the plate buckling coefficient, the reduced effective
width of a simple lip edge stiffener, and the reduced area
of other stiffened shapes. Because a discontinuity exists
in the 1996 AISI design provisions, in 2001, Dinovitzer’s
expressions were adopted in the first edition of the North
American Specification for determining the constant “n”
to eliminate the discontinuity.
3.221
In 2007, the design provisions of the first edition of
the North American Specification were revised to limit the
design equations for applying only to simple lip edge stiff-
eners due to the fact that previous equations for complex
lip stiffeners were found to be unconservative, in compar-
ison with the nonlinear finite-element analysis conducted
by Schafer, Sarawit, and Pekoz.
3.222
According to Section B4 of the 2007 edition of the
North American Specification, the effective width of the
uniformly compressed elements with a simple lip edge
stiffener can be calculated by the following equations.
For other stiffener shapes, the design of member strength
may be handled by the direct-strength method provided in
Appendix 1 of the North American Specification:
(a) Strength Determination. For w/t ≤ 0.328S
I
a
= 0 (no edge stiffener needed) (3.74)
b = w (3.75)
b
1
= b
2
=
1
2
w (see Figure 3.48) (3.76)
d
s
= d
s
For w/t > 0.328 S
b
1
=
1
2
(b)(R
I
) (see Figure3.48) (3.77)
b
2
= b − b
1
(see Figure 3.48) (3.78)
d
s
= d
s
(R
I
) (3.79)
where
S = 1.28
E
f
(3.80)