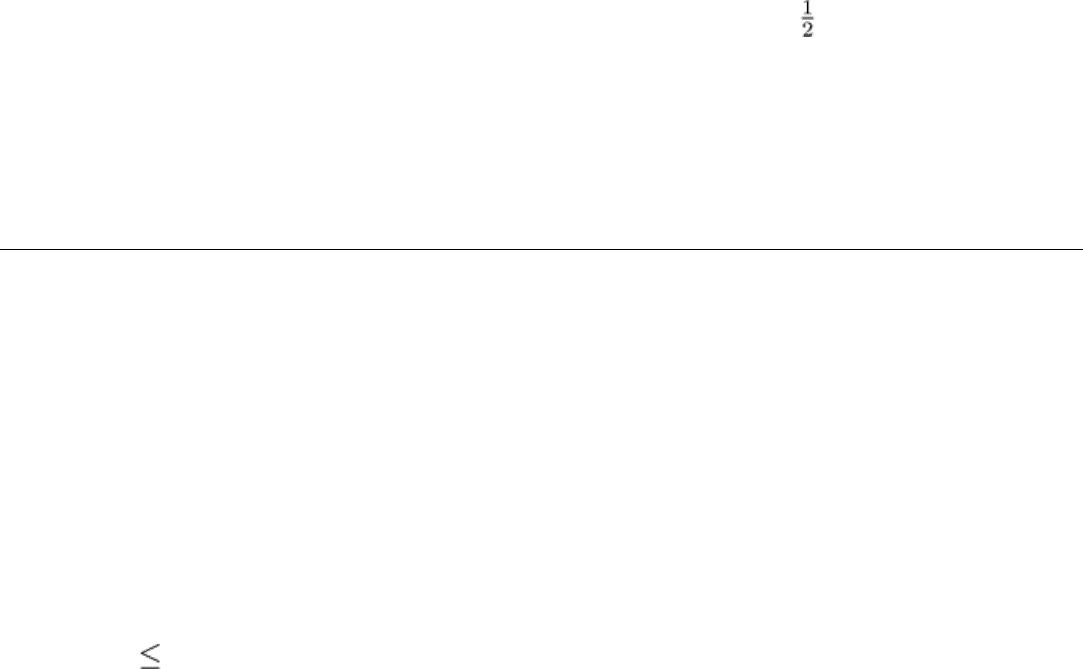
Almost any hardened tool steel is satisfactory as die material for making a small quantity of laminations. However, for
production blanking and piercing, either a high-carbon high-chromium cold-work tool steel, such as AISI D2, or carbide
must be used to resist the abrasiveness of electrical steels.
The shape or size of the lamination seldom affects the choice of die material. Dies ranging from the smallest to the largest
and from the simplest to the most complex have been made from both high-carbon high-chromium tool steel and carbide.
In addition, both die materials have been used to blank and pierce all compositions and thicknesses of electrical sheet. The
composition and thickness of the stock rarely affect the choice between carbide and tool steel.
Production Quantity. If the dies are of the same design and construction, the total quantity of parts to be produced is
the major factor in choosing die material. If the run is so short that it can be made with tool steel dies without sharpening,
tool steel is more economical. However, for longer runs, carbide dies have 10 to 20 times as much life per grind as tool
steel dies.
Uniform quality of cut edges and minimum burr height will be retained over a much longer run by carbide dies than
by tool steel dies. In some cases, the edge condition of the lamination is not critical. However, when automatic stacking
and core assembly equipment is used after blanking and piercing, burr height is important. Excessive burr height can
cause short circuiting of the laminations in the core.
Cost. Depending on size and design, a die with carbide cutting edges will cost at least 1 times as much as a steel die.
However, in terms of cost per piece, carbide dies may be more economical. Press downtime and die maintenance affect
cost per piece; carbide dies can run about ten times as long per sharpening as tool steel dies.
Press condition is important in the operation of blanking and piercing dies. To achieve the maximum potential usage
of carbide dies, press condition must be maintained at a high level. Although tool steel punches and dies can chip and
shear because of misalignment, carbide punches and dies are more likely to break. Therefore, the presses used for tool
steel dies can be in less than top level condition and continue to produce quality laminations.
Blanking and Piercing of Electrical Steel Sheet
Effect of Stock Thickness
Electrical sheet that is to be blanked and pierced usually ranges in thickness from 29 to 24 gage (0.343 to 0.607 mm, or
0.0135 to 0.0239 in.). Thinner or thicker stock is used for special applications. The blanking and piercing of extremely
thin electrical sheet requires close control of equipment and technique. The processing of thick sheet (>1.27 mm, or 0.050
in.) can also cause difficulty, although the force-capacity rating of the press is the major factor that determines the
maximum thickness of sheet that can be blanked and pierced.
Punch-to-die clearance for electrical sheet generally ranges from 3 to 7.5% of stock thickness per side, with clearances as
large as 20% reported for grain-oriented stock. These values are similar to those used for low-carbon steel, but the stock
thicknesses are thinner than those commonly used for the low-carbon steels. This results in close die clearance and
requires good diemaking practice and accurate press equipment.
Thin Sheet ( 0.254 mm, or 0.010 in.). Under carefully controlled conditions, laminations can be blanked and
pierced from sheet as thin as 0.051 mm (0.002 in.), but the press must be in top condition. Further, the feeding mechanism
must be capable of feeding within ±0.076 mm (±0.003 in.) total error per stroke at a feed rate of 23 m/min (900 ft/min).
Punches and dies of hardened tool steel, such as D2, or carbide are satisfactory, although carbide dies and punches will
have at least ten times the life of their tool steel counterparts. The punches must be rigidly supported and guided. The
entire tool must be made rugged and accurate enough to maintain alignment. To avoid shearing the punch and die during
press setup, it is important that the die be handled carefully to prevent the possibility of some of the components moving
out of alignment. The press bed, the bottom of the die shoe, the face of the press slide, and the top of the punch holder
must be clean and free of any irregularities that would cause a deviation from parallelism.
The punch and the die as a unit should be aligned square with the centerline of the press. The press slide should then be
brought down slowly to meet with the top of the punch holder, and the punch holder should be fastened to the face of the