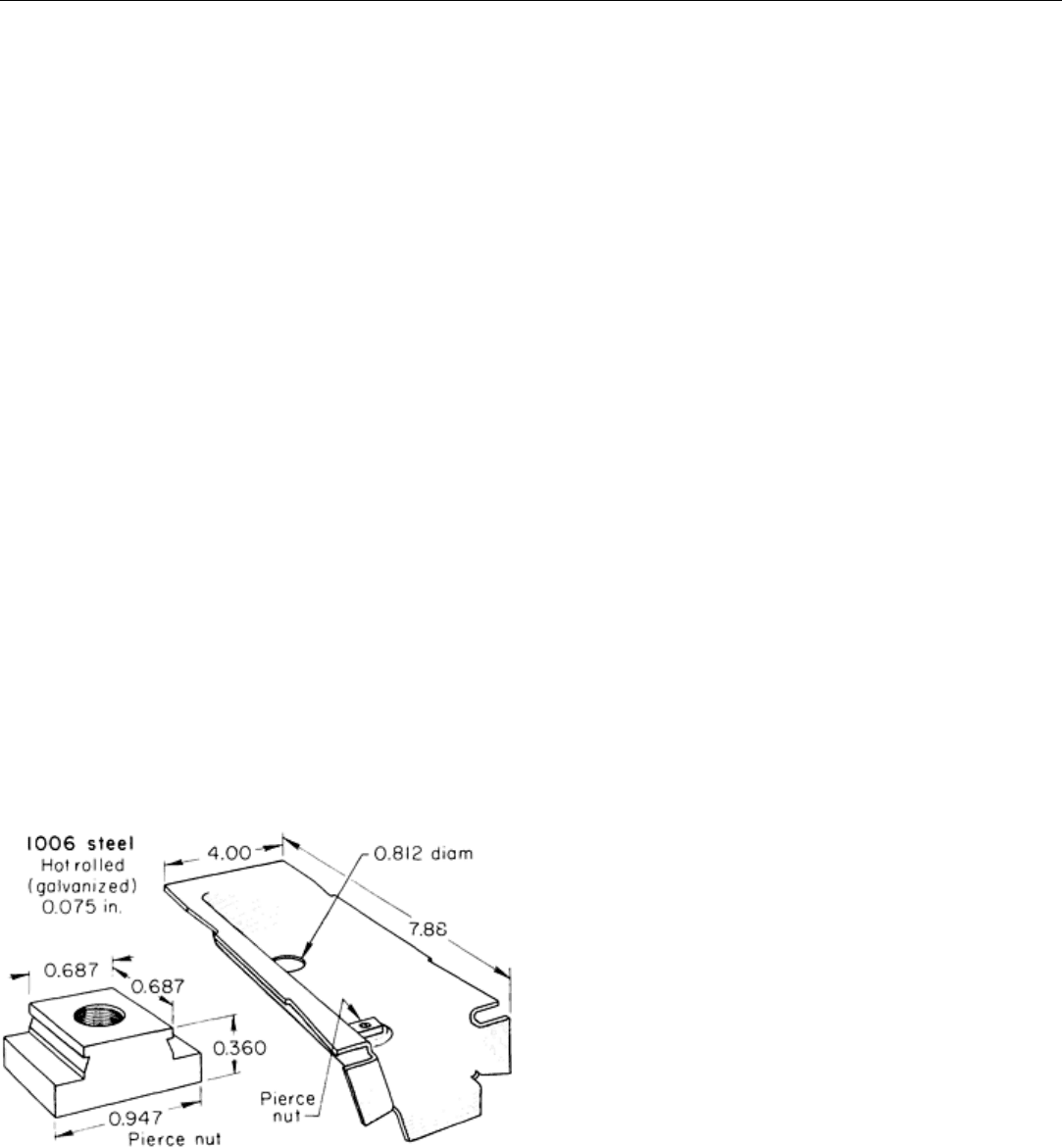
Piercing of Low-Carbon Steel
Special Piercing Techniques
Piercing operations that require special tooling and techniques include the piercing and forming of flanged holes, piercing
with a fastener and with a pointed punch, and tube piercing.
Flanged holes (sometimes called extruded, countersunk, dimpled, or burred holes) are generally used for assembly
purposes, such as providing more thread length for a tapped hole, greater bearing surface, or a recess for a flathead screw
or rivet. The flanged hole can be produced by forcing a punch of the desired hole diameter through a smaller prepierced
hole or by using a shouldered or pointed punch that both pierces the hole and flanges it.
The depth of flange that is formed depends on the elongation of the metal, and the flange is thinnest at its outer edge. A
deeper flange can be made by extruding metal into the flange. Such flanging is done by first piercing a smaller lead hole
and then using a punch that extrudes metal around the hole into the die clearance to produce a flange and simultaneously
coins or forms a slight chamfer (depressed cone) or other shape of recess into the hole (see also the article "Press Bending
of Low-Carbon Steel" in this Volume). This kind of extruded flange has uniform wall thickness. Such extrusion causes
more metal flow and greater work hardening than ordinary piercing of flanged holes.
Piercing with a fastener (self-piercing) is primarily used as an assembly technique. A rivet, for example, can be used
as a punch to pierce a hole through the material that it will join. The following example describes an application in which
a square nut with a sharp face served as a piercing tool and then became part of an assembly.
Example 10: Automatic Assembly of Self-Piercing Nut into a Bracket.
A square nut was automatically assembled into a body-bolt bracket, as shown in Fig. 15. The nut served as the piercing
punch to make a 17.4 mm (0.687 in.) square hole in the embossed portion of the bracket. The bracket was made of
galvanized, hot-rolled 1006 steel, 1.9 mm (0.075 in.) thick. After being pierced, the metal sprang back into two grooves in
the nut, locking the nut into the pierced square hole. The nut was fed from a special installing head that was loaded from a
rotary hopper.
Two assemblies were completed (pierced and installed) at
each stroke of a 640 kN (72 tonf) open-back inclinable
press running at 45 strokes per minute. Maximum daily
production was 12,000 assemblies. The bracket was fed by
a gravity-slide feed at the front of the press and was
unloaded at the rear with the help of an air blast.
The 20.6 mm (0.812 in.) diam hole was pierced at the
same time the nut was inserted. Commercial punches and
die buttons were used.
A standby unit for piercing a square hole was available in
case a supply of the square nuts was not on hand when the
part was scheduled to run. The nuts were later inserted and
clinched using pneumatic equipment.
Holes made with a pointed punch, such as a cone-
point, nail-point, or bullet-nose (ogive) punch, have rough
or torn flanges. Such a hole is satisfactory for holding a
sheet metal screw, acting as a spacer, or providing a rough
surface.
Tube piercing and slotting are done in dies when production lots are large enough to pay for special tooling. Simple
dies, as well as more complex tooling such as cam dies, are designed to hold, locate, and pierce tubes, drawn cups, and
other round parts.
Fig. 15
Bracket with a square nut that pierced a hole
for itself. Dimensions given in inches