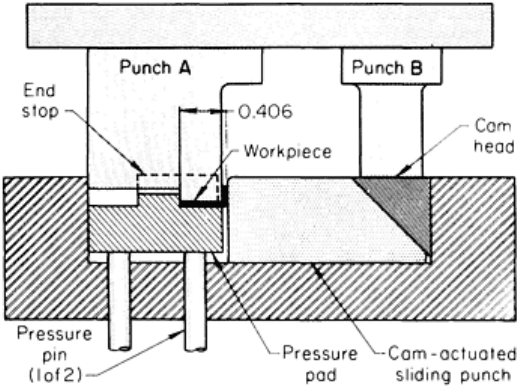
Fig. 7 Rotary-bending die used for 90° twisting of strip metal. Die is shown in close
d position; inner cylinder
has rotated to give workpiece a 90° twist. The auxiliary cam prevents rotation of the inner cylinder until it is
free of workpiece.
As shown in Fig. 7, a 90° twist is given to strip metal to make a connecting link. The punch is made in two major parts: a
hollow cylinder that is solidly mounted to the ram, and inside it a solid cylinder that is free to rotate. The inner cylinder
has a 90° helical cam groove in its cylindrical surface that engages a hardened pin in the outer cylinder.
When the ram descends, a slot in the face of the inner cylinder engages the end of the workpiece. After the inner cylinder
bottoms, as the ram continues to move down, the spring compresses, letting the outer cylinder move down over the inner
cylinder. The action of the pin in the groove makes the inner cylinder rotate, giving the workpiece a 90° twist.
An auxiliary cam keeps the inner cylinder from rotating back in the return stroke, until it has cleared the workpiece. Near
the top of the stroke, the auxiliary cam is released by a stop, allowing the inner cylinder to return to its starting position.
Cam-Actuated Flanging Dies. Horizontal motion is often needed to form, or partially form, a flange on a workpiece.
One of the most commonly used methods of producing this motion at right angles to the motion of the main press ram is
with an inclined surface, or cam, in the die mechanism.
As shown in Fig. 8, a blankholder contacts the work first and holds it in position. Resiliency, either in the form of
pressure pins leading to a die cushion or in the form of a spring, allows the ram to continue to descend. A cam actuates
the sliding punch, which either forms or completes the forming of the flange and is then retracted. The blank is placed on
the pressure pad, where it is held by punch A and wiped past the cam-actuated sliding punch to form the flange. Near the
bottom of the stroke, punch B contacts the cam head, which moves the sliding punch to set the flange to the 10.3 mm
(0.406 in.) dimension and a 90° angle. Cam-actuated sliding punches on each side of the forming punch can be used for
setting flanges on channel and U-shape parts.
Cam-actuated dies are often used in combination with
other tooling to produce complicated parts. When used
in tandem with a progressive die, a cam-actuated die
can significantly reduce the number of operations
needed to produce a part. A drawer front that
originally required nine separate operations (two
shearing, two notching, one piercing, one box-
forming, and three flanging) when using a press brake
was produced in only four separate operations (slitting
coil to width; notching, piercing, and cutting off in a
progressive die; box-forming in a second die; and
flanging the sides, top, and bottom in a cam-actuated
flanging die) with the incorporation of a cam-actuated
die.
Compound Flanging and Hemming Die. The
compound flanging and hemming die shown in Fig. 9
is unusual in having no horizontal motion of punches
or dies. There are two cushions: a spring-loaded hold-
down plate and an air cushion for the die plate. As the
ram descends, the hold-down makes first contact,
clamping the piece securely to the die. As the ram
continues to descend, the springs compress, and the
angled flange is formed between the angled face of the bending punch and the die plate.
Fig. 8 Cam-
actuated single flanging die used for producing
a multiflanged part. See text for description of operation.
Dimensions given in inches.