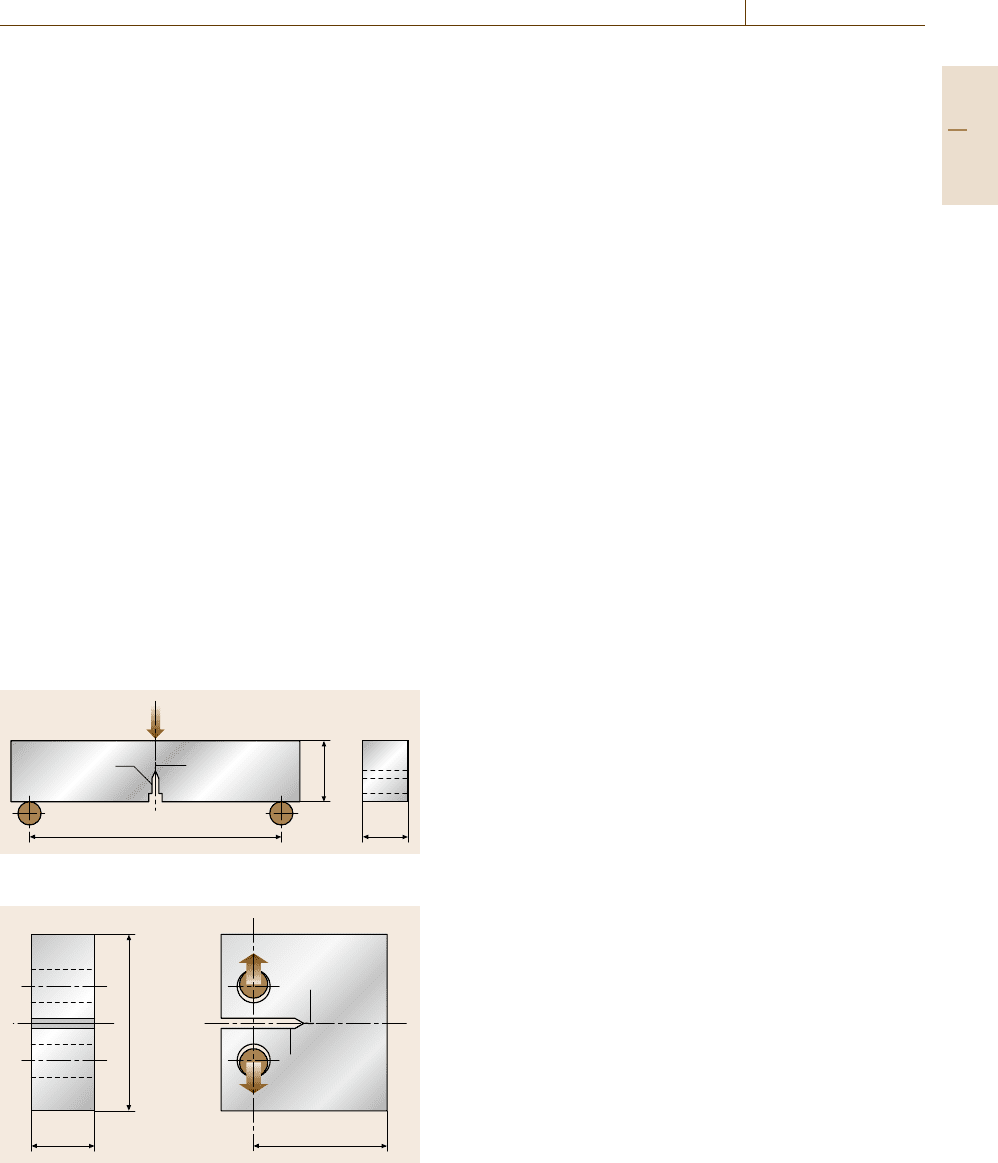
Mechanical Properties 7.5 Fracture Mechanics 411
CTOD criterion is also applied to evaluate the fracture
toughness under large-scale yielding. Historically, the
cleavage fracture toughness of structural steels has often
been evaluated in terms of the critical CTOD δ
c
.
