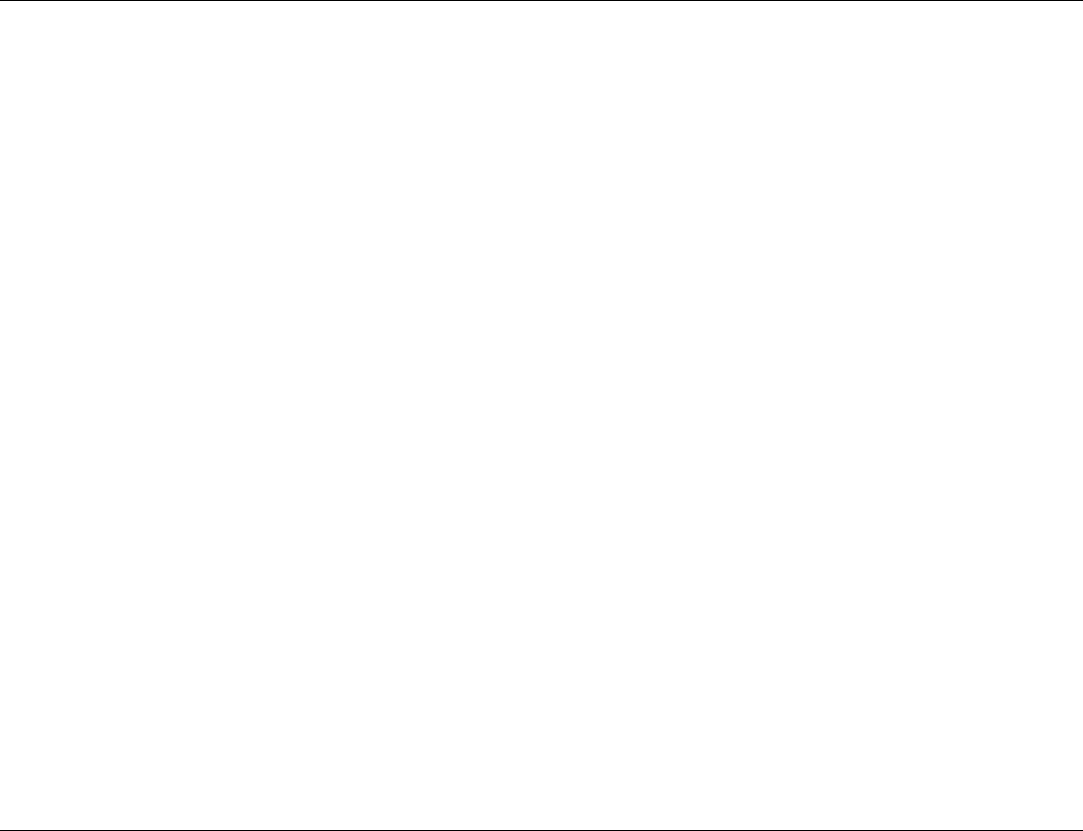
To a large extent, applications also follow the above classification (Table 1). Each group has certain distinct
characteristics that affect punchability. In addition, differences in composition and hardness within any specific group
cause considerable variation in punchability (see the section "Effect of Work Metal Composition and Condition" in this
article).
Blanking and Piercing of Electrical Steel Sheet
Presses
A general-purpose punch press in good mechanical condition is acceptable for stamping laminations, but large-volume
production of laminations by progressive-die methods requires the use of high-productivity presses (see the article
"Presses and Auxiliary Equipment for Forming of Sheet Metal" in this Volume). Most high-productivity presses have
heavy bed and crown members to minimize deflection and vibration. Bed deflection for lamination presses should be no
more than 0.006 mm/mm (0.006 in./in.) of bed length (measured left-to-right between uprights), with a load equal to the
rated capacity of the machine distributed over two-thirds of the bed area between tie rod centers. Deflection of the slide
should not exceed 0.006 mm/mm (0.006 in./in.) of the length between the pitman centers, with rated load evenly
distributed between those centers. Bending deflection and shear deflection are both considered in these standards. Double-
crank presses with two or four points of suspension are preferred for progressive-die applications because of their better
resistance to off-center die loads. Parallelism of the bed and slide should be 0.012 mm/mm (0.012 in./in.) of bed
dimensions, both left-to-right and front-to-back.
Presses designed for producing laminations have heavy connections, large diameters of the mainshaft and connection
bearings, close gib clearances, and thick bolsters. Because of the close gib fits (needed for accurate vertical motion),
recirculating oil systems must be used to provide forced-feed lubrication of bearings and slides.
The fact that a die was built with uniform punch-to-die clearance at all cutting edges does not necessarily mean that the
clearance is uniform at the instant the punch begins to enter the work metal. The act of applying the load to the work
metal can cause lateral deflections in the die and press, which can change the clearances. To minimize these undesirable
deflections, the mechanical condition of the press and die must be maintained at a high level. The total force capacity
exerted at each stroke must be in proper relation to the force capacity of the press and to the type of press frame (some
types of press frames will deflect laterally more than others). Close-fitting gibs and bearings are essential in minimizing
lateral deflection. The die should be built with large guideposts and close-fitting bushings.
A preventive maintenance program must be established to ensure that all presses are kept in top condition. Special
attention should be given to bearing clearances, the condition of the counterbalance springs or cylinders, and the
parallelism of the slide.
Blanking and Piercing of Electrical Steel Sheet
Auxiliary Equipment
When producing motor laminations in individual dies for each operation with upright or inclined presses, blanks can be
loaded and unloaded manually. However, when individual dies are used for the simultaneous production of stator and
rotor laminations, feeding and stacking equipment is necessary for optimal efficiency. The use of an inclined press is
preferred because gravity assists in loading the die and removing the laminations. When progressive dies are used,
automatic feeding and scrap-cutting equipment is required.
Stock reels, cradles, and straighteners are required when coil stock is used. Several types and sizes are available
(see the article "Presses and Auxiliary Equipment for Forming of Sheet Metal" in this Volume).
Feed Mechanisms. In progressive-die operations, the common types of feed mechanisms, for example single-roll or
double-roll, hitch, grip, and slide, are used to feed strip or coil. Cam feed, which has a fixed feed length, is widely used
for large-volume production. This method is accurate at high speeds because it eliminates the slippage that usually occurs
in the overriding clutch-and-brake mechanisms of roll feeds.
Magazine feeds have a mechanism that ejects the blank from the bottom of a stack into the die or onto a magnetic belt or
a chain feed. In inclined presses, the blank may slide by gravity into the die nest after leaving the magazine.