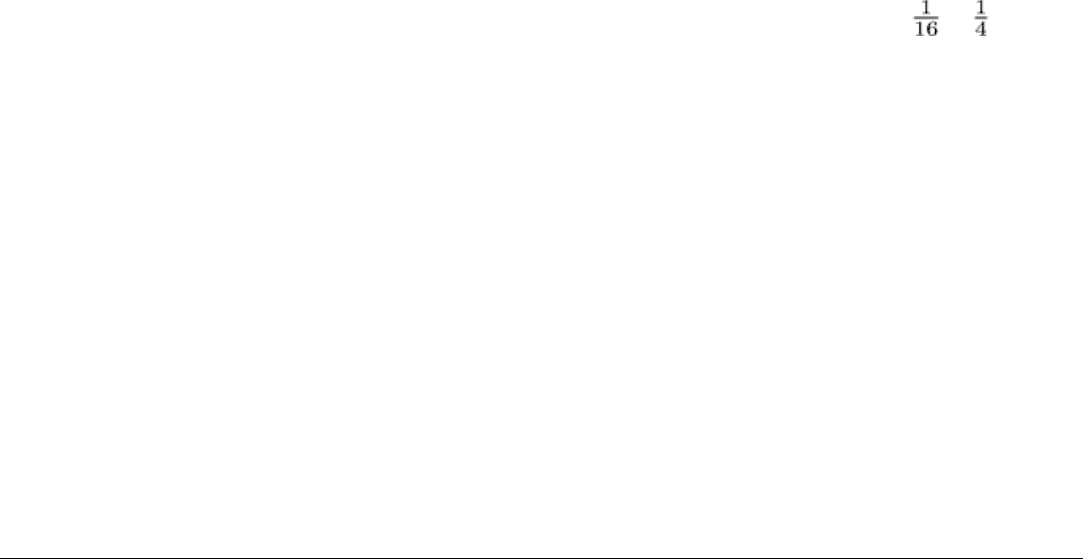
inherent at the bottom of the stroke. These presses are rated to deliver full capacity at 1.6 to 6.4 MM ( to in.) above
the bottom of the stroke. The very quick increase in force as the slide nears the bottom of the stroke is the reason its
usefulness is limited to operations performed at the bottom of the stroke. Knuckle lever presses usually have capacities of
1.4 to 8.9 MN (150 to 1000 tonf).
Rocker arm drives apply crank or eccentric motion to a rocker arm that is connected to the press slide (Fig. 6). In this
mechanism, the linkage is driven by an eccentric gear and a connecting rod. The rocker arm drive is a variation of the
knuckle lever drive. However, a press with rocker arm drive is not limited to coining operations; it can also be used for
drawing or forming operations.
The rocker arm drive is used mainly in large-bed underdrive presses. The linkage operates from below the press bed and
pulls the slide into the work by a link running up through each of the press columns. In most rocker arm drives, the rocker
pin and the connecting eccentric pin do not stop in a vertical plane; thus, the load on the eccentric shaft is relieved at the
point of maximum load on the slide, and sticking at the bottom of the stroke is prevented. In addition, a high press
capacity is obtained because of the mechanical advantage.
Toggle mechanisms are the most widely used means of providing the second action in double-action mechanical
presses. The toggles operate an outer slide, which clamps the blank against the die, while the punch, operated by the inner
slide directly from the crankshaft, performs the draw operation. Principal components of a toggle mechanism are shown
in Fig. 6.
Presses and Auxiliary Equipment for Forming of Sheet Metal
Number of Slides
Mechanical (and hydraulic) presses have one, two, or three slides and are referred to as single-, double-, or triple-action
presses. Each slide can be moved in a separately controlled motion.
A single-action press has one reciprocating slide (tool carrier) acting against a fixed bed. Presses of this type, which
are the most widely used, can be employed for many different metal-stamping operations, including blanking, embossing,
coining, and drawing. Depending on the depth of draw, single-action presses often require the use of a die cushion for
blankholding. In such applications, a blankholder ring is depressed by the slide (through pins) against the die cushion,
usually mounted in the bed of the press (see the section "Die Cushions" in this article).
A double-action press has two slides moving in the same direction against a fixed bed. These slides are generally
referred to as the outer (blankholder) slide and the inner (draw) slide. The blankholder slide is a hollow rectangle, while
the inner slide is a solid rectangle that reciprocates within the blankholder.
Double-action presses are more suitable for drawing operations, especially deep drawing, than are single-action presses.
In single-action presses, force is required to depress the cushion. In double-action presses, the blankholder slide has a
shorter stroke and dwells at the bottom of its stroke before the punch mounted on the inner slide contacts the work. As a
result, practically the entire capacity of the press is available for drawing. Another advantage is that the four corners of
the blankholder are individually adjustable so that nonuniform forces can be exerted on the work when required. A
double-action press equipped with a die having an open bottom permits pushing the stamping through the die to perform
other operations, such as ironing, after drawing.
Deep-drawing operations and irregularly shaped stampings generally require the use of a double-action press. Most
operations performed on double-action presses require a cushion either for lift-out or for reverse drawing of the stamping.
A triple-action press has three moving slides: two slides moving in the same direction as in a double-action press and
a third, or lower, slide moving upward through the fixed bed in a direction opposite to the blankholder and inner slides.
This action permits reverse drawing, forming, or beading operations against the inner slide while both upper actions are
dwelling.
Cycle time for a triple-action press is necessarily longer than it is for a double-action press because of the time required
for the third action. Because most drawn stampings require subsequent restriking and/or trimming operations, which are
done in faster, single-action presses, most stamping manufacturers consider the triple-action press too slow.