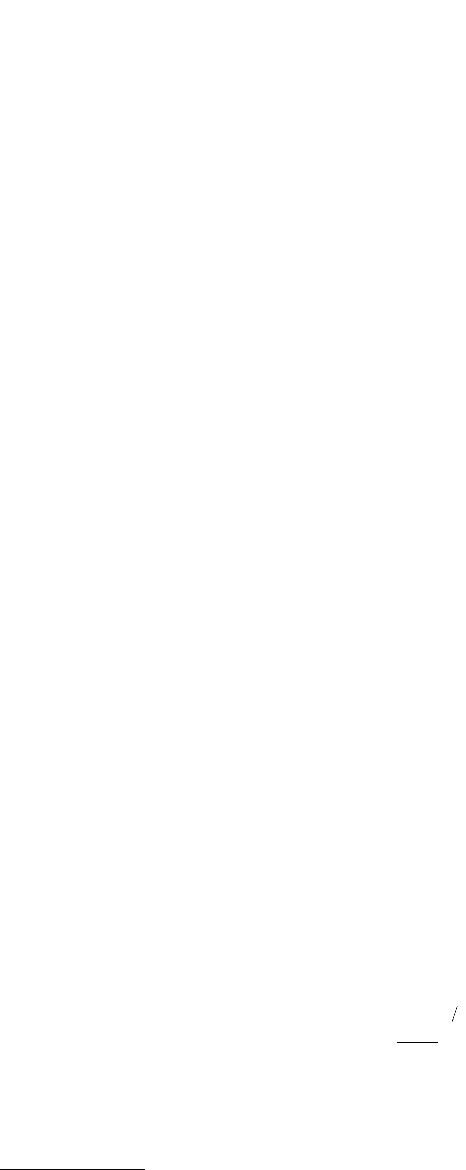
© 1999 by CRC Press LLC
used in the fit. Oliver and Pharr (1992) proposed a new procedure. They found that the entire unloading
data are well described by a simple power law relation
(10.7)
where the constants B and m are determined by a least-square fit. The initial unloading slope is then
found analytically, differentiating this expression and evaluating the derivative at the maximum load and
maximum depth. As we have pointed out earlier, unloading data used for the calculations should be
obtained after several loading/unloading cycles and with peak hold periods.
10.3.3 Determination of Load Frame Compliance
and Indenter Area Function
As stated earlier, measured displacements are the sum of the indentation depths in the specimen and the
displacements of suspending springs and the displacements associated with the measuring instruments,
referred to as load frame compliance. Therefore, to determine accurately the specimen depth, load frame
compliance must be known. This is especially important for large indentations made with high modulus
for which the load frame displacement can be a significant fraction of the total displacement. The exact
shape of the diamond indenter tip needs to be measured because hardness and Young’s modulus of
elasticity depend on the contact areas derived from measured depths. The tip gets blunt (Figure 10.22)
and its shape significantly affects the prediction of mechanical properties (Figures 10.23 through 10.25).
The method used in the past for determination of the area function has been to make a series of
indentations at various depths in materials in which the indenter displacement is predominantly plastic
and to measure the size of the indentations by direct imaging. Optical imaging cannot be used to measure
submicron-size impressions accurately. Because of the shallowness of the indent impressions, SEM results
in poor contrast.
A method consists of making two-stage carbon replicas of indentations in a soft material and imaging
them in the transmission electron microscope (TEM), was used initially by Pethica et al. (1983). Doerner
and Nix (1986) produced a series of indentations of varying size in annealed a–brass. Cellulose acetate
replicating tape was applied to the sample with a drop of acetone. Platinum with 20% palladium was
used as a shadowing agent. The indentations were oriented such that one side of the triangular perimeter
of each indentation was perpendicular to the shadowing direction. A shadowing angle of 19° was used.
Following shadowing, a carbon film was evaporated onto the replica and the cellulose acetate removed
by dissolving in acetone. Doerner and Nix then imaged the prepared replicas at zero tilt in the transmitted
electron mode in the TEM. The areas of the indentations were measured and compared to the contact
depths as measured using the nanoindenter. An example of the calibration curve is shown in
Figure 10.23a. We can clearly see that use of the ideal geometry results in a large overestimate of the
hardness and modulus at small depths since the indenter tip is considerably more blunt than the ideal
pyramid. A calibration curve of the type shown in Figure 10.23a is used to determine the effective
indentation depth, h
eff
. The effective indentation depth is the depth needed for a pyramid of ideal
geometry to obtain a projected contact area equivalent to that of a real pyramid. Since the projected area
of ideal geometry of a Berkovich indenter is 24.5 h
c
2
, the effective indentation depth can be obtained
from the following equation:
(10.8)
where the area is obtained from the shape calibration and the true contact depth (Doerner and Nix,
1986). It is observed that ideal geometry underestimates the contact area which leads to overestimation
WBhh
f
m
=−
()
h
eff
Area
24.5
=
12