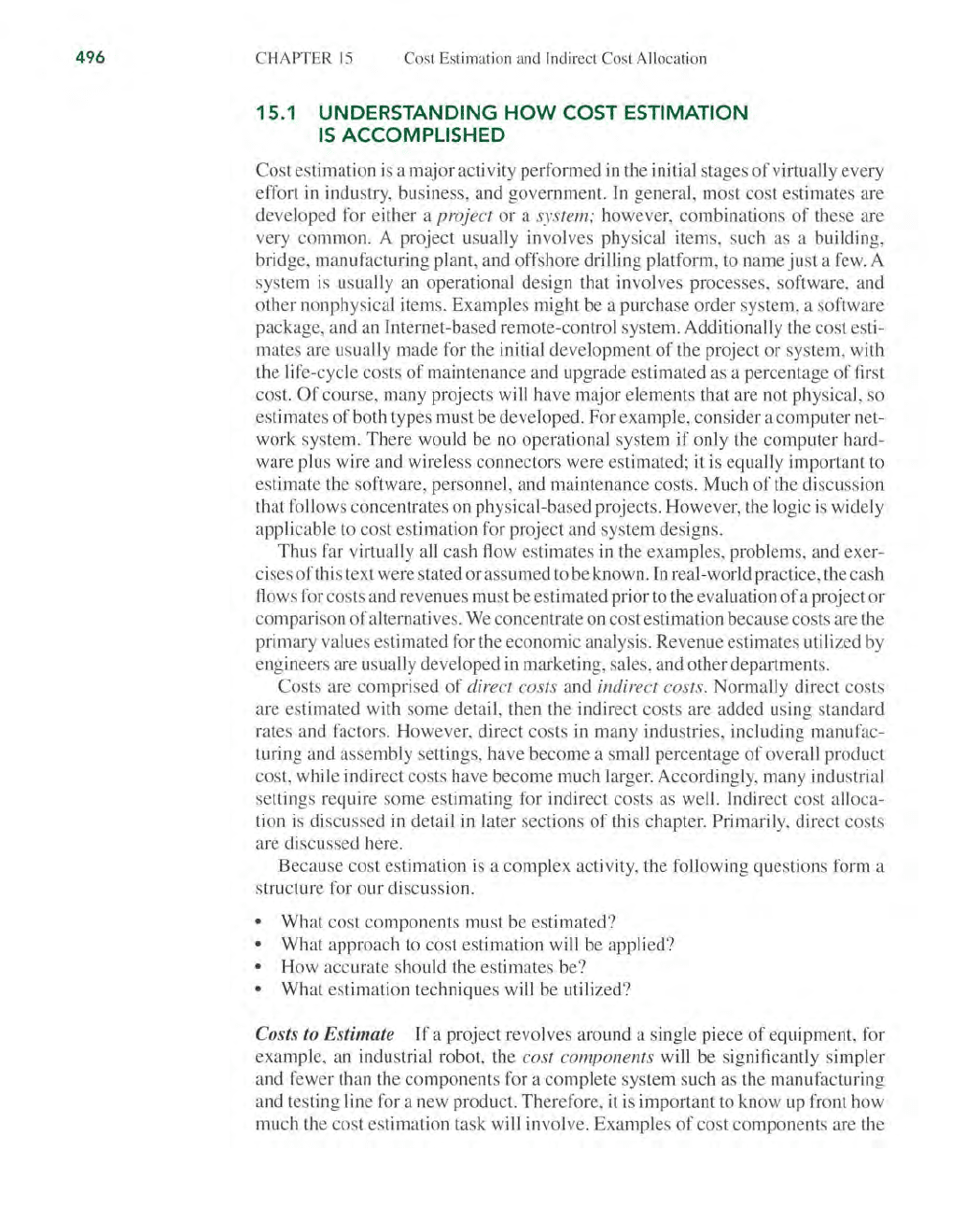
496
CHAPTER
15
Cost
Estimation and Indirect
Cost
Allocation
15.1 UNDERSTANDING
HOW
COST ESTIMATION
IS
ACCOMPLISHED
Cost estimation
is
a major activity performed
in
the initial stages
of
virtually every
effort
in
industry, business, and government.
In
general, most cost estimates are
developed for eith
er
a project
or
a system; however, combinations
of
these are
very common. A project usually involves physical items, such as a building,
bridge, manufacturing plant, and offshore drilling platform, to name
just
a few. A
system
is
usually an operational design that involves processes, software, and
other nonphysical items. Examples might be a purchase order system, a software
package, and an Internet-based remote-control system. Additionally the cost esti-
mates are usually made for the initial development
of
the project
or
system, with
the life-cycle costs
of
maintenance and upgrade estimated as a percentage
of
first
cost.
Of
course, many projects will have major elements that are not physical, so
esti mates
of
both types
must
be
developed.
For
example, consider a computer net-
work system.
There
would be no operational system
if
only the computer hard-
ware plus wire and wireless connectors were estimated; it is equally important to
estimate the software, personnel, and maintenance costs.
Much
of
the discussion
that follows concentrates on physical-based projects. However, the logic
is
widely
applicable to cost estimation for project and system designs.
Thus far virtually all cash flow estimates
in
the examples, problems, and exer-
cises
of
this text were stated
or
assumed to
beknown.
In
real-world practice, the cash
flows for costs and revenues must be estimated prior to the evaluation
of
a project
or
comparison
of
alternatives. We concentrate on cost estimation because costs are the
primary values estimated for the economic analysis. Revenue estimates utilized by
eng
in
eers are usually developed in marketing, sales, and other departments.
Costs are comprised
of
direct costs and indirect costs. Normally direct costs
are estimated with some detail, then the indirect costs are added using standard
rates and factors. However, direct costs in many industries, including manufac-
turing and assembly settings, have
become
a small percentage
of
overall product
cost, while indirect costs have become much larger. Accordingly, many industrial
settings require
some
estimating for indirect costs as well. Indirect cost alloca-
tion
is
discussed
in
detail in later sections
of
this chapter. Primarily, direct costs
are discussed here.
Because cost estimation is a complex activity, the following questions form a
structure for
our
discussion.
•
•
•
What cost components must be estimated?
What approach to cost estimation will be applied?
How accurate should the estimates be?
What
estimation techniques will be utilized?
Costs to Estimate
If
a project revolves around a single piece
of
equipment, for
example, an industrial robot, the cost components will be signifi
cant
ly
simpler
and fewer than the
co
mponents for a complete system such as the manufacturing
a
nd
testing line for a new product. Therefore, it
is
important to know up front how
much the cost estima
ti
on task will involve. Examples
of
cost components are the