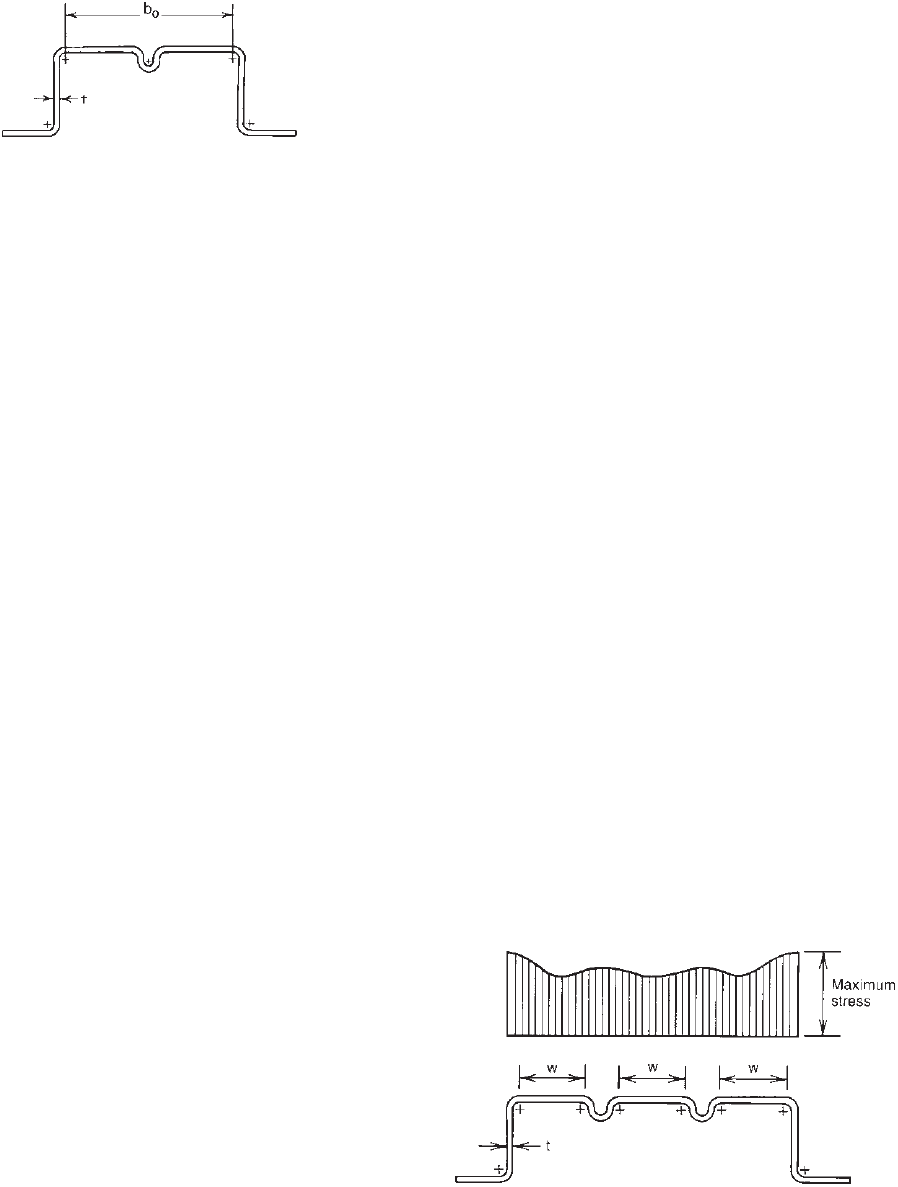
STRUCTURAL BEHAVIOR OF COMPRESSION ELEMENTS AND DESIGN CRITERIA 87
Figure 3.52 Section with single i ntermediate stiffener.
stiffener has been studied by H
¨
oglund,
3.72
K
¨
onig,
3.73
K
¨
onig
and Thomasson,
3.74
Desmond, Pekoz, and Winter,
3.75–3.77
Pekoz,
3.17
and Yang and Schafer.
