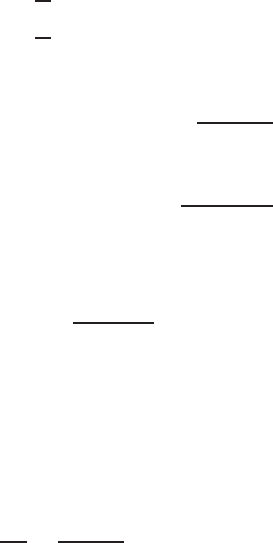
BENDING STRENGTH AND DEFLECTION 113
iii. To tal I
x
and S
x
.
2I
5
= 2 ×
1
12
× (4.6624)
3
= 16.8918
2I
1
= 2 ×
1
12
× (0.5812)
3
= 0.0327
2(I
2
+ I
4
+ I
6
) = 0.0020
(Ly
2
) = 258.0345
274.9610
−
L
y
cg
2
=−26.7618(2.428)
2
=−157.7657
I
x
= 117.1953 in.
3
I
x
= I
x
t = 117.1953(0.075) = 8.7896 in.
4
S
x
=
8.7896
5 − 2.428
= 3.4174 in.
3
2. Nominal and Allowable Moments. The nominal
moment for section strength is
M
n
= S
e
F
y
= S
x
F
y
= (3.4174)(33) = 112.774 in.-kips
Theallowablemomentis
M
a
=
M
n
b
=
112.774
1.67
= 67.53 in.-kips
B. LRFD Method.
The nominal moment for the LRFD method is the same
as that computed for the ASD method. From the above
calculations, the nominal moment about the x axis of the
section is
M
n
= 112.774 in.-kips
Based on Section 4.2.1 in this volume or C3.1.1 of the
North American specification, the design moment for the
given section having a uniformly compressed flange with
one intermediate stiffener (φ
b
= 0.95) is
φ
b
M
n
= 0.95(112.774) = 107.14 in.-kips
4.2.2.2 Effects of Cold Work on Bending Strength The
bending strength of cold-formed steel sections discussed
above was based on the mechanical properties of the
virgin material. The effects of cold work were completely
neglected.
When the effects of cold work are utilized in the deter-
mination of bending strength, the computation can be
performed by one of the following two design approaches.
1. Consider the increase in yield stress at corners due to
cold work and neglect the effects of cold work in all
flat portions of the section. As discussed in Chapter
2, the increase in yield stress can be found either by
the use of Eq. (2.11) or by tests.
2. Consider the effects of cold work for corners and all
flat elements. Equation (2.14) can be used to compute
the average yield stress of the entire section.
In either design approach, the following procedures may be
used
2.17
:
1. Subdivide the section into a number of elements.
Assume a position of the neutral axis and the strain in
the top fiber. Compute the strains in various elements
based on the assumed neutral axis and the top fiber
strain.
2. Determine the stresses from the stress–strain rela-
tionship of the material in various elements for the
computed strains.
3. Locate the neutral axis by iteration until
σA= 0
is satisfied. Then the bending moment can be approx-
imated by
M =
σy A
where σ = stress
A = area for element
y = distance between center of gravity of
each element and neutral axis
Results of the study by Winter and U ribe indicate
that for the steels commonly used in thin-walled cold-
formed steel construction, considering the effects of
cold work only in the corners of the formed sections,
the moment capacities can be increased by 4–22%
compared with those obtained when neglecting cold
work.
2.17
If the effects of cold work are considered in both the
flats and the corners, the increase in bending strength
ranges from 17 to 41% above the virgin value.
It can be seen that a substantial advantage can be
obtained by using the increase in strength of the mate-
rial. Figure 4.14, reproduced from Ref. 2.17, shows a
comparison of the ultimate moments computed for
three different conditions. It should be noted that the
effects of cold work as shown in Fig. 4.14 may not
be directly applied to other configurations because the
relative influence of corners or flats on the increase
in bending strength depends mainly on the config-
uration of the section and the spread between the
tensile strength and yield stress of the virgin mate-
rial. Attention should be given to the limitations
of Section A7.2 of the North American Specifica-
tion when the effects of cold work are used in
design.