In the standards for toughness testing, several spec-
ifications are prescribed so that the constraint effect
can be negligible. Single-parameter fracture mechanics
breaks down in the presence of excessive plasticity, or
for specimens with too shallow a notch, and fracture
toughness depends on the size and geometry of the test
specimen.
K
Ic
Testing
The standard test methods for determining plane–strain
fracture toughness (K
Ic
) of metallic materials are spec-
ified in several standards [7.231, 238, 239]. In these
standards, ASTM E399-90 [7.231], which was origi-
nally published as E399-70, is widely used.
For the standard K
Ic
test, a single-edge notched
(SEN) bend specimen or a compact test (CT) spec-
imen is used; these standard geometries are shown
in Figs. 7.77 and 7.78, respectively. The standard
bend specimen has a rectangular cross section (B ×2B,
W =2B, where B is the specimen thickness and W is
the specimen width). Alternative a specimen geometry
with square cross section (B × B, W = B) can also be
used for the bend test. However, the size requirement for
Notch
Fatigue
precrack
S B
W
Fig. 7.77 Single-edge notched (SEN) bend specimen
Fatigue
precrack
Notch
1.2 W
B
W
Fig. 7.78 Compact test (CT) specimen
the plane–strain fracture toughness test, which will be
described later, should be satisfied. In the CT specimen,
W = 2B is recommended.
The fatigue precrack is introduced at the notch tip
by cyclic loading and the recommended value for the
total crack length (machined notch plus fatigue crack)
is 0.45–0.55W. The fatigue precracking load can af-
fect the fracture toughness results, so the cyclic loading
conditions are strictly limited. The stress ratio (min-
imum load to maximum load) of cyclic loading is
between −1and0.1. The maximum fatigue stress in-
tensity (K
max
) does not exceed 80% of the K
Ic
value of
the material. For the final stage of fatigue crack exten-
sion, K
max
must not exceed 60% of the K
Ic
value, and
the ratio of K
max
to the Young’s modulus of the material
K
max
/E should not exceed 0.00032 m
1/2
. Usually, the
number of cycles for fatigue precracking is 10
4
–10
6
.
Normally, as the temperatures of the fatigue cracking
and fracture toughness tests are different, the effect of
temperature should be taken into account. When fatigue
cracking is conducted at temperature T
1
and the frac-
ture testing at a different temperature, T
2
, K
max
must
not exceed 0.6(σ
ys1
/σ
ys2
)K
Ic
, where σ
ys1
and σ
ys2
are
the yield stress at the respective temperatures T
1
and T
2
.
It is recommended that the length of the fatigue crack be
larger than 1.3mmand2.5% of W for a straight-through
notch.
The single-edge notched specimen is loaded in
three-point bending with a support span S, which is nor-
mally equal to 4W,thatisS =4W. The bend testing
fixture is designed to minimize friction effects by allow-
ing the support rollers to rotate and move apart slightly
when the specimen is loaded. The compact specimen is
loaded in tension through pins by allowing the specimen
to rotate during the test.
Fracture tests are conducted with a static load-
ing with a rate of increase of stress intensity of
0.55–2.75 MPa m
1/2
. The test temperature is controlled
within 3
◦
C[7.237] and the specimen should be kept at
the test temperature for 1.2min/mm of specimen thick-
ness before testing [7.238]. During testing, continuous
measurement of load versus crack mouth opening dis-
placement is required. The displacement is measured
by a double-cantilever displacement gage or a ring-type
displacement gage.
After fracture testing, the crack length is measured
at the following three positions: at the crack front, and
midway between the center of the crack front and the
end of the crack front on each surface of the speci-
men. The average of these three measurements is the
crack length and is used to calculate the stress intensity.
Part C 7.5