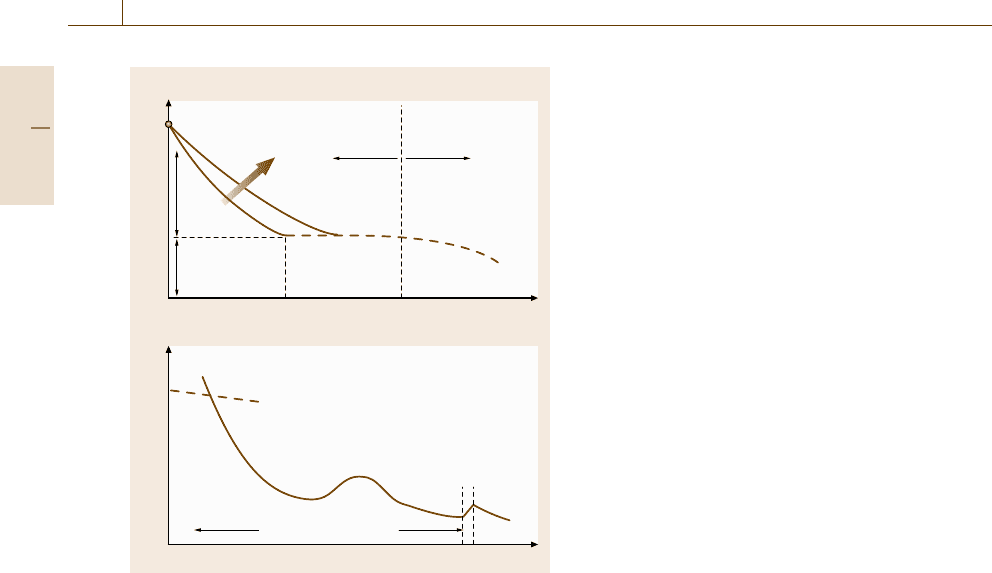
402 Part C Materials Properties Measurement
a)
b)
Relative flow stress σ/E
Flow stress
Twinning
Phase transformation
Ferrite / pearlite
Austenite
Temperature
Dynamic strain
aging
σ
c
/E
Increase in
strain rate
Low temperature
deformation
Thermal
component
Athermal
component
High temperature
deformation
0
0
T
c
/T
m
Relative temperature T/T
m
α–γ
Fig. 7.62a,b Effect of temperature on the yield strength
(schematic illustration): (a) general case and (b) mild steel
the curves for body-centered cubic (BCC, ferrite) is
interrupted by a face-centered cubic (FCC, austenite)
regime. Depending on the temperature and strain rate,
various deformation mechanisms become dominant.
Taking a look at the map near room temperature with
a strain rate of 10
0
–10
−5
s
−1
, the dominant mechanism
is slip, i. e. dislocation motion. A simpler illustration to
explain the effect of temperature on the yield strength
isgiveninFig.7.62. At 0 K, the enhancement by ther-
mal activation disappears and the strength corresponds
to the theoretical strength. At a certain temperature,
the strength is decreased through due to thermal ac-
tivation of dislocation motion. At higher temperatures
near T
m
/2, all the short-range barriers for dislocation
motion can be overcome, but some long-range barriers
remain. The stresses related to overcoming these two
kinds of barriers are called thermal stress (or effective
stress) and athermal stress (internal stress), respectively.
Thus, as shown in Fig. 7.62a, thermal stress becomes
zero at T
0
.BelowT
0
the temperature dependence of the
yield strength is ascribed to thermal activation mech-
anisms for dislocation motion. Therefore, if the strain
rate is increased, its effect is equivalent to decreasing
temperature. The influence of strain rate on the yield
strength is also drawn schematically in Fig. 7.62a. Flow
stress can also be discussed using this approach, al-
though the evolution of the dislocation structure must
also be taken into account. With increasing of plastic
strain, the dislocation density (ρ) increases by ρ
+
and
then workhardening occurs. At the same time, dislo-
cations are annihilated with recovery to be decreased
by ρ
−
, which is influenced by temperature. Therefore,
the total dislocation density (ρ
+
+ρ
−
) is determined as
a function of the strain as well as temperature and time,
i. e., strain rate. The flow curve obtained at high strain
rate is therefore influenced by two thermal activation
mechanisms: dislocation motion and dynamic recovery.
When the test temperature is higher than T
0
,the
microstructure itself changes obviously during de-
formation, for example exhibiting to grain growth,
dynamic recovery and/or recrystallization. Such a re-
gion, as shown in Fig. 7.62a, is called high-temperature
deformation. As observed in Fig.7.61, creep deforma-
tion occurs strongly at high temperatures with small
strain rates.
The behavior of a real material is compli-
cated in comparison with that of the pure metal
in Fig. 7.62a. The example of mild steel is pre-
sented in Fig. 7.62b[7.219]. The curve in the lower-
temperature region corresponds to the deformation
of the BCC ferrite phase, while that in the higher-
temperature region corresponds to FCC austenite.
Moreover, due to the intrusion of deformation twinning
at cryogenic temperatures and dynamic strain aging
caused by solute carbon and nitrogen atoms in the
region slightly above room temperature, the typical be-
havior explained in Fig. 7.62a is not easy to discern.
7.4.4 Strengthening Mechanisms
for Crystalline Materials
As described above, flow stress is controlled by the
motion of dislocations. Hence, there are two ways to
strengthen a material: remove dislocations thoroughly or
introduce a large number of obstacles to prevent disloca-
tion motion. The former approach has been achieved in
the form of single-crystal whiskers. When the diameter
of the whisker increases, the strength decreased rapidly
due to the inevitable introduction of defects including
dislocations. The latter approach has been used widely,
including solid-solution hardening, precipitation hard-
ening or dispersion particles hardening, workharden-
ing, grain-refinement hardening and the duplex structure
(composite) hardening. These mechanisms to prevent
dislocation motion are described below.
Part C 7.4