3.223
In the study of Bernard, Bridge, and Hancock,
3.171,3.172
both local buckling and distortional buckling in the
compression flange of profiled steel decks were discussed
by the researchers.
As far as the design provisions are concerned, the 1980
and earlier editions of the AISI Specification included the
requirements for the minimum moment of inertia of the
intermediate stiffener for multiple-stiffened compression
elements. When the size of the actual intermediate stiffener
did not satisfy the required minimum moment of inertia, the
load-carrying capacity of the member had to be determined
either on the basis of a flat element disregarding the
intermediate stiffener or through tests. For some cases, this
approach could be unduly conservative.
3.17
The AISI design provisions were revised in 1986 on the
basis of the research findings reported in Refs. 3.75–3.77.
In that method, the buckling coefficient k for determining
the effective width of subelements and the reduced area of
the stiffener was calculated by using the ratio I
s
/I
a
, where
I
s
is the actual stiffener moment of inertia and I
a
is the
adequate moment of inertia of the stiffener determined from
the applicable equations. The same design requirements
were retained in the 1996 edition of the AISI Specification.
Because a discontinuity could occur in those equations,
the design provisions were revised in the 2001 edition of
the North American Specification by adopting Dinovitzer’s
expressions to eliminate the discontinuity.
3.221
In the 2007 edition of the North American Specification,
the design of uniformly compressed stiffened elements with
a single intermediate stiffener was merged with the stiffened
elements having multiple intermediate stiffeners. Section
3.5.3.2.2 provides the AISI design requirements for this
particular case by using the number of stiffeners equal to
unity (i.e., n = 1) in Eqs. (3.92) and (3.93). See Example
4.4 for the application of these equations.
3.5.3.2.2 Uniformly Compressed Elements with
Multiple Intermediate Stiffeners In beam sections, the
normal stresses in the flanges result from shear stresses
between the web and flange. The web generates the normal
stresses by means of the shear stress which transfers to the
flange. The more remote portions of the flange obtain their
normal stress through shear from those close to the web.
For this reason there is a difference between webs and
intermediate stiffeners. The latter is not a shear-resisting
element and does not generate normal stresses through
shear. Any normal stress in the intermediate stiffener
must be transferred to it from the web or webs through
the flange portions. As long as the subelement between
web and stiffener is flat or is only very slightly buckled,
this stress transfer proceeds in an unaffected manner.
In this case the stress in the stiffener equals that at
the web, and the subelement is as effective as a regular
single-stiffened element with the same w/t ratio. H owever,
for subelements having larger w/t ratios, the slight waves
of the subelement interfere with complete shear transfer
and create a “shear lag” problem which results in a stress
distribution as shown in Fig. 3.53.
As far as the design is concerned, the AISI design
provisions for uniformly compressed elements with one
intermediate stiffener were revised in 1986 on the basis
of the 1981 Cornell research.
3.75–3.77
Because this Cornell
project did not cover the multiple-stiffened elements with
more than one intermediate stiffener a nd the edge-stiffened
elements with intermediate stiffeners, the 1986 and 1996
editions of the AISI Specification a dopted the same design
provisions as the 1980 edition of the AISI Specification for
these cases.
In the 1996 edition of the AISI Specification, the
design requirements for uniformly compressed elements
with multiple intermediate stiffeners and edge-stiffened
elements with intermediate stiffeners included (a) the
minimum moment of inertia of the full stiffener about its
own centroidal axis parallel to the element to be stiffened,
(b) the number of stiffeners considered to be effective,
(c) the “equivalent element” of the entire multiple-stiffened
element for closely spaced stiffeners with an “equivalent
thickness,” (d) the reduced effective width of subelement
Figure 3.53 Stress distribution in compression flange with
intermediate stiffeners.
1.161