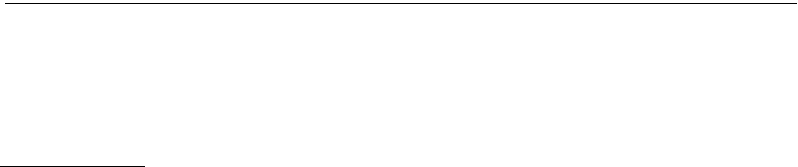
© 1999 by CRC Press LLC
16.2.2 Test Samples
Materials of most interest for planar fabrication processes using silicon as the structural material are
undoped and boron-doped (
p
+
-type) single-crystal silicon and phosphorus-doped (
n
+
-type) LPCVD
polysilicon films. For tribological reasons, silicon needs to be coated with a solid and/or liquid overcoat
or be surface treated, which exhibits low friction and wear.
Studies have been conducted on various types of virgin silicon samples: undoped (lightly doped)
single-crystal Si(100), Si(111), and Si(110) and the following types of treated/coated silicon samples:
PECVD-oxide-coated Si(111), dry-oxidized, wet-oxidized, and C
+
-implanted Si(111) (Bhushan and Ven-
katesan, 1993; Bhushan and Koinkar, 1994). Studies have also been conducted on heavily doped (
p
+
-type)
single-crystal Si(100), undoped polysilicon film, heavily doped (
n
+
-type) polysilicon film and 3C-SiC
(cubic or
β
-SiC) film (Bhushan et al., 1997a,b, 1998; Li and Bhushan, 1998; Sundararajan and Bhushan,
1998). A 10
×
10 mm coupon of each sample was ultrasonically cleaned in methanol for 20 min and
dried with a blast of dry air prior to measurements. The undoped Si(100) was a
p
-type material grown
by the CZ process. It had a boron concentration of 1.7
×
10
15
ions/cm
3
from intrinsic doping during the
manufacturing process. The doped wafer (
p
+
-type single-crystal silicon) was heavily doped with boron
ions (from a solid source of oxide of boron) with concentration of 7
×
10
19
ions/cm
3
down to a depth of
5.5 µm using thermal diffusion. The grain size of polysilicon wafer was about 5 mm. The polysilicon film
was produced as follows: (1) The substrate used was thermally oxidized Si(100) wafers with the oxide
layer grown using a standard wet oxidation recipe to a nominal thickness of about 100 nm; (2) the
polysilicon film was grown on the substrate using an LPCVD process (deposition temperature, 610°C;
silane flow rate, 285 sccm; deposition pressure, 230 mtorr), using the thermal decomposition of silane
vapor. The films were about 3 µm thick, with columnar grains and a grain size of about 750 nm. X-ray
diffraction and transmission electron microscope characterization showed the film to be highly oriented
(110). The
n
+
-doped polysilicon film was obtained by doping the polysilicon film with phosphorus ions
from a solid source of P
2
O
5
by thermal diffusion at 875°C for 90 min. The 3C-SiC films were grown
through an atmospheric pressure chemical vapor deposition (APCVD) process on an Si(100) substrate.
To grow the SiC film on the wafer by carbonizing its surface, the wafer is placed on an SiC-coated graphite
susceptor, which is induction-heated by an RF-generator to the growth temperature of 1360°C in the
presence of propane and silane at 1 atm. Prior to film growth, the wafer is heated to 1000°C in the
presence of hydrogen, which etches the native oxide from the wafer surface (Zorman et al., 1995). The
films obtained were about 2 µm thick. Both as-deposited and polished versions of the undoped polysilicon
and SiC films were studied. The polysilicon film was chemomechanically polished in a Struers Planopol-
3 polishing machine using 100 ml colloidal silica dispersion (Rippey Corporation, particle size of 30 to
100 nm) mixed in 2000 ml deionized water at a force of 210 N for 15 min, with the pads running at
150 rpm in the same direction. The SiC and doped polysilicon films were polished in a Buehler Ecomet-
3 polishing machine with diamond slurry (General Electric Company, particle size of 100 to 500 nm)
for 30 min for SiC and 12 min for doped polysilicon film at a load of 50 N, with the pads running at
10 rpm in the same direction. Doped polysilicon film was polished using Fuji film lapping tape, LT-2,
the main lapping agent being 37-µm-sized Cr
2
O
3
particles.
Boundary lubrication studies have been conducted on silicon samples coated with perfluoropolyether
lubricants (Koinkar and Bhushan, 1996a,b) and Langmuir–Blodgett and chemically grafted self-assem-
bled monolayer films (Bhushan et al., 1995b).
16.3 Results and Discussion
Reviews of five studies are presented in this section. The first study compares micro/nanotribological
properties of various forms of virgin, coated, and treated silicon samples. The second study is composed
of similar studies conducted on SiC film and compares this material to other materials currently used
in MEMS devices. The third study compares the macroscale friction and wear data of virgin, coated, and