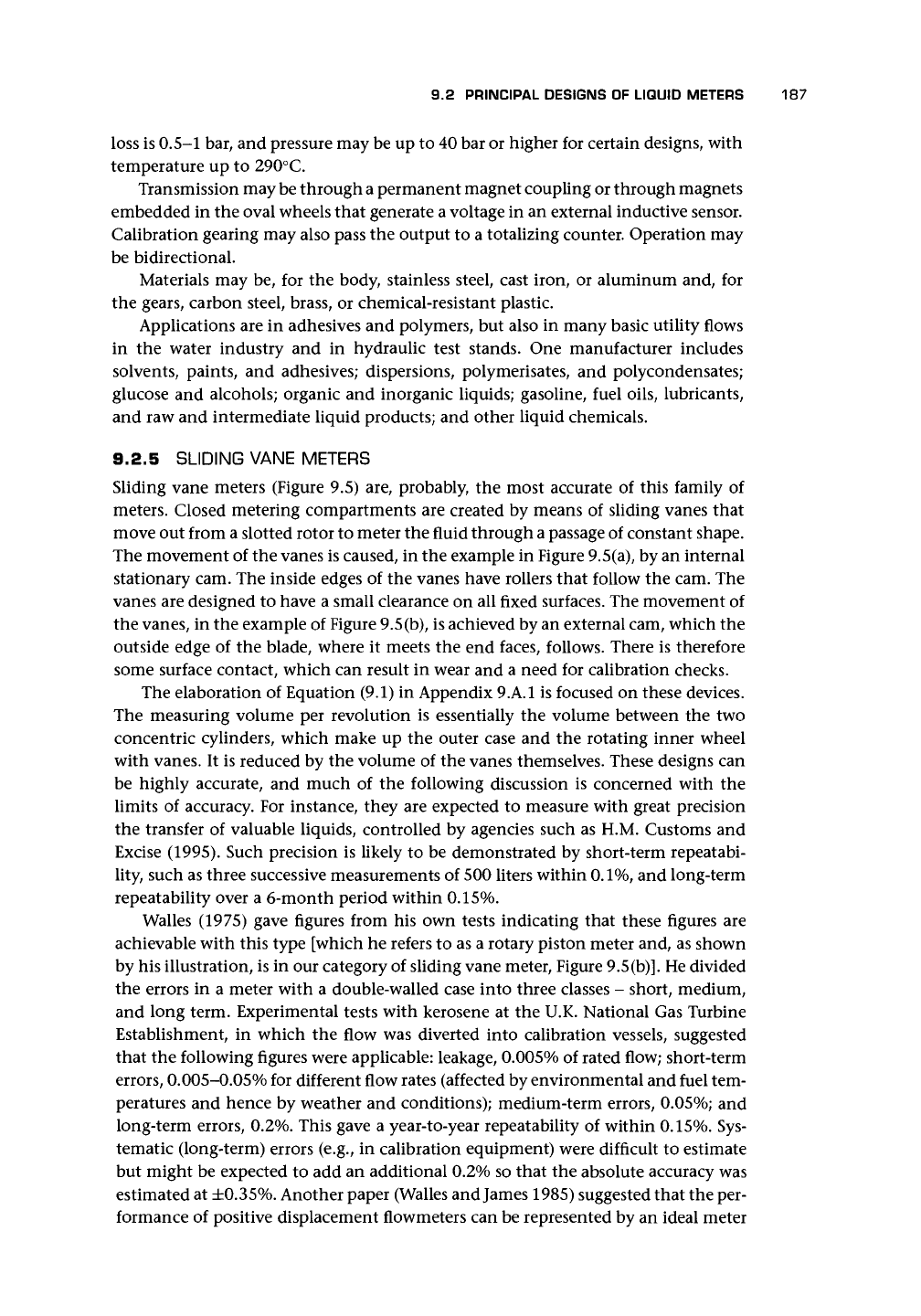
9.2 PRINCIPAL DESIGNS OF LIQUID METERS 187
loss is 0.5-1 bar, and pressure may be up to 40 bar or higher for certain designs, with
temperature up to 290°C.
Transmission may be through a permanent magnet coupling or through magnets
embedded in the oval wheels that generate a voltage in an external inductive sensor.
Calibration gearing may also pass the output to a totalizing counter. Operation may
be bidirectional.
Materials may be, for the body, stainless steel, cast iron, or aluminum and, for
the gears, carbon steel, brass, or chemical-resistant plastic.
Applications are in adhesives and polymers, but also in many basic utility flows
in the water industry and in hydraulic test stands. One manufacturer includes
solvents, paints, and adhesives; dispersions, polymerisates, and polycondensates;
glucose and alcohols; organic and inorganic liquids; gasoline, fuel oils, lubricants,
and raw and intermediate liquid products; and other liquid chemicals.
9.2.5 SLIDING VANE METERS
Sliding vane meters (Figure 9.5) are, probably, the most accurate of this family of
meters. Closed metering compartments are created by means of sliding vanes that
move out from a slotted rotor to meter the fluid through a passage of constant shape.
The movement of the vanes is caused, in the example in Figure 9.5(a), by an internal
stationary cam. The inside edges of the vanes have rollers that follow the cam. The
vanes are designed to have a small clearance on all fixed surfaces. The movement of
the vanes, in the example of Figure 9.5(b), is achieved by an external cam, which the
outside edge of the blade, where it meets the end faces, follows. There is therefore
some surface contact, which can result in wear and a need for calibration checks.
The elaboration of Equation (9.1) in Appendix 9.A.I is focused on these devices.
The measuring volume per revolution is essentially the volume between the two
concentric cylinders, which make up the outer case and the rotating inner wheel
with vanes. It is reduced by the volume of the vanes themselves. These designs can
be highly accurate, and much of the following discussion is concerned with the
limits of accuracy. For instance, they are expected to measure with great precision
the transfer of valuable liquids, controlled by agencies such as H.M. Customs and
Excise (1995). Such precision is likely to be demonstrated by short-term repeatabi-
lity, such as three successive measurements of 500 liters within
0.1%,
and long-term
repeatability over a 6-month period within 0.15%.
Walles (1975) gave figures from his own tests indicating that these figures are
achievable with this type [which he refers to as a rotary piston meter and, as shown
by his illustration, is in our category of sliding vane meter, Figure 9.5(b)]. He divided
the errors in a meter with a double-walled case into three classes - short, medium,
and long term. Experimental tests with kerosene at the U.K. National Gas Turbine
Establishment, in which the flow was diverted into calibration vessels, suggested
that the following figures were applicable: leakage, 0.005% of rated flow; short-term
errors,
0.005-0.05% for different flow rates (affected by environmental and fuel tem-
peratures and hence by weather and conditions); medium-term errors, 0.05%; and
long-term errors, 0.2%. This gave a year-to-year repeatability of within 0.15%. Sys-
tematic (long-term) errors (e.g., in calibration equipment) were difficult to estimate
but might be expected to add an additional 0.2% so that the absolute accuracy was
estimated at ±0.35%. Another paper (Walles and James 1985) suggested that the per-
formance of positive displacement flowmeters can be represented by an ideal meter